Quenching is a critical heat treatment process used to rapidly cool materials, typically metals, to achieve desired mechanical properties such as hardness, strength, and durability. There are several types of quenching methods, each suited for specific applications and materials. The primary types include Direct Quenching, Fog Quenching, Hot Quenching, Interrupted Quenching, Selective Quenching, Slack Quenching, Spray Quenching, and Time Quenching. Each method has unique characteristics and is chosen based on the material properties and the desired outcome of the heat treatment process.
Key Points Explained:
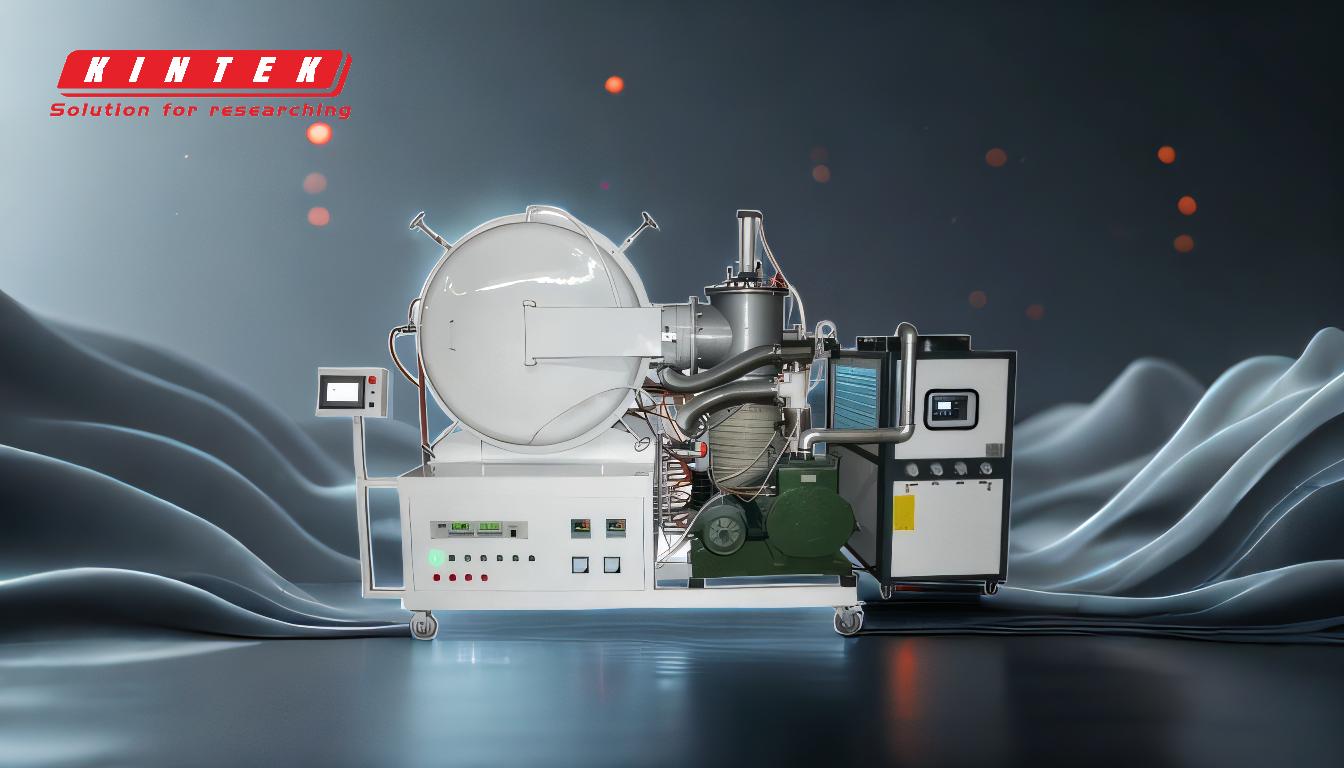
-
Direct Quenching:
- Description: This is the most common quenching method where the material is heated to a high temperature and then rapidly cooled in a quenching medium such as oil, water, or air.
