The preparation of thin films using the thermal evaporation technique involves a series of controlled steps within a vacuum environment to ensure high-quality film deposition. This process begins with selecting a pure material source, which is then evaporated in a vacuum chamber. The evaporated material travels through the vacuum and deposits onto a substrate, forming a thin film. Factors such as vacuum pressure, material properties, and substrate conditions significantly influence the quality and uniformity of the film. Post-deposition processes like annealing may be applied to enhance film properties. The entire process is meticulously controlled to achieve the desired film characteristics, making thermal evaporation a precise and effective method for thin film preparation.
Key Points Explained:
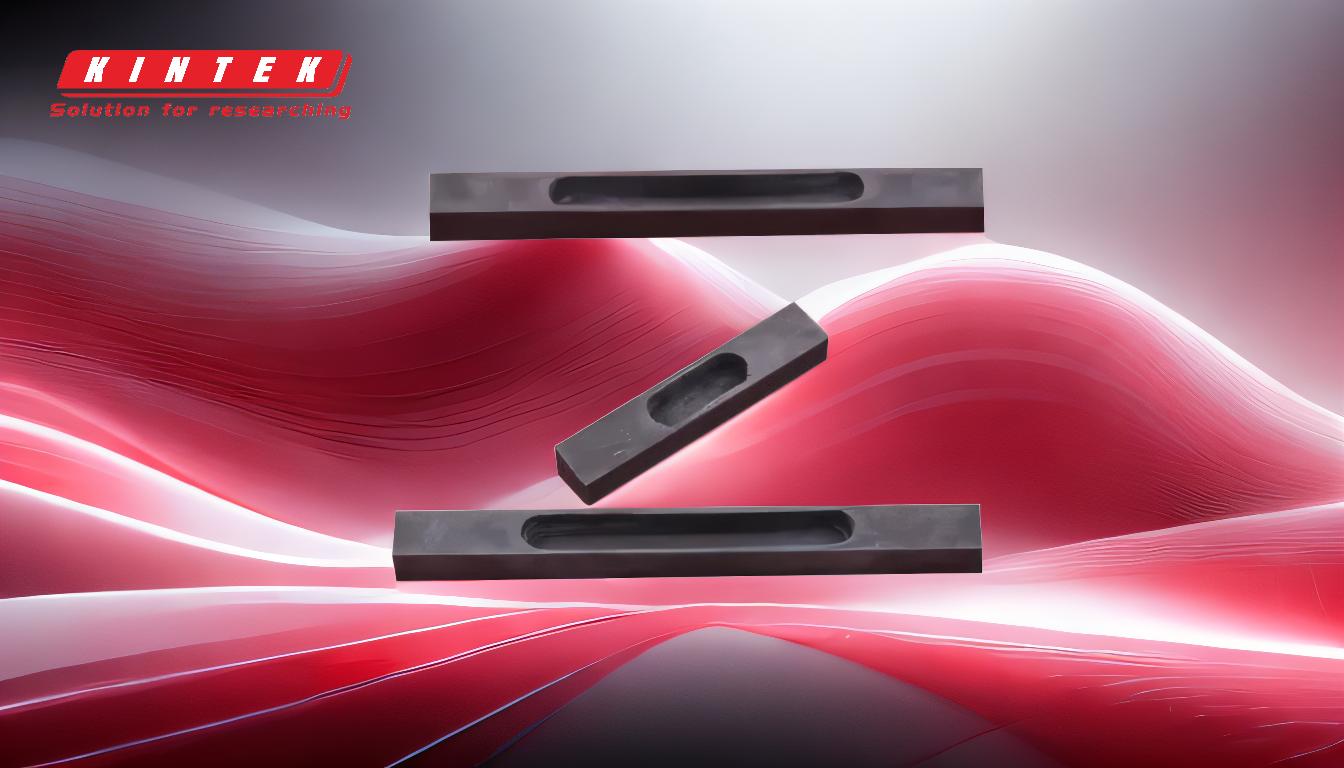
-
Selection of Material Source:
- The process begins with choosing a pure material source, often referred to as the target. The material must be compatible with thermal evaporation, meaning it should have appropriate evaporation characteristics and purity to ensure the quality of the deposited film.
- The choice of material is critical and depends on the specific application and desired film properties. For instance, materials with high melting points or specific reactivity might require special considerations.
-
Vacuum Chamber Setup:
- The thermal evaporation process takes place within a vacuum chamber to minimize the presence of impurities and to allow the evaporated material to travel freely to the substrate.
- A high degree of vacuum is essential as it increases the mean free path of the evaporated molecules, reducing collisions with residual gas molecules and thus improving the film's purity and uniformity.
-
Evaporation of the Material:
- The material source is heated to its evaporation point using a resistive heating element or an electron beam. The heat causes the material to transition from a solid to a vapor phase.
- The evaporation rate must be carefully controlled to ensure a consistent deposition rate, which is crucial for achieving uniform film thickness.
-
Deposition onto the Substrate:
- The evaporated material travels through the vacuum and deposits onto the substrate surface. The substrate is typically mounted on a holder that can be rotated to ensure even coating.
- The quality of the substrate surface is vital; a smooth surface promotes uniform deposition, whereas a rough surface can lead to non-uniform film thickness and defects.
-
Post-Deposition Processes:
- After deposition, the thin film may undergo additional treatments such as annealing or heat treatment to improve its structural and electrical properties.
- Annealing can help to relieve stresses within the film, enhance adhesion, and improve crystallinity, which are essential for the film's performance in its intended application.
-
Analysis and Quality Control:
- The properties of the deposited film, such as thickness, uniformity, and composition, are analyzed using various characterization techniques.
- Based on the analysis, the deposition process parameters may be adjusted to optimize the film quality for specific applications.
-
Considerations for Material and Process Optimization:
- The molecular weight of the source material and its evaporation rate are critical factors that influence the deposition process. Materials with higher molecular weights may require higher evaporation temperatures.
- The rotation speed of the substrate holder can also affect the film's uniformity, with faster rotation speeds generally leading to more uniform thickness distribution.
By meticulously controlling each of these factors, the thermal evaporation technique allows for the preparation of high-quality thin films with precise properties tailored to specific applications. This method is widely used in industries ranging from electronics to optics, where thin films play a crucial role in device performance and functionality.
Summary Table:
Step | Description |
---|---|
Material Selection | Choose a pure material source with appropriate evaporation characteristics. |
Vacuum Chamber Setup | Use a high-vacuum environment to minimize impurities and ensure uniform deposition. |
Evaporation of Material | Heat the material to its evaporation point using resistive heating or an electron beam. |
Deposition onto Substrate | Deposit the evaporated material onto a smooth substrate for uniform film thickness. |
Post-Deposition Processes | Apply annealing or heat treatment to enhance film properties like adhesion and crystallinity. |
Analysis and Quality Control | Analyze film properties (thickness, uniformity) and optimize process parameters. |
Ready to achieve high-quality thin films for your applications? Contact our experts today to get started!