Physical Vapor Deposition (PVD) coating is a sophisticated process used to apply thin, durable, and highly adherent coatings to various substrates. The process involves creating a high-vacuum environment, vaporizing a target material, and depositing it onto a substrate to form a protective or functional layer. PVD coatings are widely used in industries like aerospace, automotive, and electronics due to their exceptional hardness, wear resistance, and corrosion protection. The process typically involves steps such as vaporization, transportation, reaction, and deposition, with techniques like sputtering and thermal evaporation being commonly employed.
Key Points Explained:
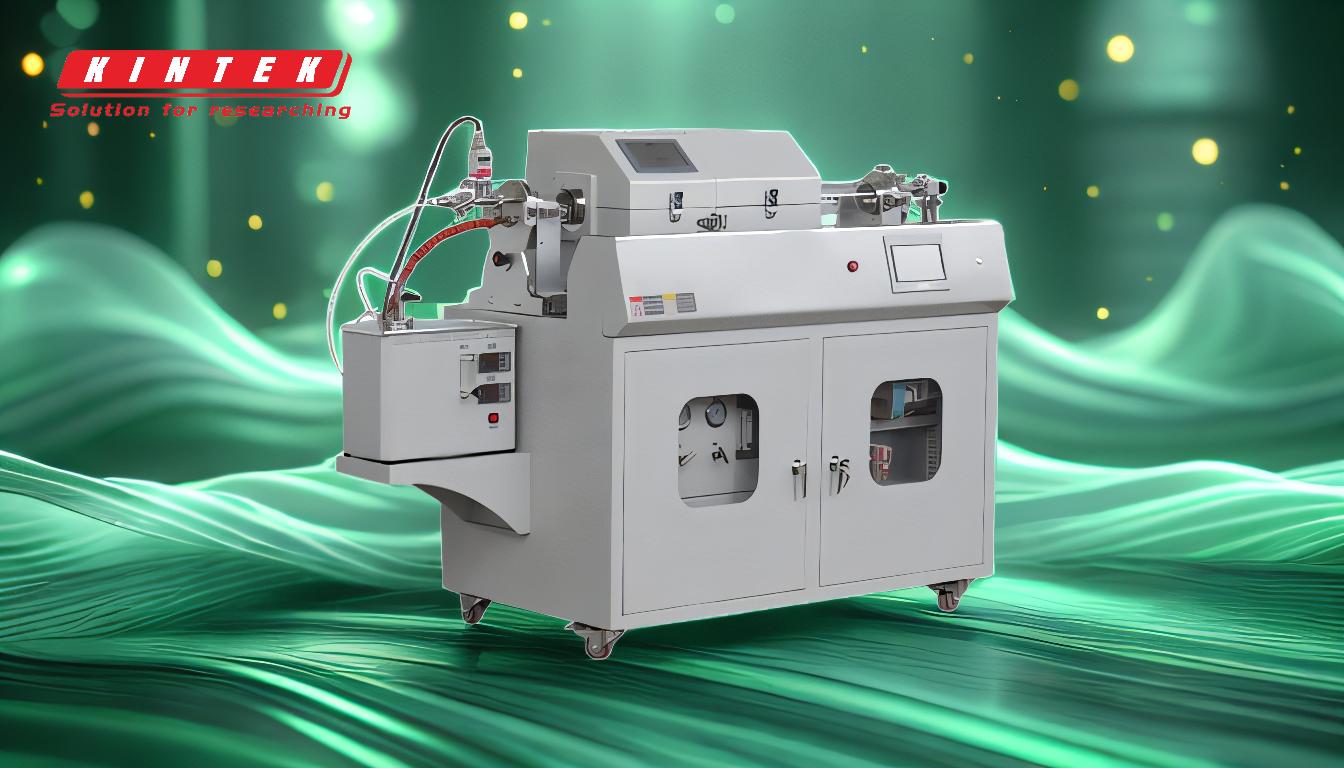
-
Preparation of the Vacuum Chamber:
- The PVD process begins by placing the target material (the material to be coated) and the substrate (the material to be coated onto) inside a vacuum chamber.
- The chamber is then evacuated to create a high-vacuum environment, typically at pressures ranging from 10^-2 to 10^-6 Torr, which approximates the conditions of outer space.
- This vacuum environment is crucial to prevent contamination and ensure the purity of the coating.
-
Vaporization of the Target Material:
- The target material is vaporized using high-energy sources such as electron beams, ions, or photons. This step is known as evaporation.
- In techniques like sputtering, the target material is bombarded with high-energy ions (often Argon ions) to dislodge atoms from the target surface, creating a plasma of atoms or molecules.
- In thermal evaporation, the target material is heated to a high temperature until it vaporizes.
-
Transportation of Vaporized Material:
- The vaporized atoms or molecules are then transported through the vacuum chamber towards the substrate.
- This transportation occurs in a chemically inert atmosphere, often created using inert gases like Argon, to prevent unwanted chemical reactions during the process.
-
Reaction (Optional):
- Depending on the desired properties of the coating, the vaporized material may react with selected gases (such as nitrogen, oxygen, or methane) to form compounds like metal oxides, nitrides, or carbides.
- This reaction step determines key properties of the coating, such as hardness, color, and chemical resistance.
-
Deposition on the Substrate:
- The vaporized material condenses onto the substrate, forming a thin, uniform film that bonds strongly to the surface.
- The deposition process is carefully controlled to ensure the desired thickness and uniformity of the coating, typically in the range of a few microns.
- The result is a highly adherent coating that interpenetrates with the underlying material, preventing issues like flaking or chipping.
-
Purging and Cooling:
- After the deposition is complete, the chamber is purged with inert gas to remove any residual vapors.
- The coated substrate is then allowed to cool before being removed from the chamber.
-
Techniques Used in PVD Coating:
- Sputtering: A widely used PVD technique where high-energy ions bombard the target material, causing atoms to be ejected and deposited onto the substrate.
- Thermal Evaporation: Involves heating the target material until it vaporizes, with the vapor then condensing onto the substrate.
- Arc Vapor Deposition: Uses an electric arc to vaporize the target material, often used for hard coatings like titanium nitride.
-
Applications and Benefits of PVD Coatings:
- PVD coatings are used in a variety of applications, including cutting tools, medical devices, and decorative finishes.
- The coatings provide excellent wear resistance, corrosion protection, and aesthetic appeal.
- The process is environmentally friendly, as it does not involve harmful chemicals or produce significant waste.
By following these steps, PVD coating creates a durable, high-performance layer that enhances the properties of the substrate, making it suitable for demanding applications across multiple industries.
Summary Table:
Step | Description |
---|---|
1. Preparation | Target material and substrate are placed in a high-vacuum chamber. |
2. Vaporization | Target material is vaporized using high-energy sources like electron beams. |
3. Transportation | Vaporized atoms are transported through an inert gas atmosphere. |
4. Reaction (Optional) | Vaporized material reacts with gases to form compounds like nitrides or oxides. |
5. Deposition | Vapor condenses onto the substrate, forming a thin, uniform coating. |
6. Purging & Cooling | Chamber is purged, and the coated substrate is cooled. |
7. Techniques | Sputtering, thermal evaporation, and arc vapor deposition are commonly used. |
8. Applications | Used in cutting tools, medical devices, and decorative finishes. |
Interested in enhancing your materials with PVD coatings? Contact our experts today to learn more!