Using a press mold for ceramics involves a series of steps that ensure the clay is evenly compressed into the desired shape. This method is efficient and allows for the production of uniform ceramic products, such as tiles, bricks, and other items, without the need for traditional kiln firing. The process leverages hydraulic presses or semi-isostatic pressing techniques to apply consistent pressure, ensuring the final product has good mechanical performance and dimensional accuracy. Below is a detailed explanation of how to use a press mold for ceramics, including key points and considerations for achieving optimal results.
Key Points Explained:
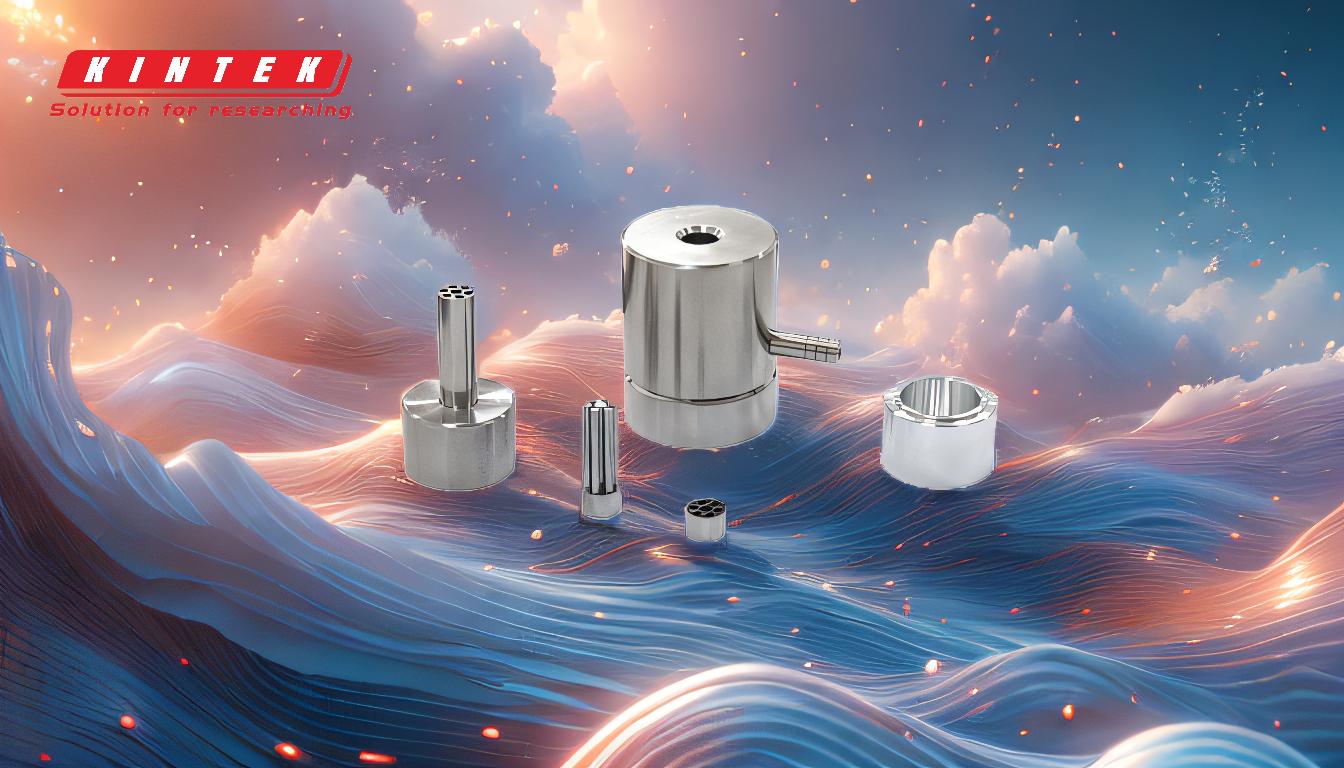
-
Understanding Press Molds for Ceramics
- Press molds are typically made from bisque clay (clay fired at 960-1000℃) or plaster. These materials are chosen for their durability and ability to hold shape under pressure.
- The mold is designed to create a geometrically defined shape, which is essential for producing consistent ceramic products.
-
Preparing the Clay
- Start with fresh clay that is pliable and free of air bubbles. Knead the clay thoroughly to ensure even consistency.
- Roll the clay into a slab of uniform thickness, ensuring it is large enough to cover the entire mold.
-
Lining the Mold with Clay
- Place the slab of clay onto the mold, ensuring it covers all areas evenly. Use your hands to gently press the clay into the mold, starting from the center and working outward to avoid trapping air.
- Pay attention to corners and intricate details to ensure the clay fully conforms to the mold's shape.
-
Applying Pressure
- Use your hands or a soft tool to press the clay gently and evenly into the mold. Avoid applying excessive force, as this can distort the shape or cause the clay to tear.
- For industrial applications, hydraulic presses are used to apply consistent pressure. This ensures uniformity and reduces the risk of defects.
-
Allowing the Clay to Firm Up
- Once the clay is pressed into the mold, allow it to firm up slightly before attempting to remove it. This ensures the clay retains its shape and does not deform during demolding.
- The drying time will depend on the type of clay and the ambient conditions.
-
Demolding the Ceramic Piece
- Carefully remove the clay from the mold once it has firmed up. Start by gently loosening the edges and then lifting the piece out of the mold.
- Inspect the piece for any imperfections or air pockets that may need to be smoothed out.
-
Post-Processing
- After demolding, allow the ceramic piece to dry completely before further processing, such as trimming or decorating.
- For industrial applications, the piece may undergo additional pressing or firing processes to achieve the desired strength and finish.
-
Advantages of Using Press Molds
- Uniformity: Press molds ensure consistent shapes and dimensions, which is critical for mass production.
- Efficiency: Hydraulic presses and semi-isostatic pressing techniques reduce production time compared to traditional kiln firing.
- Versatility: Press molds can be used to create a wide range of ceramic products, from tiles to complex shapes.
-
Considerations for Optimal Results
- Mold Maintenance: Regularly inspect and clean molds to prevent buildup of clay residue, which can affect the quality of the final product.
- Clay Consistency: Ensure the clay is properly prepared and free of air bubbles to avoid defects in the finished piece.
- Pressure Control: In industrial settings, monitor the pressure applied during pressing to prevent over-compression or under-compression.
By following these steps and considerations, you can effectively use a press mold for ceramics to produce high-quality, uniform products. Whether you are working on a small scale or in an industrial setting, understanding the process and its nuances is key to achieving successful results.
Summary Table:
Step | Key Details |
---|---|
Understanding Press Molds | Made from bisque clay or plaster for durability and shape retention. |
Preparing the Clay | Use fresh, pliable clay; knead and roll into a uniform slab. |
Lining the Mold | Press clay evenly into the mold, starting from the center. |
Applying Pressure | Use hands or hydraulic presses for consistent pressure. |
Allowing Clay to Firm Up | Let clay firm up before demolding to retain shape. |
Demolding | Gently remove the piece and inspect for imperfections. |
Post-Processing | Dry completely before trimming or decorating; additional pressing for strength. |
Advantages | Uniformity, efficiency, and versatility in production. |
Considerations | Mold maintenance, clay consistency, and pressure control are critical. |
Ready to elevate your ceramic production? Contact us today for expert guidance and solutions!