Lamination is a manufacturing process that involves bonding multiple layers of materials together to create a composite material with enhanced properties such as strength, stability, and appearance. The process typically involves applying an adhesive to one substrate, pressing another substrate onto it to form a duplex (two-layer) laminate, removing excess adhesive, and winding the finished laminate onto a roll. This technique is widely used in various industries, including packaging, printing, electronics (e.g., MLCCs, hybrid chips, and ceramics), and labeling. The resulting laminated material can serve as a durable and functional product tailored to specific applications.
Key Points Explained:
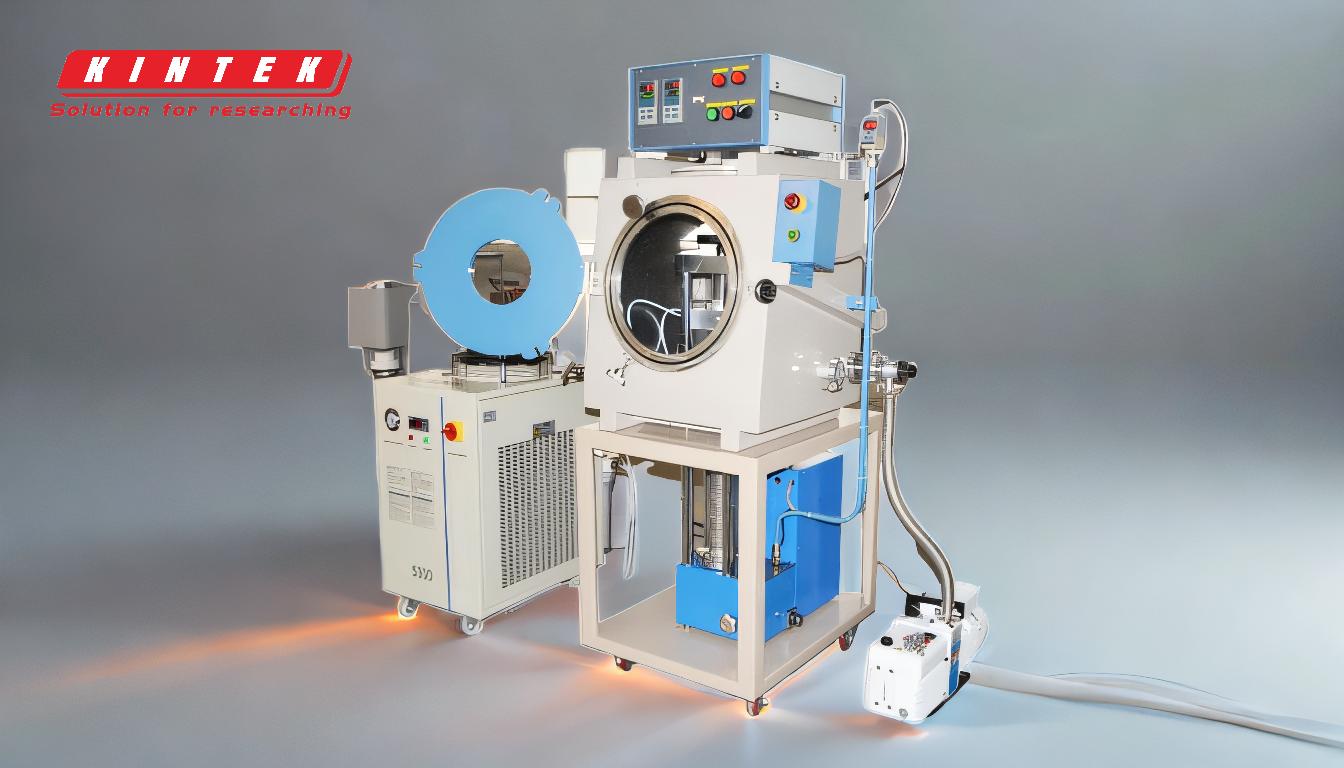
-
Definition and Purpose of Lamination:
- Lamination is a process that combines multiple layers of materials to create a single, unified composite material.
- The primary goal is to enhance properties such as strength, durability, stability, and aesthetic appeal.
- It is widely used in industries like packaging, printing, electronics, and labeling.
-
Materials Involved:
- Substrate Webs: These are the base materials that form the layers of the laminate. They can vary in composition, such as paper, plastic, or metal, depending on the application.
- Adhesive: A bonding agent is applied to one of the substrates to ensure the layers stick together effectively.
-
Steps in the Lamination Process:
- Adhesive Application: An adhesive is applied to the less absorbent substrate web. This ensures proper bonding between the layers.
- Pressing: The second substrate web is pressed onto the adhesive-coated web to form a duplex (two-layer) laminate. This step ensures even distribution of the adhesive and proper bonding.
- Excess Adhesive Removal: A blade or similar tool is used to remove any excess adhesive, ensuring a clean and uniform laminate.
- Winding: The finished laminate is wound onto a roll for storage, transport, or further processing.
-
Applications of Laminated Materials:
- Packaging: Laminated materials are often used in packaging to provide durability, moisture resistance, and aesthetic appeal.
- Printing Substrates: They serve as high-quality surfaces for printing, ensuring vibrant colors and sharp images.
- Labels: Laminated labels are durable and resistant to wear, making them ideal for product labeling.
- Electronics: In industries like electronics, lamination is used to create components such as MLCCs (multilayer ceramic capacitors), hybrid chips, and ceramics, where layered structures enhance performance.
-
Benefits of Lamination:
- Enhanced durability and strength due to the combination of multiple layers.
- Improved resistance to environmental factors like moisture, heat, and chemicals.
- Better aesthetic qualities, such as a glossy or matte finish, depending on the application.
- Tailored properties to meet specific industry requirements, such as flexibility, rigidity, or conductivity.
-
Considerations for Equipment and Consumables Purchasers:
- Adhesive Selection: Choose adhesives that are compatible with the substrates and suitable for the intended application (e.g., heat resistance for electronics).
- Substrate Compatibility: Ensure the substrate materials are compatible with the lamination process and the desired end-use properties.
- Equipment Requirements: Invest in lamination machines that offer precise control over adhesive application, pressing pressure, and winding speed.
- Quality Control: Implement processes to monitor and ensure the uniformity and quality of the laminated product.
By understanding the lamination process and its applications, purchasers can make informed decisions about the equipment and consumables needed to achieve high-quality laminated materials tailored to their specific needs.
Summary Table:
Aspect | Details |
---|---|
Definition | Bonding multiple layers to create a composite material with enhanced properties. |
Materials | Substrate webs (paper, plastic, metal) and adhesives. |
Process Steps | Adhesive application, pressing, excess adhesive removal, winding. |
Applications | Packaging, printing substrates, labels, electronics (e.g., MLCCs, ceramics). |
Benefits | Enhanced strength, durability, resistance, and aesthetic appeal. |
Key Considerations | Adhesive selection, substrate compatibility, equipment, and quality control. |
Ready to enhance your materials with lamination? Contact us today for expert guidance!