Porosity in powder metallurgy is a critical factor that affects the mechanical properties and performance of the final product. Reducing porosity can be achieved by optimizing several key parameters during the manufacturing process. These include increasing compaction pressure, sintering temperature, and sintering time, which collectively help decrease apparent porosity and increase bulk density. Additionally, controlling particle size is crucial, as larger particles tend to increase porosity. By carefully managing these factors, manufacturers can produce high-density, low-porosity components with improved mechanical properties.
Key Points Explained:
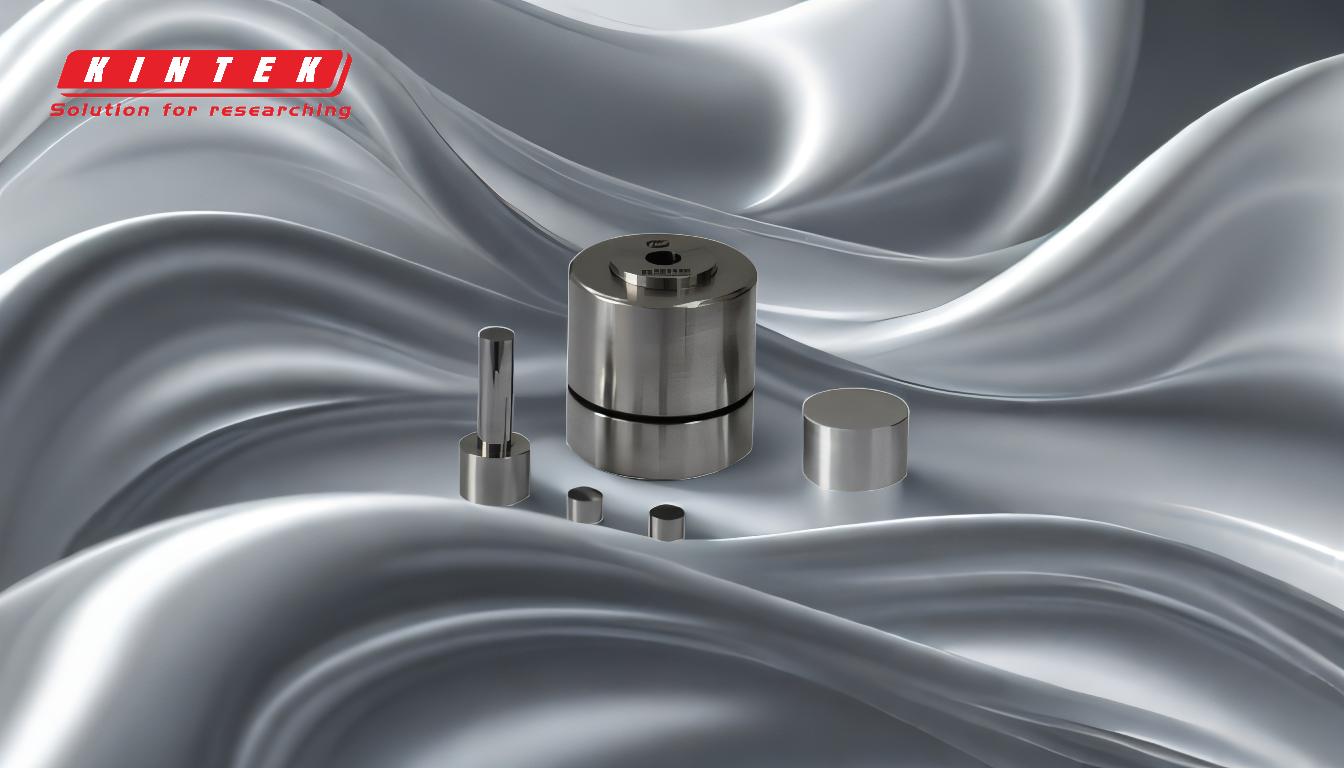
-
Increasing Compaction Pressure:
- Impact: Higher compaction pressure reduces the gaps between powder particles, leading to a denser compact with lower porosity.
- Mechanism: When pressure is applied during the compaction stage, the particles are forced closer together, minimizing voids and increasing the bulk density of the green compact.
- Practical Consideration: While higher pressure is beneficial, it must be balanced with the risk of damaging the die or causing uneven density distribution in the part.
-
Optimizing Sintering Temperature and Time:
- Impact: Higher sintering temperatures and longer sintering times promote better particle bonding and diffusion, reducing porosity and enhancing density.
- Mechanism: Sintering involves heating the compacted powder below its melting point, allowing atoms to diffuse across particle boundaries, which closes pores and strengthens the material.
- Practical Consideration: Excessive temperature or time can lead to grain growth or distortion, so careful optimization is necessary.
-
Controlling Particle Size:
- Impact: Smaller particle sizes generally result in lower porosity because they pack more efficiently, leaving fewer voids.
- Mechanism: Fine particles have a higher surface area-to-volume ratio, which enhances sintering and bonding. Larger particles, on the other hand, create more gaps and increase porosity.
- Practical Consideration: While smaller particles are preferable, they can also increase the risk of agglomeration, which must be managed during processing.
-
Powder Production Methods:
- Impact: The method used to produce metal powders influences their size, shape, and distribution, which in turn affects porosity.
- Mechanism: Techniques like atomization produce powders with controlled size ranges, which can be tailored to minimize porosity. Crushing and grinding may produce irregularly shaped particles that pack less efficiently.
- Practical Consideration: Selecting the appropriate powder production method is essential for achieving the desired particle characteristics and minimizing porosity.
-
Material Selection:
- Impact: The choice of base material (e.g., copper-base or iron-base) can influence porosity due to differences in particle shape, size, and sintering behavior.
- Mechanism: Some materials sinter more readily than others, leading to better densification and lower porosity.
- Practical Consideration: Material selection should align with the intended application and desired mechanical properties.
By addressing these key factors, manufacturers can effectively reduce porosity in powder metallurgy, resulting in components with improved strength, durability, and performance.
Summary Table:
Key Factor | Impact | Mechanism | Practical Consideration |
---|---|---|---|
Increasing Compaction Pressure | Reduces gaps between particles, leading to denser compacts with lower porosity. | Pressure forces particles closer, minimizing voids and increasing bulk density. | Balance pressure to avoid die damage or uneven density distribution. |
Optimizing Sintering Temperature & Time | Promotes particle bonding, reduces porosity, and enhances density. | Heating below melting point allows atom diffusion, closing pores and strengthening the material. | Avoid excessive temperature or time to prevent grain growth or distortion. |
Controlling Particle Size | Smaller particles pack efficiently, reducing porosity. | Fine particles have higher surface area-to-volume ratio, enhancing sintering and bonding. | Manage agglomeration risks with smaller particles. |
Powder Production Methods | Influences particle size, shape, and distribution, affecting porosity. | Atomization produces controlled size ranges; crushing/grinding may create irregular particles. | Select the right method to achieve desired particle characteristics. |
Material Selection | Base material affects porosity due to differences in sintering behavior. | Some materials sinter more readily, leading to better densification and lower porosity. | Align material choice with application and desired mechanical properties. |
Ready to optimize your powder metallurgy process? Contact our experts today for tailored solutions!