A three-stage furnace operates at three distinct levels of heating capacity, typically 40%, 65%, and 100% of its full capacity. This allows for more precise temperature control and energy efficiency compared to single-stage furnaces. The furnace uses electric heating elements or resistance heating to generate heat, which is then distributed evenly within the furnace chamber. By adjusting the heating stages and maintaining a controlled atmosphere, the furnace minimizes material oxidation and ensures effective heating. This multi-stage operation is particularly useful for applications requiring varying levels of heat intensity, such as in industrial processes or advanced material treatments.
Key Points Explained:
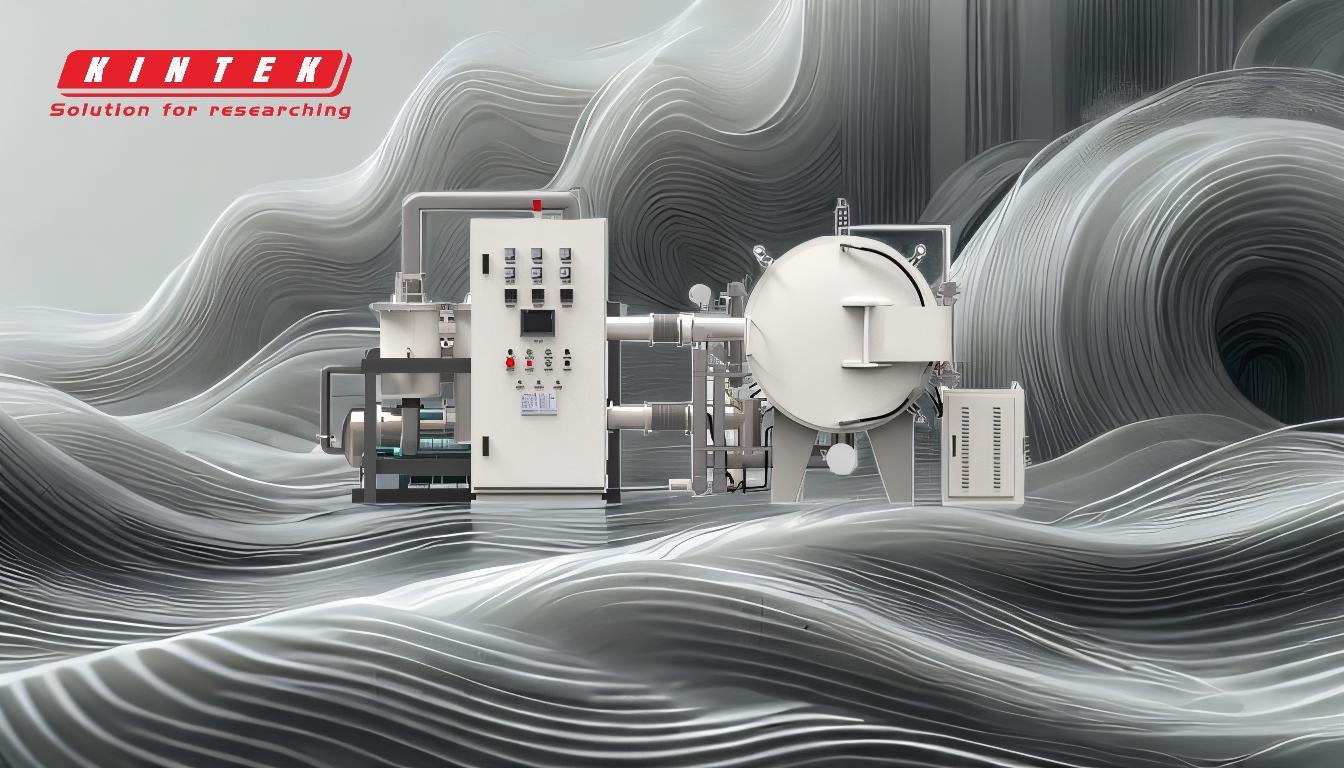
-
Three-Stage Operation:
- A three-stage furnace operates at three distinct levels of heating capacity: 40%, 65%, and 100% of its full capacity.
- This allows for more precise temperature control compared to single-stage furnaces, which only operate at full capacity.
- The intermediate stages (40% and 65%) are particularly useful for maintaining consistent temperatures during less demanding heating periods, improving energy efficiency.
-
Heating Mechanism:
- The furnace uses electric heating elements or resistance heating to generate heat.
- In a resistance furnace, electric current passes through a conductor, generating Joule heat, which is then used to heat the metal or materials inside the furnace.
- The heat is evenly distributed within the furnace chamber through radiation, ensuring uniform heating of the materials.
-
Atmosphere Control:
- The furnace maintains a controlled atmosphere to minimize oxidation and deterioration of materials during heating.
- By adjusting the atmosphere (e.g., introducing inert gases), the furnace prevents unwanted chemical reactions, ensuring the integrity of the materials being heated.
- This is particularly important in industrial processes where material properties must be preserved during heating.
-
Energy Efficiency:
- The three-stage operation allows the furnace to use only the necessary amount of energy for the required heating level.
- Instead of running at full capacity all the time, the furnace can operate at lower stages (40% or 65%) when less heat is needed, reducing energy consumption.
- This adaptability makes three-stage furnaces more energy-efficient compared to single-stage models.
-
Applications:
- Three-stage furnaces are ideal for applications requiring varying levels of heat intensity, such as heat treatment of metals, annealing, and other industrial processes.
- They are also used in advanced material treatments where precise temperature control and minimal oxidation are critical.
- The ability to switch between stages makes these furnaces versatile and suitable for a wide range of heating tasks.
-
Comparison with Modulating Furnaces:
- Unlike modulating furnaces, which can adjust their heating capacity in small increments, three-stage furnaces operate at fixed intermediate stages (40%, 65%, and 100%).
- While modulating furnaces offer finer control, three-stage furnaces provide a balance between precise temperature control and simpler operation.
- This makes three-stage furnaces a cost-effective alternative for applications where extremely fine adjustments are not necessary.
By combining these features, a three-stage furnace offers a versatile, energy-efficient, and precise heating solution for a variety of industrial and material processing applications.
Summary Table:
Feature | Description |
---|---|
Three-Stage Operation | Operates at 40%, 65%, and 100% capacity for precise temperature control. |
Heating Mechanism | Uses electric or resistance heating for uniform heat distribution. |
Atmosphere Control | Maintains a controlled atmosphere to minimize oxidation and material damage. |
Energy Efficiency | Reduces energy consumption by operating at lower stages when less heat is needed. |
Applications | Ideal for heat treatment, annealing, and advanced material processing. |
Comparison | Offers a balance between precise control and simplicity compared to modulating furnaces. |
Upgrade your industrial heating process with a three-stage furnace—contact us today to learn more!