Physical Vapor Deposition (PVD) is a process used to deposit thin films of material onto a substrate. Unlike Chemical Vapor Deposition (CVD), which involves chemical reactions, PVD is a purely physical process. The key mechanisms in PVD include sputtering, evaporation, and ion plating. In sputtering, high-energy particles strike a target material, ejecting atoms that then deposit onto a substrate. Evaporation involves heating a material until it vaporizes, and the vapor then condenses onto the substrate. Ion plating combines these methods by ionizing the vaporized material, enhancing adhesion and film quality. PVD is widely used in industries for coating tools, electronics, and optics due to its ability to produce high-quality, durable films.
Key Points Explained:
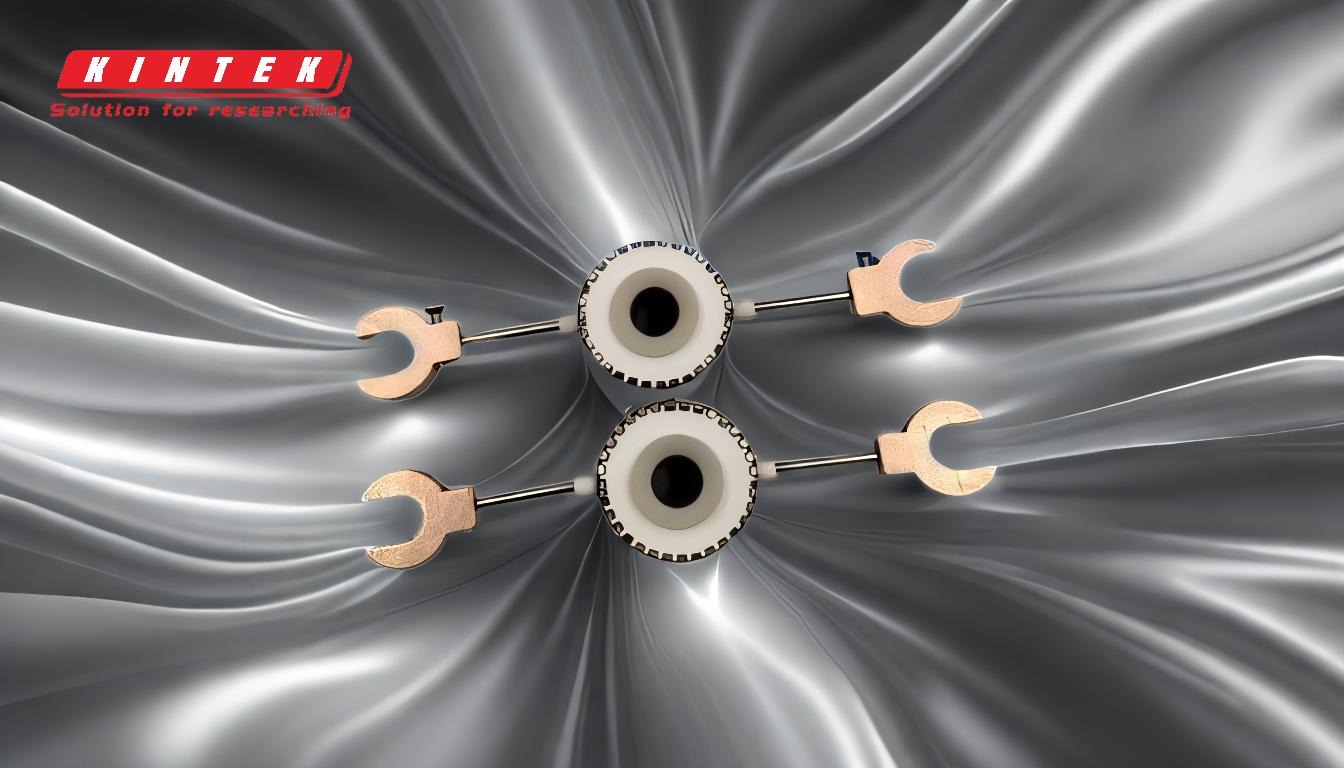
-
Mechanisms of Physical Vapor Deposition (PVD):
- Sputtering: This is a primary PVD mechanism where high-energy particles (usually ions) bombard a target material, causing atoms to be ejected from its surface. These ejected atoms then travel through a vacuum or low-pressure gas and deposit onto a substrate, forming a thin film. Sputtering is widely used because it allows for precise control over film thickness and composition.
