The lifespan of a heating element depends on several factors, including the material used, operating conditions, maintenance practices, and environmental factors. Silicon carbide heating elements, for example, are influenced by furnace atmosphere, watt density, operating temperature, and whether they are used continuously or intermittently. Other factors, such as alloy composition, watt loading, and device architecture, also play a role. Heating elements typically only need replacement when they fail, and manufacturers generally only warrant against manufacturing defects due to the many variables affecting their lifespan. Understanding these factors can help optimize the longevity of heating elements in specific applications.
Key Points Explained:
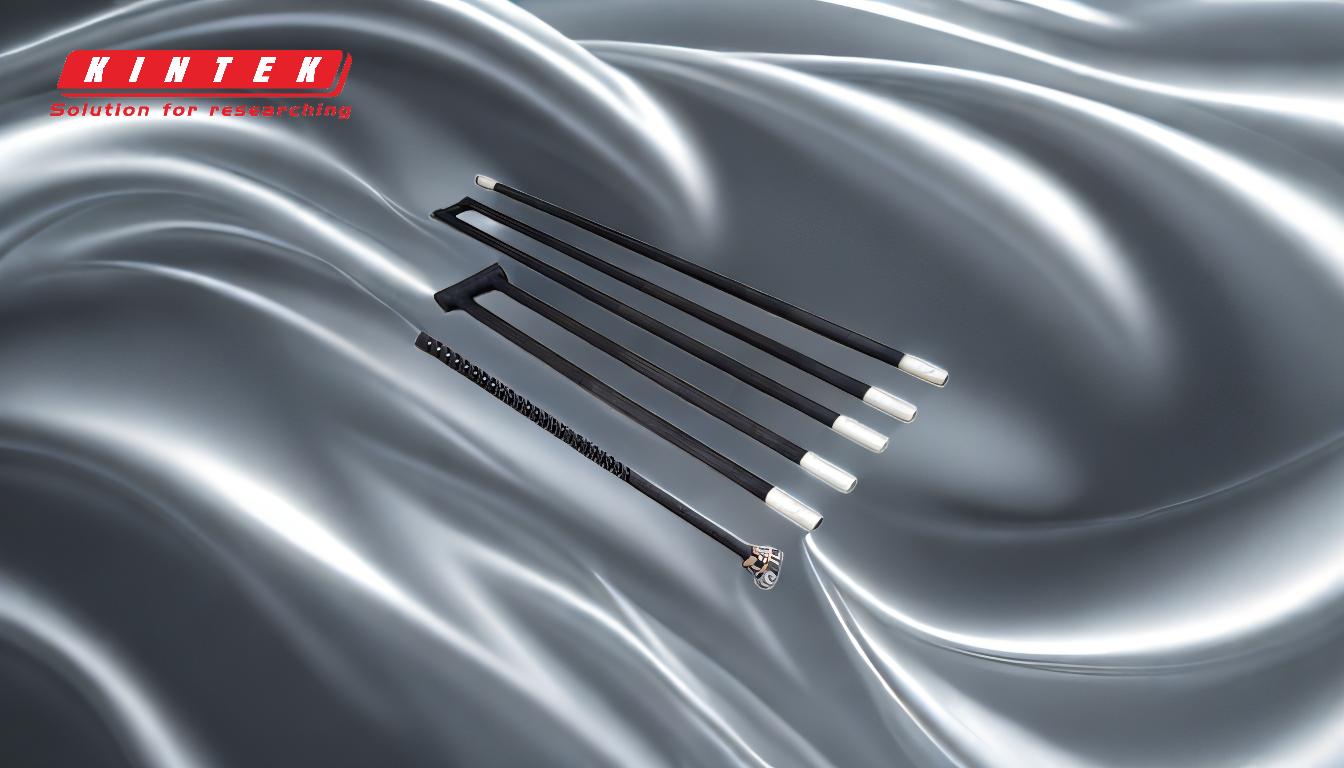
-
Material Composition and Design:
- The lifespan of a heating element is heavily influenced by its material composition and design. For instance, silicon carbide elements are known for their durability but are still affected by factors like alloy composition, dimensions, and watt loading.
- Different materials have varying temperature ratings and reactivities to oxygen, which must be considered when selecting a heating element for a specific application.
-
Operating Conditions:
- Temperature: Operating at higher temperatures can reduce the lifespan of a heating element. Silicon carbide elements, for example, are sensitive to excessive heat, which can accelerate wear and tear.
- Watt Density: Higher watt density can lead to faster degradation of the heating element. It is crucial to balance watt density with the element’s capacity to ensure longevity.
- Furnace Atmosphere: The environment in which the heating element operates (e.g., oxidizing, reducing, or neutral) significantly impacts its lifespan. Some materials are more resistant to certain atmospheres than others.
-
Usage Patterns:
- Continuous vs. Intermittent Use: Heating elements used continuously tend to wear out faster than those used intermittently. Frequent heating and cooling cycles can cause thermal stress, leading to premature failure.
- Rapid Heating and Cooling: Rapid temperature changes can cause thermal shock, which is particularly damaging to ceramic heating elements like silicon carbide.
-
Maintenance Practices:
- Regular maintenance can extend the life of a heating element. This includes cleaning, inspecting for damage, and ensuring proper alignment and connection.
- Neglecting maintenance can lead to issues like uneven heating, hotspots, and eventual failure.
-
Manufacturer Warranties and Lifespan Expectations:
- Manufacturers typically only warrant heating elements against manufacturing defects, not operational wear and tear. This is because many variables, such as furnace atmosphere and usage patterns, are beyond their control.
- Heating elements are generally replaced only when they fail, and only the failed elements in a series need to be replaced, reducing overall maintenance costs.
-
Environmental Factors:
- Reactivity to Oxygen: Some materials can tolerate elevated temperatures in the presence of oxygen, while others require protective atmospheres to prevent oxidation and degradation.
- Process Applications: The specific application (e.g., industrial furnaces, laboratory equipment) also plays a role in determining the lifespan of a heating element. Elements must be chosen based on their suitability for the intended process.
By understanding and optimizing these factors, users can maximize the lifespan of their heating elements, ensuring efficient and cost-effective operation.
Summary Table:
Factor | Impact on Lifespan |
---|---|
Material Composition | Determines durability and reactivity to oxygen; affects temperature tolerance. |
Operating Temperature | Higher temperatures accelerate wear and tear, reducing lifespan. |
Watt Density | High watt density leads to faster degradation; balance with element capacity. |
Furnace Atmosphere | Oxidizing, reducing, or neutral environments impact material resistance and lifespan. |
Usage Patterns | Continuous use and rapid heating/cooling cycles cause thermal stress and failure. |
Maintenance Practices | Regular cleaning, inspection, and alignment extend lifespan; neglect leads to failure. |
Environmental Factors | Reactivity to oxygen and suitability for specific applications influence durability. |
Maximize your heating element’s lifespan—contact our experts today for tailored solutions!