An atmospheric furnace is a specialized heating device designed to provide controlled heating in an environment where oxidation or other chemical reactions are minimized. It works by creating an inert atmosphere, typically using gases like nitrogen, to protect materials from oxidation during heating. The furnace operates by first removing air (creating a vacuum) and then introducing an inert gas. Heating is achieved through electric heating elements or gas burners, and the temperature and atmosphere are carefully controlled using advanced systems. This ensures uniform heating and prevents material degradation, making it ideal for applications like sintering, heat treatment, and other processes requiring precise environmental conditions.
Key Points Explained:
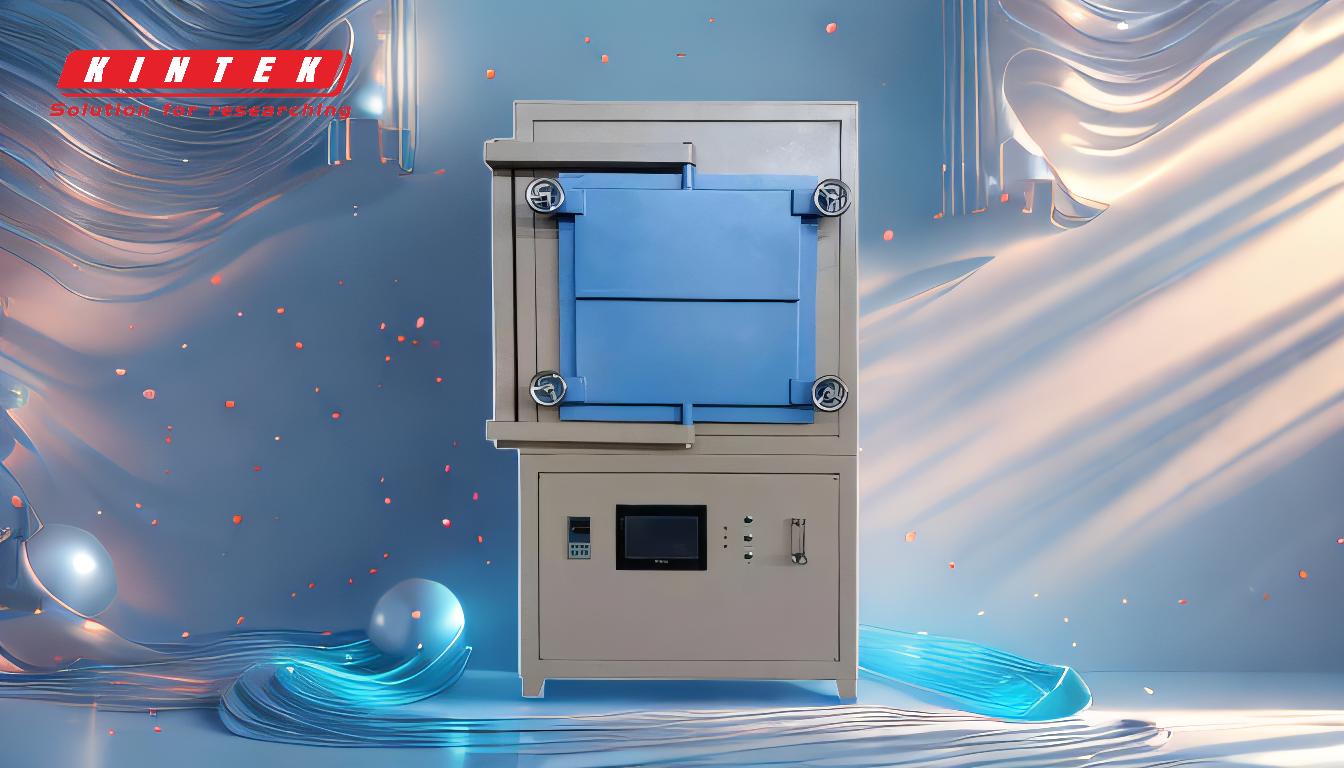
-
Purpose and Design of an Atmospheric Furnace:
- An atmospheric furnace is designed to heat materials in a controlled environment, preventing oxidation or other unwanted chemical reactions.
- It is fully sealed to maintain vacuum and gas pressure, ensuring no external air enters the chamber during operation.
- This makes it suitable for heat-treating materials that are sensitive to oxidation, such as metals and ceramics.
-
Key Components:
- Heating Chamber: Constructed with high-temperature-resistant materials to withstand extreme heat.
- Heating Elements: Electric resistance heaters or gas burners generate heat, which is evenly distributed through radiation.
- Temperature Control System: Includes sensors and controllers to monitor and regulate the furnace temperature.
- Gas Supply System: Introduces inert gases like nitrogen to create a controlled atmosphere.
- Atmosphere Control System: Maintains the desired gas composition within the furnace.
-
Operation Steps:
- Vacuum Creation: After loading the material and sealing the furnace, a vacuum pump removes air from the chamber to eliminate oxygen.
- Gas Purging: Once a vacuum is achieved, an inert gas (e.g., nitrogen) is introduced to create a protective atmosphere.
- Heating: The furnace begins heating using electric elements or gas burners, with the temperature carefully controlled to ensure uniform heating.
- Atmosphere Maintenance: The atmosphere control system continuously monitors and adjusts the gas composition to maintain optimal conditions.
-
Heating Mechanism:
- Heat is generated by electric heating elements or gas burners and distributed evenly through radiation.
- The controlled atmosphere minimizes oxidation and material degradation, ensuring effective and precise heating.
-
Applications:
- Used in processes like sintering, annealing, and heat treatment of metals and ceramics.
- Ideal for materials that require protection from oxidation or contamination during heating.
-
Advantages:
- Prevents oxidation and material degradation.
- Provides precise temperature and atmosphere control.
- Suitable for a wide range of industrial applications.
By understanding these key points, a purchaser can evaluate the suitability of an atmospheric furnace for their specific needs, ensuring optimal performance and material protection.
Summary Table:
Feature | Description |
---|---|
Purpose | Provides controlled heating to minimize oxidation and chemical reactions. |
Key Components | Heating chamber, heating elements, temperature control, gas supply, atmosphere control. |
Operation Steps | Vacuum creation, gas purging, heating, atmosphere maintenance. |
Heating Mechanism | Electric elements or gas burners distribute heat evenly through radiation. |
Applications | Sintering, annealing, heat treatment of metals and ceramics. |
Advantages | Prevents oxidation, precise temperature control, versatile industrial use. |
Discover how an atmospheric furnace can enhance your material processing—contact us today for expert advice!