A mesh belt furnace is a type of industrial furnace designed for heat treatment and thermo-chemical processing of small components. It operates by transporting workpieces on a mesh belt conveyor through various heating and cooling zones, ensuring uniform and repeatable results. The furnace is fully automated, with minimal manual intervention required, and offers advantages such as synchronized belt transport, efficient atmosphere distribution, and compliance with industry standards like AMS-2750 and CQI-9. Processes like carburizing, hardening, and tempering are commonly performed, making it suitable for applications requiring precise and consistent heat treatment.
Key Points Explained:
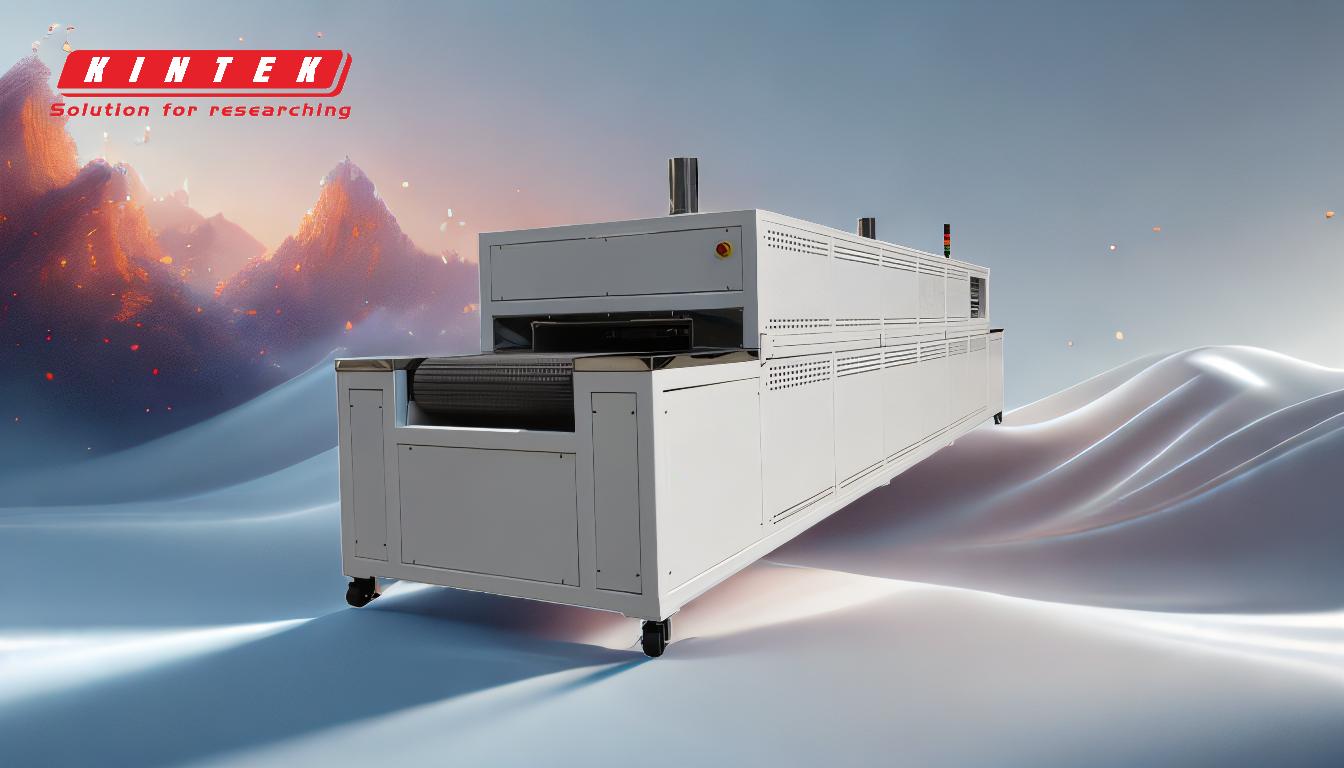
-
Loading and Conveyor System:
- Workpieces are loaded onto the mesh belt conveyor outside the furnace.
- The conveyor system transports the materials through the furnace's heating and cooling zones.
-
Heating Mechanism:
- The furnace is heated using burners, electric heating elements, or other heat sources.
- The temperature is precisely controlled to achieve the desired heat treatment results.
-
Automation and Control:
- The operation is fully automated, with a control system managing all processes.
- Manual tasks are limited to loading and unloading the workpieces.
-
Processes Performed:
- Common processes include carburizing, carbonitriding, hardening, and tempering.
- These processes are designed to enhance the mechanical properties of the materials.
-
Advantages of Mesh Belt Furnaces:
- Synchronized Belt Transport: Ensures smooth and consistent movement of materials.
- Long Muffle Service Life: Optimal design reduces wear and tear.
- Limited Contamination: Minimizes exposure to oil vapors and other contaminants.
- Efficient Atmosphere Distribution: Ensures uniform heat treatment.
- Efficient Quenching Oil Circulation: Reduces the risk of deformation in hardened objects.
- Low Energy Consumption: Designed for energy efficiency.
- Adaptability: Can be customized to meet specific plant conditions.
- Weekend Cycle Program: Includes stand-by modes for energy savings during non-operational periods.
- Compliance with Standards: Meets AMS-2750 and CQI-9 standards for quality and safety.
-
Applications and Flexibility:
- Suitable for a wide range of component sizes.
- Offers flexible processing capabilities, reducing the risk of component damage and mixing.
-
Repeatable and Homogeneous Results:
- Ensures consistent and uniform heat treatment across all workpieces.
- Ideal for applications requiring high precision and repeatability.
By understanding these key points, a purchaser can appreciate the efficiency, precision, and versatility of mesh belt furnaces, making them a valuable investment for industrial heat treatment processes.
Summary Table:
Feature | Description |
---|---|
Loading & Conveyor System | Workpieces are loaded onto a mesh belt conveyor, moving through heating/cooling zones. |
Heating Mechanism | Uses burners or electric elements for precise temperature control. |
Automation & Control | Fully automated operation with minimal manual intervention. |
Common Processes | Carburizing, hardening, tempering, and carbonitriding. |
Advantages | Synchronized belt transport, low energy consumption, compliance with AMS-2750/CQI-9. |
Applications | Suitable for small components, offering flexibility and repeatable results. |
Ready to enhance your heat treatment process? Contact us today to learn more about mesh belt furnaces!