The cost of an isostatic press varies significantly based on its type, size, and intended application. Benchtop isostatic presses designed for lab-scale samples typically weigh between 20-50 pounds and cost between $5,000 and $10,000, depending on specific requirements and specifications. On the other hand, industrial-scale isostatic presses, which are much larger and designed for processing large pieces, can weigh thousands of pounds and cost anywhere from $50,000 to over $200,000. The price range reflects the differences in capacity, complexity, and customization needed for various applications.
Key Points Explained:
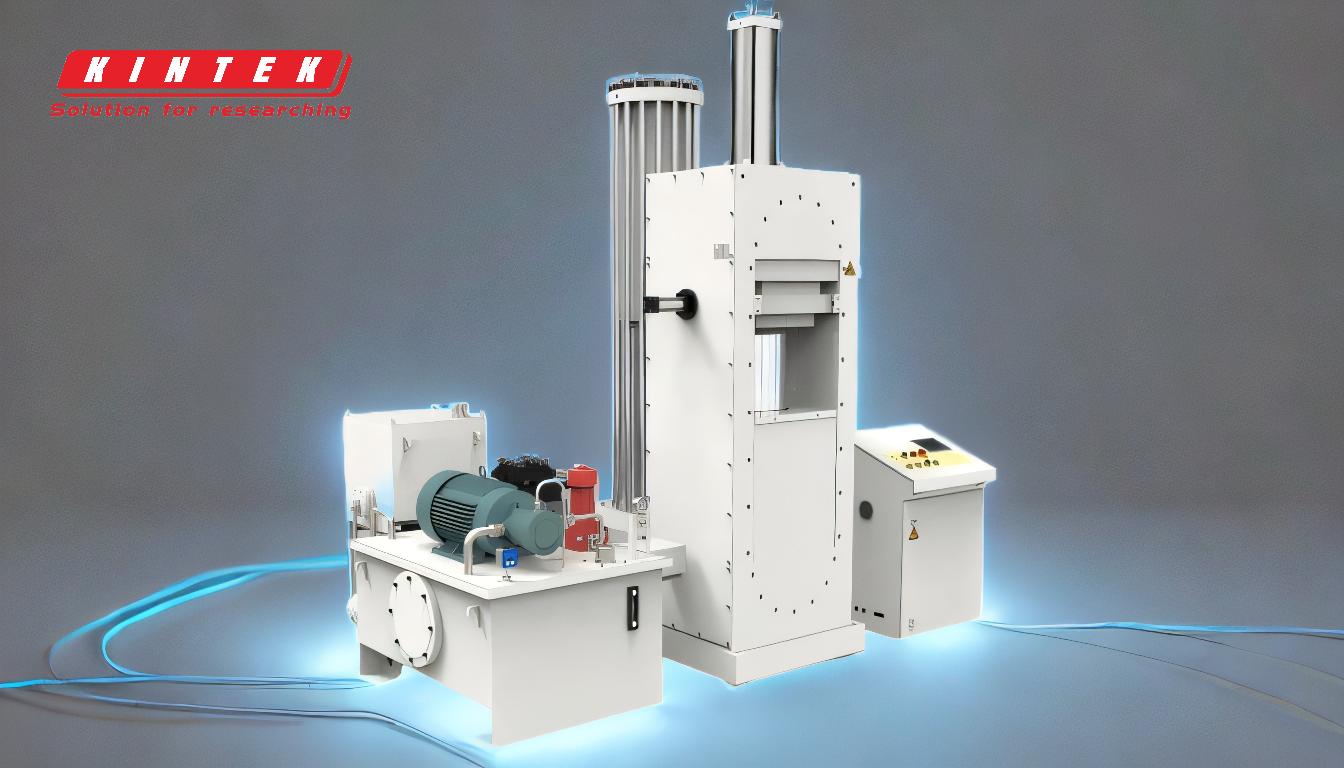
-
Types of Isostatic Presses:
- Benchtop Isostatic Presses: These are smaller, lab-scale units designed for pressing small samples. They are ideal for research and development purposes where precision and control are critical.
- Industrial Isostatic Presses: These are larger systems designed for manufacturing and production environments. They are capable of handling much larger and heavier components, making them suitable for industrial applications.
-
Cost Range:
- Benchtop Models: The cost for benchtop isostatic presses typically ranges from $5,000 to $10,000. This price range is influenced by factors such as the level of precision, control features, and customization required for specific lab applications.
- Industrial Models: Industrial isostatic presses are significantly more expensive, with prices ranging from $50,000 to over $200,000. The higher cost is due to their larger size, greater capacity, and the need for robust construction to handle high-pressure and large-scale production.
-
Factors Influencing Cost:
- Size and Capacity: Larger presses with higher capacity naturally cost more due to the increased materials and engineering required.
- Precision and Control: Advanced control systems and precision engineering can drive up the cost, especially for lab-scale units where accuracy is paramount.
- Customization: Custom-built presses designed to meet specific requirements will generally be more expensive than standard models.
- Application: The intended use of the press (e.g., research vs. industrial production) will also affect the cost, as industrial presses need to be more durable and capable of continuous operation.
-
Applications:
- Lab-Scale Presses: These are used in research and development, material testing, and small-scale production. They are ideal for applications requiring high precision and control over the pressing process.
- Industrial Presses: These are used in manufacturing processes where large components need to be pressed under high pressure. They are commonly used in industries such as aerospace, automotive, and ceramics.
-
Considerations for Purchasers:
- Budget: Determine your budget based on the scale of your operations. Lab-scale presses are more affordable but may not be suitable for large-scale production.
- Requirements: Assess your specific needs, including the size of the samples, the required pressure levels, and any special features you may need.
- Long-Term Use: Consider the long-term use and potential for scaling up. Investing in a more expensive industrial press might be justified if you anticipate future growth in production needs.
In summary, the cost of an isostatic press can vary widely depending on its type, size, and intended use. Benchtop models are more affordable and suited for lab-scale applications, while industrial models are more expensive but necessary for large-scale production. Understanding your specific requirements and budget will help you choose the right press for your needs.
Summary Table:
Type | Weight | Cost Range | Applications |
---|---|---|---|
Benchtop Presses | 20-50 lbs | $5,000 - $10,000 | Lab-scale R&D, material testing |
Industrial Presses | Thousands of lbs | $50,000 - $200,000+ | Aerospace, automotive, ceramics |
Need help choosing the right isostatic press? Contact our experts today for personalized guidance!