Carbon coating is a process that involves depositing a thin layer of carbon onto a substrate to enhance its properties, such as surface chemical stability, structural stability, and Li-ion diffusion. This is achieved through thermal evaporation of carbon in a vacuum system, where a carbon source is heated to its evaporation temperature, allowing carbon to deposit onto the specimen. The process is widely used in applications like X-ray microanalysis and electron microscopy. Carbon coating not only improves material performance but also reduces costs by using minimal material. Below, we explore the key mechanisms and processes involved in carbon coating.
Key Points Explained:
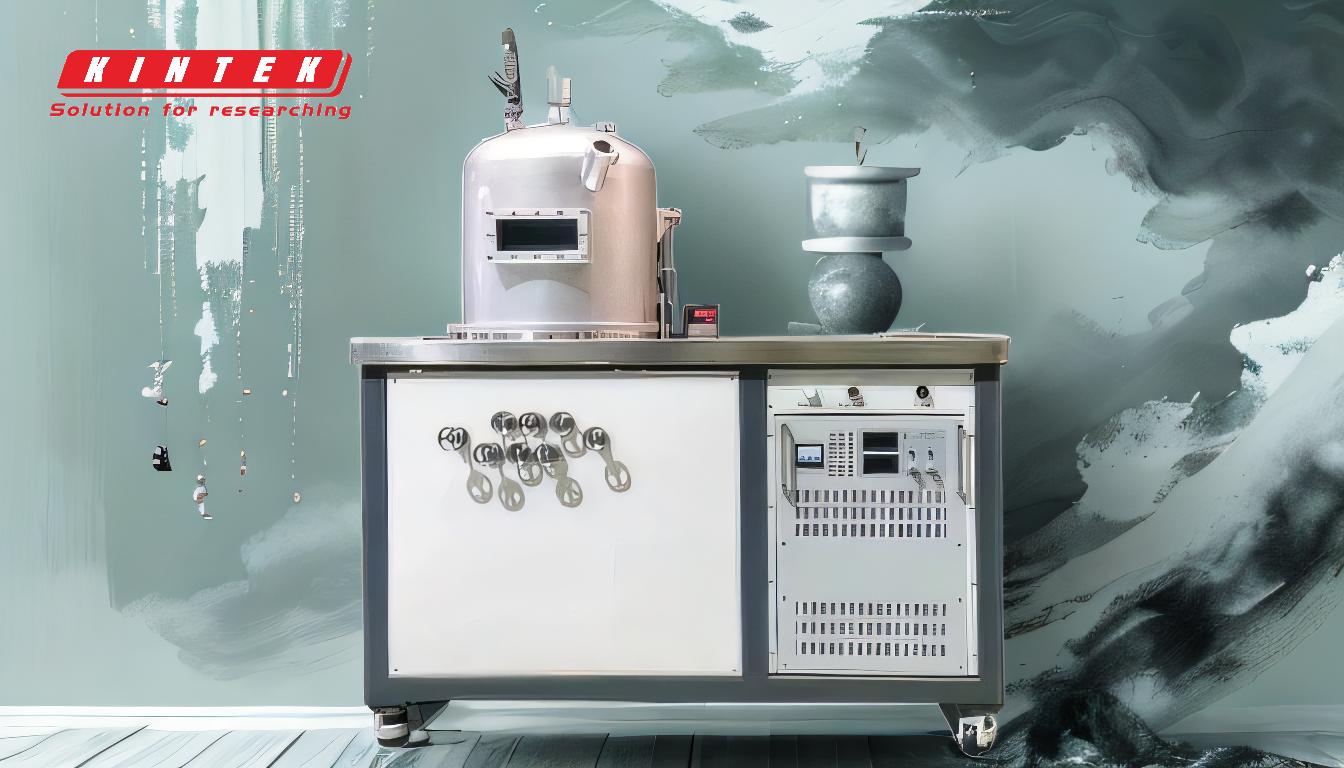
-
Mechanisms of Carbon Coating:
- Modifying Surface Chemical Stability: Carbon coatings create a barrier that protects the substrate from chemical reactions, such as oxidation or corrosion, thereby enhancing its durability in harsh environments.
- Enhancing Structural Stability: The carbon layer reinforces the substrate, preventing mechanical degradation and improving its ability to withstand physical stress.
- Improving Li-ion Diffusion: In battery applications, carbon coatings on electrode materials facilitate faster and more efficient movement of lithium ions, which is critical for battery performance.
-
Process of Carbon Coating:
- Thermal Evaporation: Carbon coating is achieved by heating a carbon source (e.g., a thread or rod) to its evaporation temperature in a vacuum system. This causes carbon to evaporate and deposit onto the substrate as a thin, uniform layer.
- Carbon Rod Coating Technique: Two carbon rods with a pointed contact area are used. A current flows between the rods, generating high heat at the contact point, which causes carbon to evaporate. This can be done with a ramping or pulsating current.
- Outgassing and Deposition: Before carbon deposition, the substrate undergoes outgassing to remove chemical binders or contaminants. The deposition is then carried out under vacuum conditions to ensure a clean and uniform coating.
-
Applications of Carbon Coating:
- Electron Microscopy: Carbon coatings are used to create specimen support films on TEM grids, enabling better imaging and analysis in electron microscopy.
- X-ray Microanalysis: The coating enhances the conductivity of specimens, improving the accuracy of X-ray microanalysis.
- Battery Technology: Carbon coatings on electrode materials improve the performance and lifespan of lithium-ion batteries by enhancing Li-ion diffusion and structural stability.
-
Benefits of Carbon Coating:
- Corrosion and Wear Resistance: The carbon layer protects the substrate from environmental damage, extending its lifespan.
- Increased Surface Hardness: The coating improves the mechanical strength of the material, making it more resistant to scratches and abrasion.
- Thermal and Electrical Insulation: Carbon coatings can provide insulation properties, depending on the application.
- Cost Efficiency: Since the coating is only a few micrometers thick, it minimizes material usage, reducing costs and addressing material scarcity concerns.
-
Technical Considerations:
- Vacuum Conditions: The process must be conducted in a vacuum to prevent contamination and ensure uniform deposition.
- Precision Control: The thickness and uniformity of the coating are critical for performance, requiring precise control of the evaporation process.
- Material Compatibility: The substrate material must be compatible with the carbon coating process to achieve the desired properties.
By understanding these key points, purchasers and users of carbon-coated materials can make informed decisions about their applications, ensuring optimal performance and cost-effectiveness.
Summary Table:
Aspect | Details |
---|---|
Mechanisms | - Enhances surface chemical stability - Improves structural stability - Boosts Li-ion diffusion |
Process | - Thermal evaporation in a vacuum system - Carbon rod coating technique - Outgassing and deposition |
Applications | - Electron microscopy - X-ray microanalysis - Battery technology |
Benefits | - Corrosion resistance - Increased surface hardness - Cost efficiency |
Technical Considerations | - Vacuum conditions - Precision control - Material compatibility |
Discover how carbon coating can optimize your materials—contact our experts today!