Electric arc furnaces (EAFs) offer several advantages over basic oxygen furnaces (BOFs), particularly in terms of flexibility, energy efficiency, and environmental impact. EAFs can achieve 100% scrap metal recycling, making them highly sustainable and cost-effective for steel recycling. They provide operational flexibility, allowing for easy start-stop processes, and are capable of producing high-quality alloy steel. Additionally, EAFs are more compact, energy-efficient, and technologically advanced, enabling precise temperature control and effective impurity removal. These features make EAFs a preferred choice in modern steelmaking, especially for recycling and producing specialized steels.
Key Points Explained:
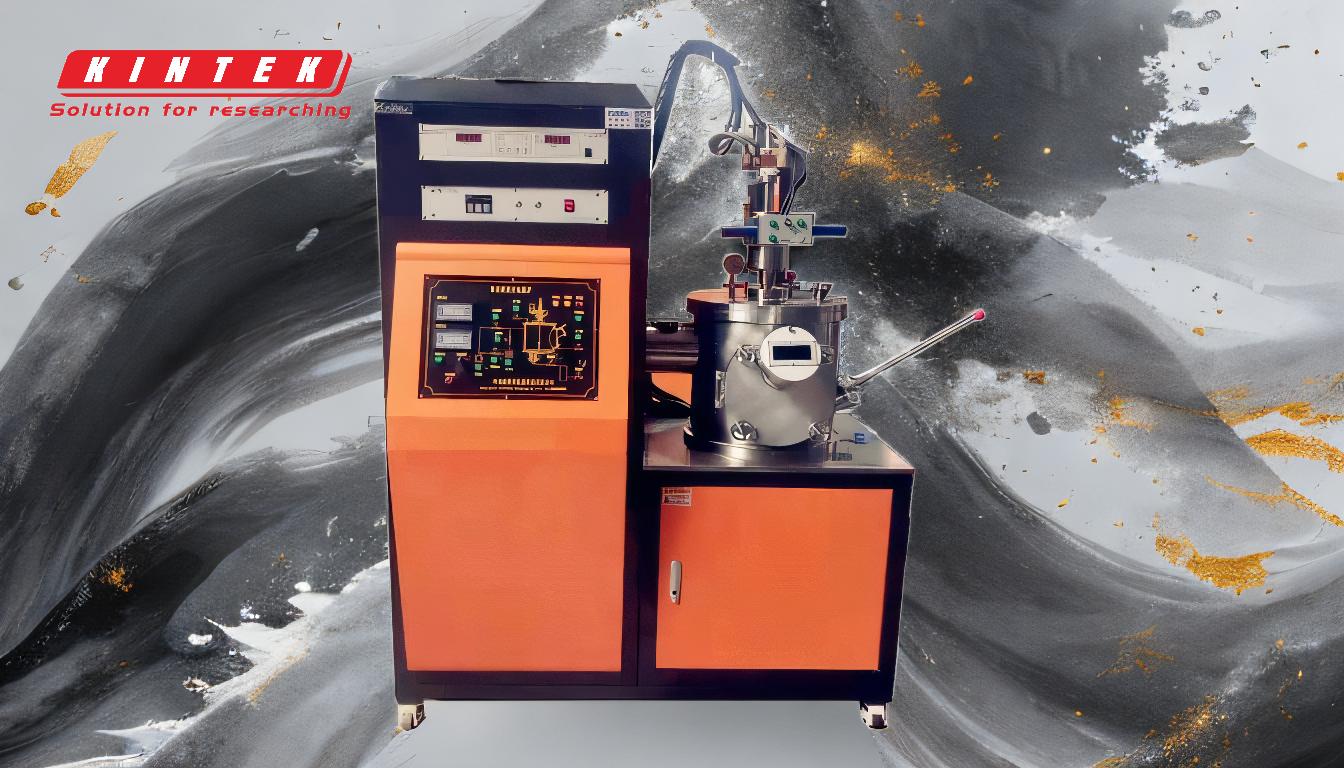
-
Scrap Metal Recycling:
- EAFs can utilize 100% scrap metal, making them ideal for recycling and reducing the need for raw materials like iron ore. This not only lowers costs but also minimizes environmental impact by reducing waste and emissions.
- In contrast, BOFs primarily rely on raw materials such as pig iron and limited scrap metal, making them less sustainable.
-
Operational Flexibility:
- EAFs allow smelters to start and stop the process as needed, providing greater flexibility in production scheduling. This is particularly useful for adapting to market demands or energy availability.
- BOFs, on the other hand, require continuous operation and are less adaptable to fluctuations in production needs.
-
Energy Efficiency:
- EAFs use electrical currents to melt scrap steel, which is more energy-efficient compared to the combustion processes used in BOFs. This reduces overall energy consumption and operational costs.
- The ability to control energy input precisely also contributes to better energy management.
-
Technological Advantages:
- EAFs offer superior technological flexibility, enabling precise temperature control and effective removal of impurities like sulphur and phosphorus. This makes them suitable for producing high-quality alloy steel.
- Their compact design and small volume make them easier to operate and maintain, while also ensuring a high degree of purity in the final product.
-
Environmental Benefits:
- By recycling scrap metal and using electricity instead of fossil fuels, EAFs significantly reduce greenhouse gas emissions and other pollutants compared to BOFs.
- This aligns with global sustainability goals and makes EAFs a more environmentally friendly option.
-
Cost-Effectiveness:
- The ability to use scrap metal and lower energy consumption translates to reduced production costs. Additionally, the flexibility in operation allows for better resource management and cost control.
- BOFs, with their reliance on raw materials and continuous operation, tend to have higher operational costs.
In summary, electric arc furnaces present clear advantages over basic oxygen furnaces in terms of sustainability, flexibility, energy efficiency, and cost-effectiveness. These benefits make EAFs a preferred choice for modern steelmaking, particularly in recycling and producing specialized steels.
Summary Table:
Advantage | Electric Arc Furnace (EAF) | Basic Oxygen Furnace (BOF) |
---|---|---|
Scrap Metal Recycling | 100% scrap metal utilization, reducing raw material needs and environmental impact. | Relies on raw materials like pig iron, with limited scrap metal usage. |
Operational Flexibility | Easy start-stop processes, adaptable to market demands and energy availability. | Requires continuous operation, less adaptable to production fluctuations. |
Energy Efficiency | Uses electrical currents, reducing energy consumption and operational costs. | Relies on combustion processes, leading to higher energy consumption. |
Technological Advantages | Precise temperature control, effective impurity removal, and compact design. | Less advanced in temperature control and impurity management. |
Environmental Benefits | Reduces greenhouse gas emissions and pollutants by using electricity and recycling scrap. | Higher emissions due to reliance on fossil fuels and raw materials. |
Cost-Effectiveness | Lower production costs due to scrap metal usage and energy efficiency. | Higher operational costs due to raw material dependence and continuous operation. |
Ready to enhance your steelmaking process with electric arc furnaces? Contact us today to learn more!