Determining the sintering temperature for different materials involves a careful analysis of several factors, including the material's composition, particle size, desired final properties, and the sintering environment. The sintering temperature must be optimized to achieve the desired density, strength, and other mechanical properties while avoiding defects such as excessive grain growth or unwanted phase transformations. Key considerations include the material's melting point, the presence of a liquid phase, and the interaction between particles during the sintering process. By understanding these factors and conducting experimental trials, the optimal sintering temperature can be determined for each specific material.
Key Points Explained:
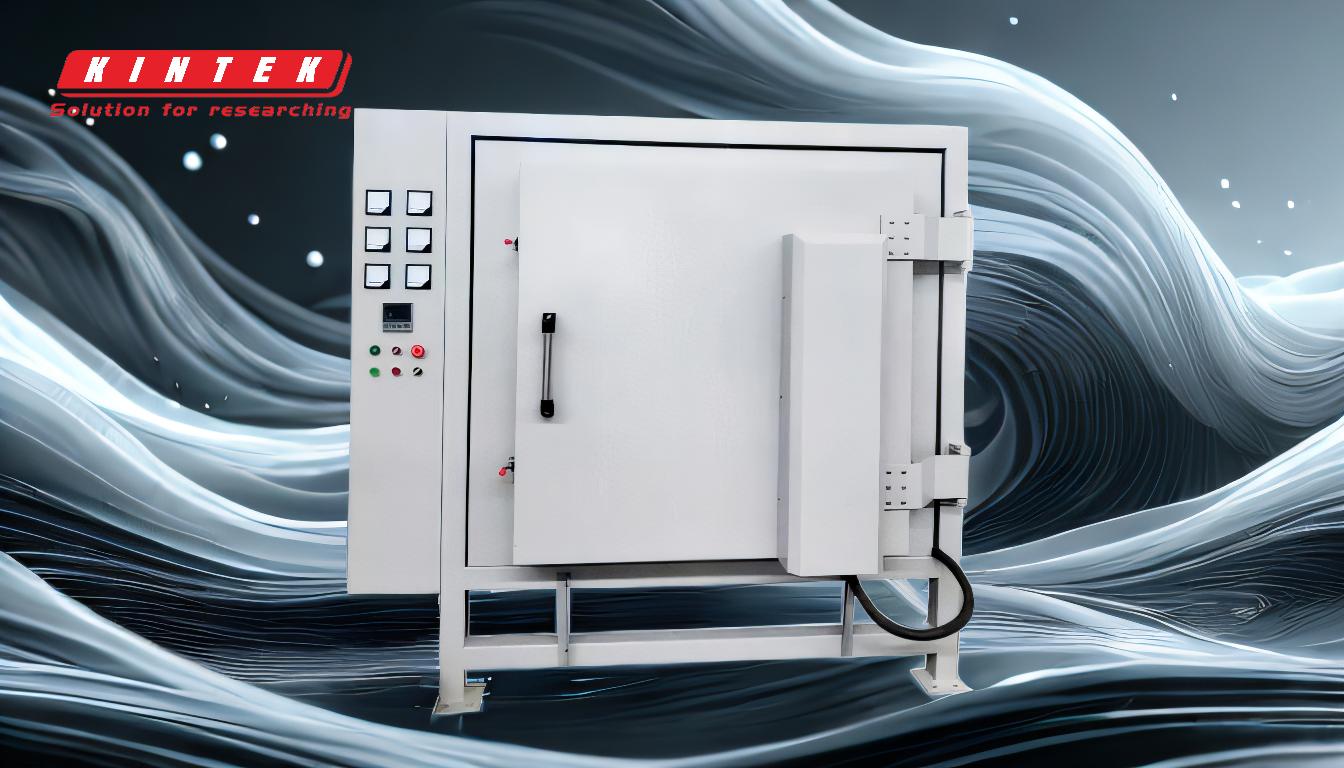
-
Material Composition and Properties:
- The composition of the material plays a critical role in determining the sintering temperature. Materials with different chemical compositions will have varying melting points and sintering behaviors.
- For example, ceramics and metals require different sintering temperatures due to their distinct thermal and chemical properties.
- The presence of additives or binders in the material can also influence the sintering temperature by altering the material's thermal behavior.
-
Particle Size and Distribution:
- Smaller particles have a higher surface area-to-volume ratio, which promotes faster densification at lower temperatures.
- Homogeneous particle size distribution ensures uniform sintering, reducing the risk of defects such as uneven densification or cracking.
- Finer powders generally require lower sintering temperatures compared to coarser powders.
-
Desired Final Properties:
- The required density, strength, and other mechanical properties of the final product influence the choice of sintering temperature.
- Higher sintering temperatures can increase tensile strength, bending fatigue strength, and impact energy, but they may also lead to excessive grain growth or phase transformations.
- The sintering temperature must be carefully balanced to achieve the desired properties without compromising the material's integrity.
-
Sintering Environment and Atmosphere:
- The sintering atmosphere (e.g., air, vacuum, or inert gases like argon or nitrogen) can significantly affect the sintering process.
- A controlled atmosphere prevents oxidation or contamination, which can alter the material's properties.
- The choice of atmosphere depends on the material's reactivity and the desired final properties.
-
Heating Rate and Cooling Rate:
- The heating rate affects the densification process, with slower heating rates allowing for more uniform temperature distribution and reduced thermal stresses.
- The cooling rate influences the microstructure of the sintered material, with slower cooling rates often resulting in larger grain sizes and potentially better mechanical properties.
-
Experimental Trials and Optimization:
- Determining the optimal sintering temperature often involves conducting experimental trials to evaluate the effects of different temperatures on the material's properties.
- These trials help identify the temperature range that provides the best balance between densification, mechanical properties, and microstructure.
- Advanced techniques such as differential thermal analysis (DTA) or thermogravimetric analysis (TGA) can be used to study the material's thermal behavior and guide the selection of sintering temperatures.
-
Role of Pressure in Sintering:
- Applied pressure during sintering can enhance particle rearrangement and eliminate porosity, leading to higher density and improved mechanical properties.
- Pressure-assisted sintering techniques, such as hot pressing or spark plasma sintering, allow for lower sintering temperatures compared to conventional methods.
-
Interaction Between Temperature and Other Parameters:
- The sintering temperature must be considered in conjunction with other parameters such as pressure, heating rate, and atmosphere to achieve the desired results.
- For example, higher temperatures may be required when sintering in a vacuum compared to an inert gas atmosphere due to differences in heat transfer and chemical reactions.
By carefully considering these factors and conducting systematic experiments, the optimal sintering temperature for different materials can be determined, ensuring the production of high-quality sintered products with the desired properties.
Summary Table:
Key Factors | Description |
---|---|
Material Composition | Chemical composition affects melting points and sintering behavior. |
Particle Size | Smaller particles enable faster densification at lower temperatures. |
Desired Final Properties | Balance temperature to achieve density, strength, and avoid defects. |
Sintering Environment | Atmosphere (air, vacuum, inert gases) influences sintering outcomes. |
Heating/Cooling Rates | Slower rates ensure uniform temperature distribution and better microstructure. |
Experimental Trials | Conduct trials to identify optimal temperature ranges for specific materials. |
Pressure in Sintering | Applied pressure enhances density and mechanical properties. |
Need help determining the optimal sintering temperature for your materials? Contact our experts today for personalized guidance!