Reactivating carbon involves a series of steps designed to restore the adsorption capacity of spent activated carbon. This process typically includes heating the carbon in an oxygen-free environment, desorbing contaminants, and thermally purifying the material to ensure it can be reused effectively. The goal is to remove adsorbed impurities and restore the carbon's porous structure, making it ready for reuse in various applications such as water purification, air filtration, and chemical processing.
Key Points Explained:
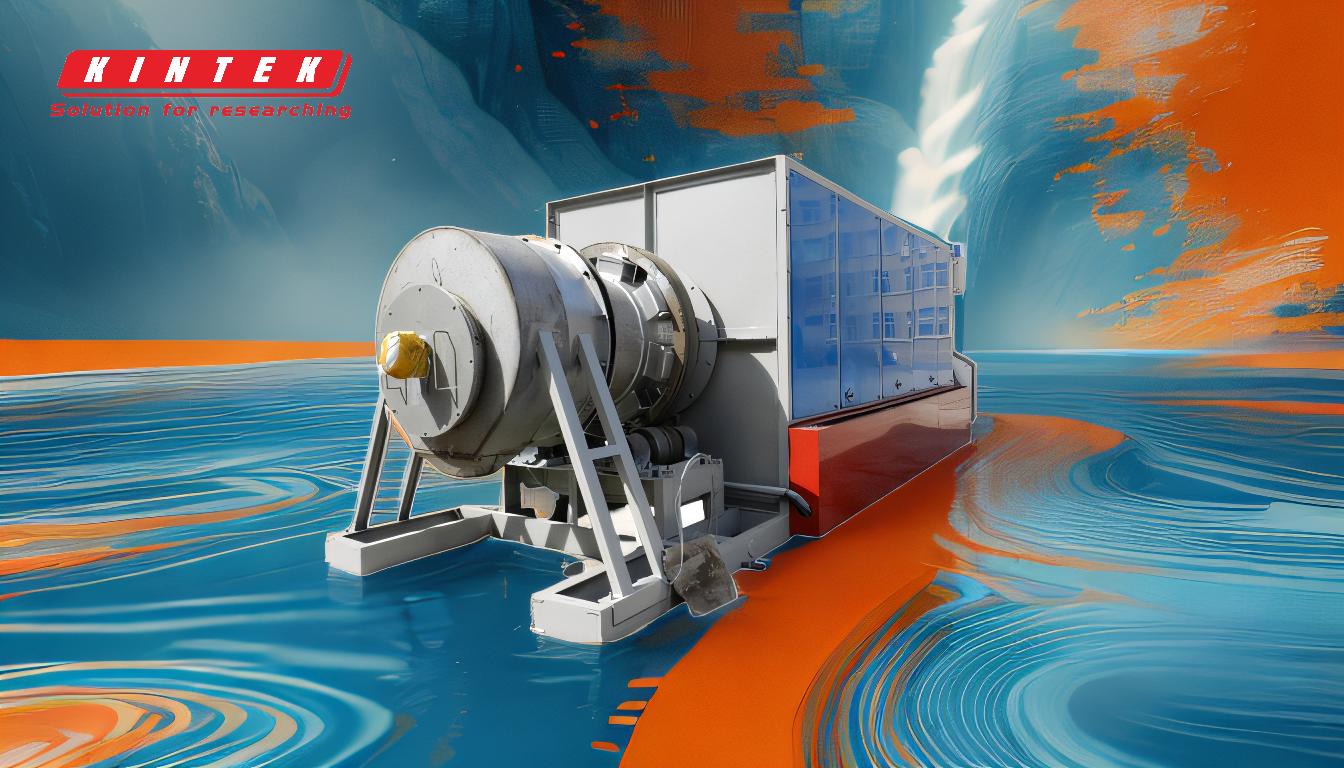
-
Thermal Phase:
- The reactivation process begins with heating the spent activated carbon in oxygen-free furnaces. This is crucial to prevent combustion of the carbon material.
- Steam is used as a selective oxidizer during this phase. It helps in breaking down and removing organic contaminants adsorbed on the carbon surface without damaging the carbon structure.
-
Desorption of Contaminants:
- During the heating process, contaminants adsorbed on the carbon surface are desorbed. This means they are released from the carbon and vaporized due to the high temperatures.
- The desorption process ensures that the pores of the activated carbon are cleared of impurities, which is essential for restoring its adsorption capacity.
-
Post-Combustion:
- After desorption, any remaining volatile organic compounds (VOCs) or other contaminants are typically oxidized in a post-combustion chamber.
- This step ensures that the contaminants are completely destroyed and do not escape into the environment, making the process environmentally friendly.
-
Thermal Purification:
- The carbon is further subjected to high temperatures to ensure that all residual contaminants are removed.
- This step also helps in restoring the carbon's microporous structure, which is essential for its adsorption efficiency.
-
Restoration of Adsorption Capacity:
- The final step involves cooling the reactivated carbon and ensuring that its adsorption capacity is fully restored.
- The reactivated carbon is now ready for reuse in various applications, offering a cost-effective and sustainable alternative to using new activated carbon.
By following these steps, the reactivation process not only extends the life of activated carbon but also reduces waste and environmental impact, making it a sustainable solution for industries that rely on activated carbon for purification and filtration processes.
Summary Table:
Step | Description |
---|---|
Thermal Phase | Heat spent carbon in oxygen-free furnaces; use steam to remove organic contaminants. |
Desorption | Release and vaporize adsorbed contaminants at high temperatures. |
Post-Combustion | Oxidize remaining VOCs in a post-combustion chamber for environmental safety. |
Thermal Purification | Further heat to remove residual contaminants and restore microporous structure. |
Restoration | Cool reactivated carbon and ensure full adsorption capacity restoration. |
Discover how reactivated carbon can enhance your sustainability efforts—contact us today!