Vacuum hardening is a specialized heat treatment process used to enhance the mechanical properties of metal components, such as strength, toughness, and resistance to wear and corrosion. This process is carried out in a vacuum hardening furnace, which operates under reduced atmospheric pressure to create a controlled environment. The absence of oxygen prevents oxidation and contamination, ensuring high-quality results. The process involves loading the components into the furnace, creating a vacuum, heating the parts to the desired temperature, and cooling them in a controlled manner, often using inert gases. This method is widely used in industries requiring precision and high-performance metal components.
Key Points Explained:
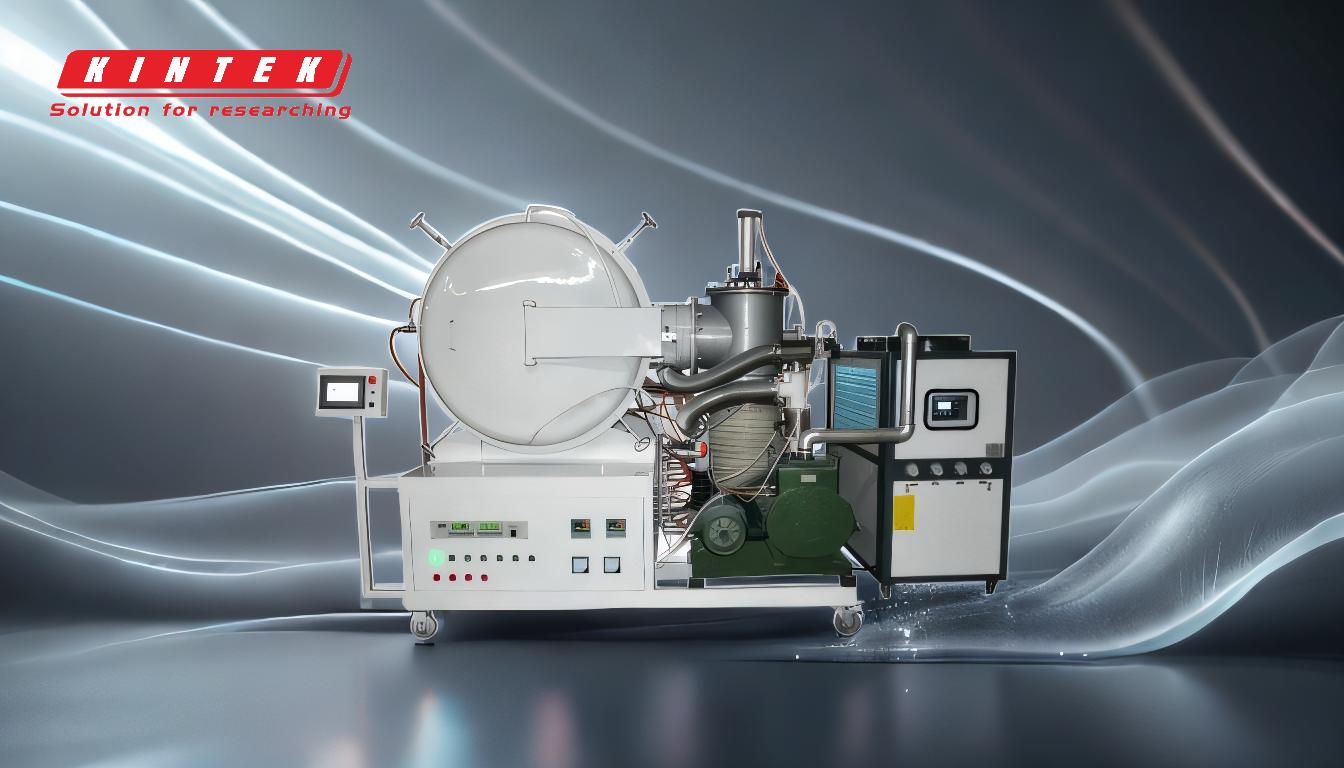
-
Purpose of Vacuum Hardening:
- Vacuum hardening is primarily used to improve the mechanical properties of metal components. It enhances hardness, strength, and resistance to wear and corrosion, making it ideal for high-performance applications in industries like aerospace, automotive, and tool manufacturing.
-
Role of the Vacuum Hardening Furnace:
- The furnace is the core equipment in this process. It operates under reduced atmospheric pressure, creating a vacuum environment that eliminates oxygen and other reactive gases. This prevents oxidation and contamination, ensuring the metal components remain clean and free from defects during the heat treatment process.
-
Key Steps in the Vacuum Hardening Process:
- Loading: The metal components are placed inside the furnace chamber.
- Vacuum Creation: A vacuum pump removes air and gases from the chamber, achieving a high level of vacuum.
- Heating: The furnace heats the components to the required temperature using precise temperature controls.
- Cooling: After heating, the components are cooled in a controlled manner, often using inert gases like argon or nitrogen to prevent oxidation and ensure uniform cooling.
-
Advantages of Vacuum Hardening:
- Oxidation Prevention: The vacuum environment eliminates oxygen, preventing oxidation and ensuring a clean surface finish.
- Controlled Atmosphere: The absence of reactive gases allows for precise control over the heat treatment process, resulting in consistent and high-quality outcomes.
- Improved Mechanical Properties: The process enhances hardness, strength, and durability, making it suitable for critical applications.
-
Applications of Vacuum Hardening:
- This process is widely used in industries that require high-performance metal components, such as:
- Aerospace: For turbine blades and other critical parts.
- Automotive: For gears, shafts, and engine components.
- Tool Manufacturing: For cutting tools, dies, and molds.
- This process is widely used in industries that require high-performance metal components, such as:
-
Safety and Operational Considerations:
- Vacuum hardening furnaces are complex and should only be operated by trained personnel. Proper maintenance and adherence to safety protocols are essential to ensure efficient and safe operation.
-
Comparison with Other Heat Treatment Methods:
- Unlike traditional methods like gas or oil quenching, vacuum hardening eliminates the risk of oxidation and contamination. It also provides better control over the heating and cooling processes, resulting in superior mechanical properties and surface quality.
By understanding these key points, purchasers of equipment and consumables can make informed decisions about investing in vacuum hardening technology and its associated components.
Summary Table:
Key Aspect | Details |
---|---|
Purpose | Improves hardness, strength, and wear resistance of metal components. |
Equipment | Vacuum hardening furnace operates under reduced atmospheric pressure. |
Process Steps | Loading → Vacuum creation → Heating → Controlled cooling with inert gases. |
Advantages | Prevents oxidation, ensures clean surface, and enhances mechanical properties. |
Applications | Aerospace, automotive, and tool manufacturing industries. |
Safety Considerations | Requires trained personnel and proper maintenance for safe operation. |
Interested in vacuum hardening for your metal components? Contact us today to learn more!