- Evaporation: In this method, the material to be deposited is heated to its vaporization point in a vacuum. The vaporized atoms then travel to the substrate, where they condense and form a thin film. Evaporation is particularly useful for materials with low melting points and is commonly used in the production of optical coatings and electronic components.
- Ion Plating: This technique combines elements of sputtering and evaporation. The vaporized material is ionized, and the ions are then accelerated towards the substrate. This not only improves the adhesion of the film to the substrate but also enhances the density and uniformity of the deposited layer.
-
Steps Involved in PVD:
- Preparation of the Target Material: The material to be deposited is prepared in a form suitable for the chosen PVD method (e.g., a solid target for sputtering or a crucible for evaporation).
- Creation of a Vacuum: The process occurs in a vacuum chamber to minimize contamination and allow the vaporized atoms to travel unimpeded to the substrate.
- Vaporization: Depending on the method, the target material is either sputtered or evaporated, producing a vapor of atoms or molecules.
- Transport of Vapor: The vaporized atoms travel through the vacuum or low-pressure environment to the substrate.
- Deposition: The atoms condense on the substrate, forming a thin film. The properties of the film, such as thickness, adhesion, and uniformity, can be controlled by adjusting parameters like temperature, pressure, and the energy of the vaporized atoms.
-
Applications of PVD:
- Tool Coating: PVD is extensively used to coat cutting tools, molds, and dies with hard, wear-resistant materials like titanium nitride (TiN), enhancing their durability and performance.
- Electronics: In the electronics industry, PVD is used to deposit thin films of conductive, insulating, or semiconducting materials onto silicon wafers, essential for the fabrication of integrated circuits and other microelectronic devices.
- Optics: PVD is employed to create anti-reflective, reflective, or protective coatings on lenses, mirrors, and other optical components, improving their performance in various applications.
-
Advantages of PVD:
- High-Quality Films: PVD produces films with excellent adhesion, uniformity, and purity, making it suitable for demanding applications.
- Versatility: A wide range of materials, including metals, ceramics, and composites, can be deposited using PVD techniques.
- Environmentally Friendly: PVD processes typically do not involve harmful chemicals or produce hazardous byproducts, making them more environmentally friendly compared to some other deposition methods.
-
Comparison with Chemical Vapor Deposition (CVD):
- Process Nature: PVD is a physical process involving the transfer of material through vaporization and condensation, whereas CVD involves chemical reactions to deposit material.
- Temperature Requirements: PVD generally requires lower temperatures compared to CVD, making it suitable for substrates that cannot withstand high temperatures.
- Film Properties: PVD films often have better adhesion and are more dense than those produced by CVD, but CVD can produce more complex and conformal coatings, especially on intricate geometries.
In summary, Physical Vapor Deposition is a versatile and efficient method for depositing high-quality thin films on various substrates. Its mechanisms, including sputtering and evaporation, allow for precise control over film properties, making it indispensable in industries ranging from tool manufacturing to electronics and optics.
Summary Table:
Aspect | Details |
---|---|
Mechanisms | Sputtering, Evaporation, Ion Plating |
Key Steps | Target Preparation, Vacuum Creation, Vaporization, Transport, Deposition |
Applications | Tool Coating, Electronics, Optics |
Advantages | High-Quality Films, Versatility, Environmentally Friendly |
Comparison with CVD | Lower Temperature, Better Adhesion, Denser Films |
Discover how PVD can enhance your applications—contact our experts today!