Thermal evaporation in Physical Vapor Deposition (PVD) is a process where a solid or liquid material is heated to a high temperature in a vacuum environment, causing it to evaporate and form a thin film on a substrate. The material, placed in a crucible, is heated using a resistive heat source until its vapor pressure exceeds the vacuum pressure, leading to sublimation or boiling. The evaporated atoms travel through the vacuum chamber and condense on the cooler substrate, forming a thin film. This process is carried out at high vacuum pressures (less than 10^-5 torr) to ensure minimal collisions and efficient transport of vapor to the substrate. The technique is gentle, energy-efficient, and produces low-energy evaporated particles (around 0.12 eV).
Key Points Explained:
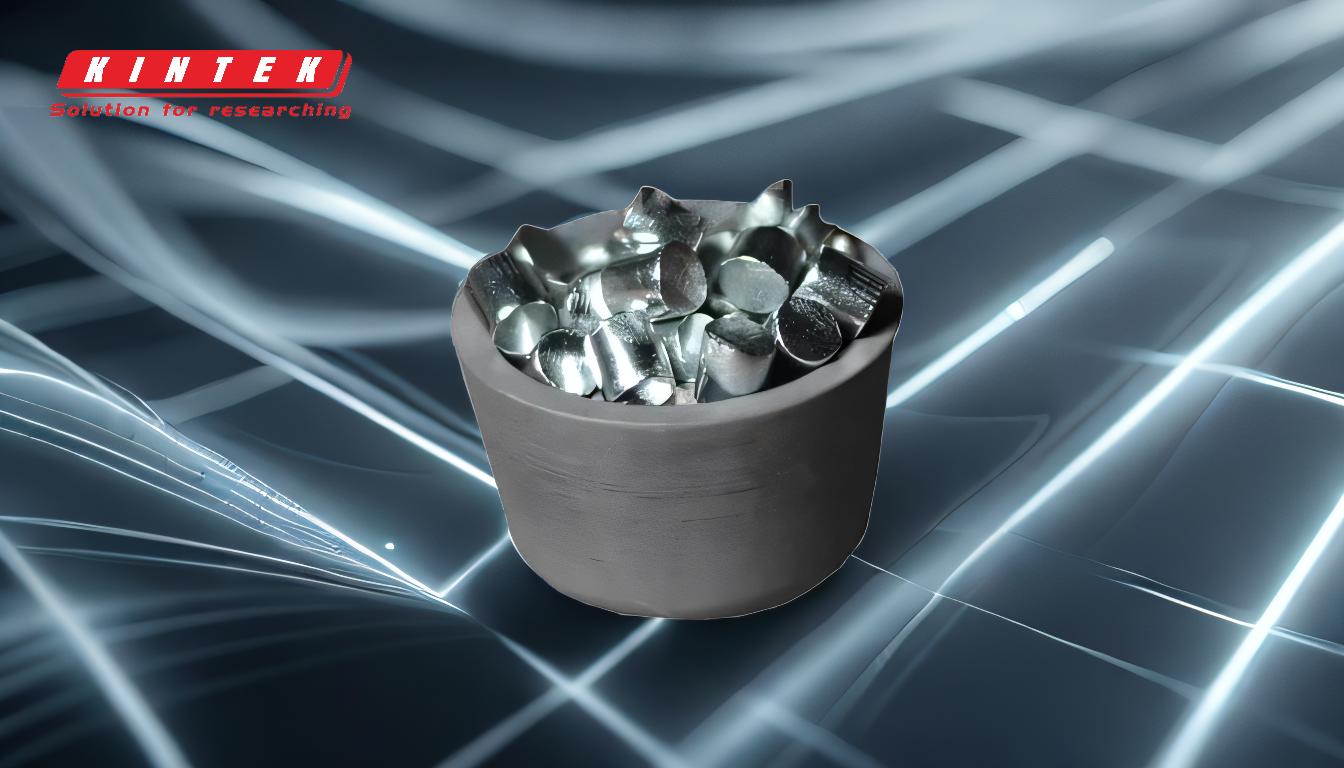
-
Principle of Thermal Evaporation:
- Thermal evaporation is based on heating a material (solid or liquid) in a vacuum until it reaches its vaporization temperature.
- The material is placed in a crucible and heated using a resistive heat source, causing it to sublimate or boil.
- The vapor pressure of the material must exceed the vacuum pressure for evaporation to occur.
-
Vacuum Environment:
- The process is conducted in a high vacuum chamber with pressures typically below 10^-5 torr.
- The vacuum ensures minimal collisions between evaporated atoms and residual gas molecules, allowing for efficient and collisionless transport of vapor to the substrate.
-
Heating Mechanism:
- A resistive heat source is used to heat the material to the required temperature.
- The heat source can be a filament, boat, or crucible made of materials like tungsten, tantalum, or graphite, depending on the material being evaporated.
-
Vaporization Process:
- As the material is heated, its surface atoms gain enough thermal energy to overcome the binding forces and leave the surface.
- This results in the formation of a vapor stream that travels through the vacuum chamber.
-
Transport of Vapor:
- The evaporated atoms or molecules traverse the vacuum chamber at thermal energy levels (typically less than 1 eV).
- The substrate is positioned at a lower temperature compared to the source, facilitating condensation of the vapor onto the substrate.
-
Condensation and Film Formation:
- The vapor condenses on the cooler substrate, forming a thin film.
- The thickness of the film can range from angstroms to microns, depending on the deposition parameters.
-
Advantages of Thermal Evaporation:
- It is a simple and cost-effective PVD technique.
- The process is gentle, with low power consumption and minimal damage to the substrate.
- It produces low-energy evaporated particles, making it suitable for delicate substrates.
-
Applications:
- Thermal evaporation is widely used in the deposition of pure materials, such as metals, semiconductors, and dielectrics.
- It is employed in various industries, including electronics, optics, and coatings, for applications like thin-film transistors, solar cells, and reflective coatings.
-
Limitations:
- The process is limited to materials that can be evaporated at temperatures compatible with the crucible and heating elements.
- It may not be suitable for materials with very high melting points or those that decompose before evaporation.
-
Process Optimization:
- The deposition rate, film thickness, and uniformity can be controlled by adjusting parameters such as heating power, vacuum pressure, and substrate temperature.
- Proper alignment of the source and substrate is crucial for achieving uniform coatings.
By understanding these key points, one can effectively utilize thermal evaporation in PVD for various thin-film deposition applications, ensuring high-quality and consistent results.
Summary Table:
Aspect | Details |
---|---|
Principle | Heating material in a vacuum until it vaporizes and forms a thin film. |
Vacuum Environment | Operates at pressures below 10^-5 torr for efficient vapor transport. |
Heating Mechanism | Resistive heat sources like filaments or crucibles heat the material. |
Advantages | Cost-effective, gentle process, low-energy particles, suitable for delicate substrates. |
Applications | Used in electronics, optics, and coatings for thin-film transistors, solar cells, and more. |
Limitations | Limited to materials with compatible vaporization temperatures. |
Discover how thermal evaporation can enhance your thin-film processes—contact our experts today!