Hardening processes are critical in gear manufacturing and other industries to enhance the mechanical properties of materials, particularly their hardness and wear resistance. Commonly used hardening processes can be broadly categorized into three main types: through hardening, case hardening (including carburizing, carbonitriding, nitriding, and nitrocarburizing), and hardening by applied energy (such as flame, laser, and induction hardening). Each method has distinct mechanisms, applications, and benefits, making them suitable for different material types and industrial requirements.
Key Points Explained:
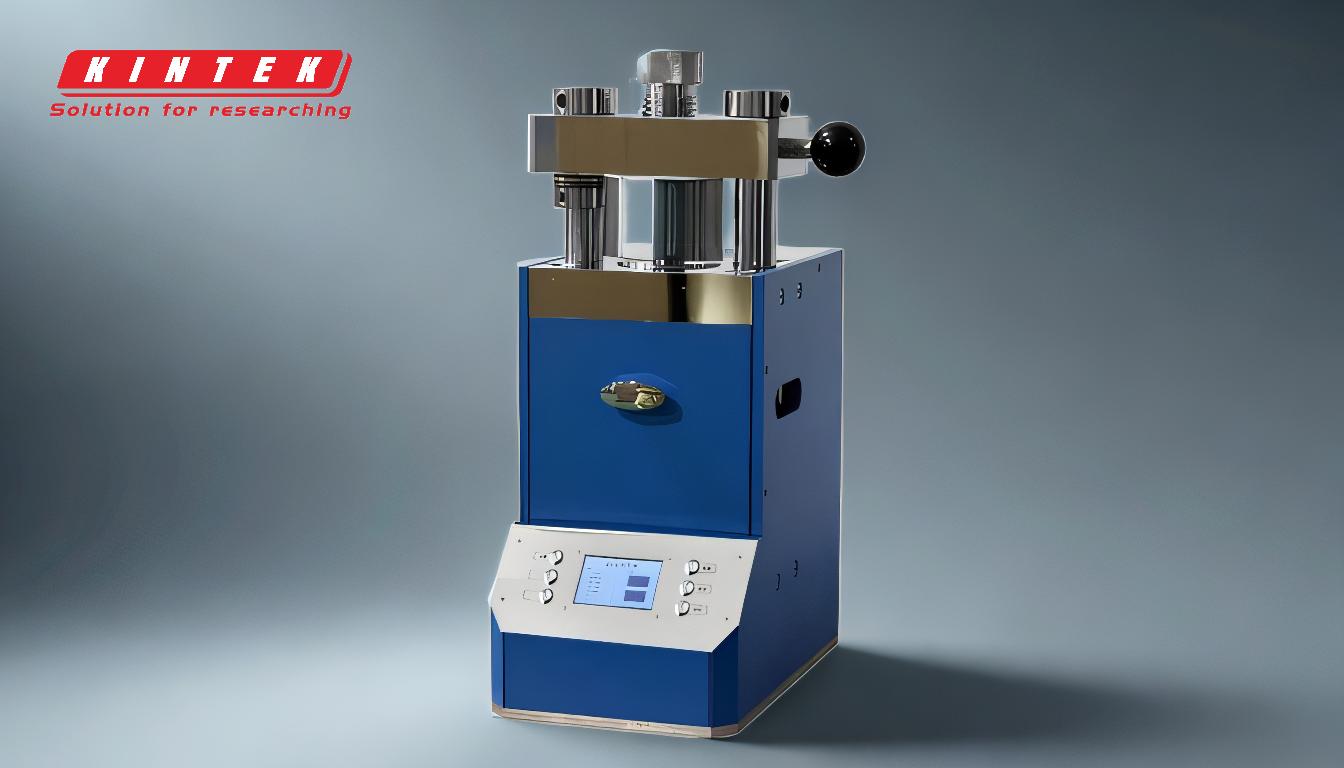
-
Through Hardening
- Definition: Through hardening, also known as bulk hardening, involves heating the entire material to a specific temperature, holding it for a set duration, and then rapidly cooling it (quenching) to achieve uniform hardness throughout the material.