- Application: Used for hardening steel and other metals to increase strength and wear resistance.
- Considerations: The choice of quenching medium (oil, water, air, or brine) depends on the material and the desired cooling rate.
-
Fog Quenching:
- Description: Involves cooling the material using a fine mist or fog of water.
- Application: Suitable for materials that require a controlled cooling rate to prevent cracking or distortion.
- Considerations: Provides a more uniform cooling compared to direct water quenching, reducing the risk of thermal stress.
-
Hot Quenching:
- Description: The material is quenched in a medium that is at an elevated temperature, typically between 150°C to 500°C.
- Application: Used to reduce the risk of cracking and distortion in high-carbon and alloy steels.
- Considerations: The higher temperature of the quenching medium slows down the cooling rate, allowing for more controlled transformation of the material's microstructure.
-
Interrupted Quenching:
- Description: The material is initially quenched rapidly and then the cooling process is interrupted at a specific temperature, followed by slower cooling.
- Application: Used to achieve a balance between hardness and toughness in the material.
- Considerations: Requires precise control of the cooling process to ensure the desired properties are achieved.
-
Selective Quenching:
- Description: Only specific areas of the material are quenched, while the rest is left to cool naturally.
- Application: Used when only certain parts of the material need to be hardened, such as in the case of gears or tools.
- Considerations: Requires careful masking or shielding of the areas not to be quenched.
-
Slack Quenching:
- Description: The material is cooled at a slower rate than in direct quenching, often using a less aggressive quenching medium.
- Application: Used to reduce internal stresses and minimize distortion in the material.
- Considerations: Results in lower hardness compared to direct quenching but with improved toughness.
-
Spray Quenching:
- Description: The material is cooled by spraying a liquid (usually water or oil) onto its surface.
- Application: Suitable for large or complex-shaped parts where uniform cooling is difficult to achieve with immersion quenching.
- Considerations: Provides better control over the cooling rate and can be adjusted to suit the geometry of the part.
-
Time Quenching:
- Description: The material is held at a specific temperature for a predetermined time before quenching.
- Application: Used to achieve specific microstructural transformations that enhance the material's properties.
- Considerations: Requires precise control of both temperature and time to ensure the desired outcome.
Each quenching method has its own advantages and limitations, and the choice of method depends on the material being treated, the desired mechanical properties, and the specific application. Understanding these different types of quenching allows for more effective heat treatment processes, leading to materials with optimized performance characteristics.
Summary Table:
Quenching Method | Description | Application | Key Considerations |
---|---|---|---|
Direct Quenching | Rapid cooling in oil, water, or air. | Hardening steel and metals for strength and wear resistance. | Choose quenching medium based on material and cooling rate. |
Fog Quenching | Cooling with a fine mist or fog of water. | Controlled cooling to prevent cracking or distortion. | Provides uniform cooling, reducing thermal stress. |
Hot Quenching | Quenching in a medium at elevated temperature (150°C–500°C). | Reduces cracking and distortion in high-carbon and alloy steels. | Slower cooling rate for controlled microstructural transformation. |
Interrupted Quenching | Rapid initial cooling, then slower cooling at a specific temperature. | Balances hardness and toughness. | Requires precise control of cooling process. |
Selective Quenching | Quenching specific areas while leaving others to cool naturally. | Hardens specific parts like gears or tools. | Requires masking or shielding of non-quenched areas. |
Slack Quenching | Slower cooling using a less aggressive medium. | Reduces internal stresses and minimizes distortion. | Results in lower hardness but improved toughness. |
Spray Quenching | Cooling by spraying liquid (water or oil) onto the surface. | Ideal for large or complex-shaped parts. | Better control over cooling rate, adjustable for part geometry. |
Time Quenching | Holding material at a specific temperature before quenching. | Achieves specific microstructural transformations. | Requires precise control of temperature and time. |
Need help selecting the right quenching method for your materials? Contact our experts today for personalized advice!