- Process: The material is heated in a furnace to a temperature that transforms its internal structure (typically above the austenitizing temperature) without melting it. It is then held at this temperature for a specific time (e.g., one hour per inch of thickness) and quenched in oil, water, or air.
- Applications: Suitable for materials that require uniform hardness and strength throughout their structure, such as gears, shafts, and tools.
- Advantages: Provides consistent hardness across the entire component, improving overall durability and wear resistance.
- Limitations: May lead to brittleness in some materials, requiring tempering to reduce internal stresses.
-
Case Hardening
- Definition: Case hardening is a surface hardening process that increases the hardness of the outer layer (case) of the material while maintaining a softer, tougher core. This is achieved by introducing carbon or nitrogen into the surface layer.
-
Types of Case Hardening:
- Carburizing: Involves introducing carbon into the surface layer by heating the material in a carbon-rich environment (e.g., gas, liquid, or solid carburizing). The carbon diffuses into the surface, creating a hard, wear-resistant case.
- Carbonitriding: Similar to carburizing but involves introducing both carbon and nitrogen into the surface layer. This process is often used for low-carbon steels and provides a harder case with improved wear resistance.
- Nitriding: Involves introducing nitrogen into the surface layer by heating the material in a nitrogen-rich environment (e.g., gas or plasma nitriding). Nitriding is performed at lower temperatures than carburizing and does not require quenching.
- Nitrocarburizing: Combines nitriding and carburizing to introduce both nitrogen and carbon into the surface layer. This process is often used for components requiring high wear resistance and fatigue strength.
- Applications: Ideal for components that require a hard, wear-resistant surface and a tough core, such as gears, camshafts, and bearings.
- Advantages: Enhances surface hardness and wear resistance while maintaining the toughness of the core.
- Limitations: Limited to surface hardening, and the process can be time-consuming and expensive.
-
Hardening by Applied Energy
- Definition: This category involves localized hardening processes that use concentrated energy sources to heat specific areas of the material, followed by rapid cooling.
-
Types of Applied Energy Hardening:
- Flame Hardening: Uses an oxy-acetylene flame to heat the surface of the material, followed by quenching. This method is suitable for large components and irregular shapes.
- Laser Hardening: Uses a high-energy laser beam to heat the surface of the material, followed by rapid cooling. This method provides precise control over the hardened area and is suitable for complex geometries.
- Induction Hardening: Uses electromagnetic induction to heat the surface of the material, followed by quenching. This method is highly efficient and suitable for high-volume production.
- Applications: Used for components that require localized hardening, such as gear teeth, crankshafts, and camshafts.
- Advantages: Provides precise control over the hardened area, minimizes distortion, and is suitable for high-volume production.
- Limitations: Limited to surface hardening and requires specialized equipment.
In summary, the choice of hardening process depends on the material type, component design, and desired mechanical properties. Through hardening is ideal for uniform hardness, case hardening is suitable for surface hardness with a tough core, and hardening by applied energy is perfect for localized hardening with minimal distortion. Each method offers unique advantages and limitations, making them suitable for specific industrial applications.
Summary Table:
Hardening Process | Definition | Applications | Advantages | Limitations |
---|---|---|---|---|
Through Hardening | Uniform heating and quenching for consistent hardness throughout the material. | Gears, shafts, tools. | Consistent hardness, improved durability. | May cause brittleness, requires tempering. |
Case Hardening | Surface hardening with a tough core by introducing carbon or nitrogen. | Gears, camshafts, bearings. | Hard surface, tough core, enhanced wear resistance. | Time-consuming, expensive, limited to surface hardening. |
Hardening by Applied Energy | Localized hardening using energy sources like flame, laser, or induction. | Gear teeth, crankshafts, camshafts. | Precise control, minimal distortion, high efficiency. | Requires specialized equipment, limited to surface hardening. |
Need help choosing the right hardening process for your application? Contact our experts today!