Sintered components are solid materials created through the sintering process, which involves compacting and bonding particles (such as metals, ceramics, or plastics) using heat and pressure without fully melting the material. This method is particularly useful for materials with high melting points, like tungsten and molybdenum, and is widely used in industries such as automotive, biomedical, and mechanical engineering. Sintered components offer advantages like cost efficiency, complex shape production, environmental friendliness, and excellent mechanical properties. The process can involve technologies like powder pressing, metal injection molding, and additive manufacturing, making it versatile for various applications.
Key Points Explained:
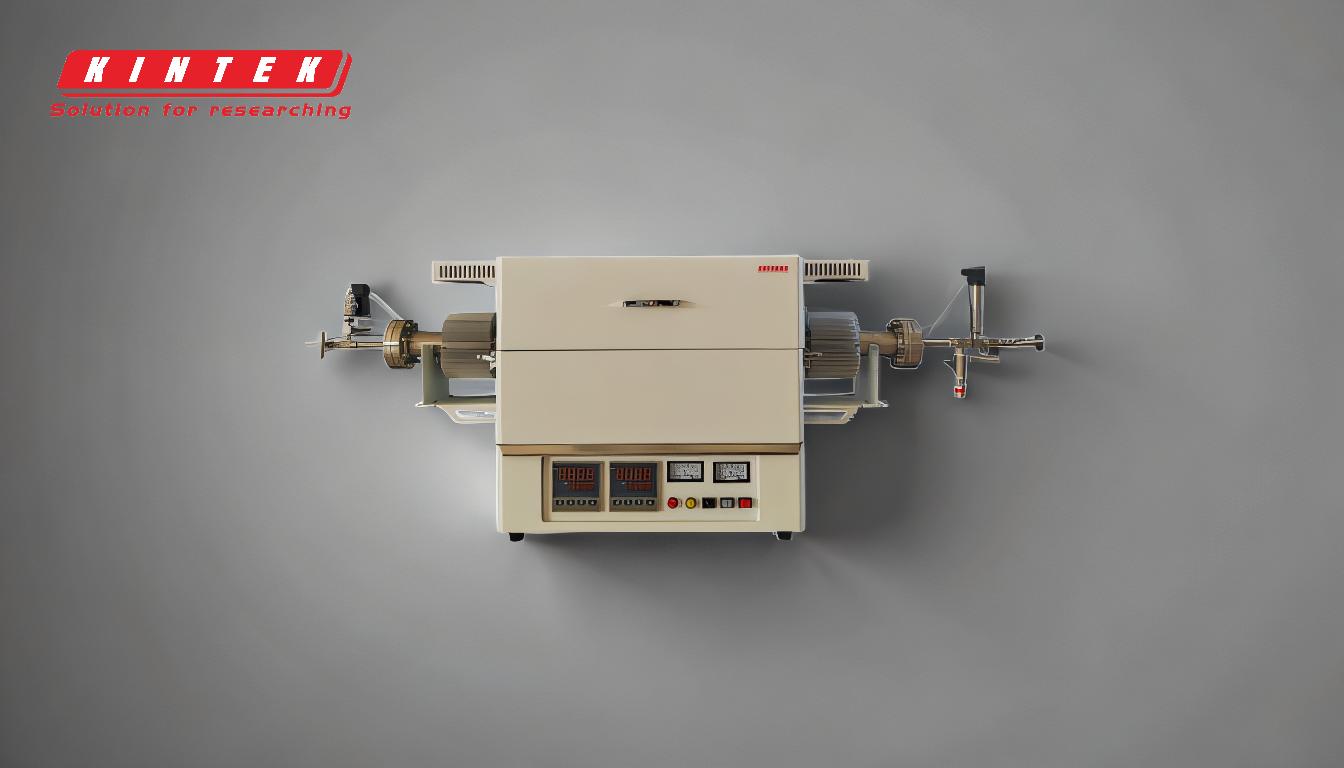
-
Definition of Sintering:
- Sintering is a manufacturing process that compacts and bonds particles into a solid mass using heat and pressure, without melting the material to its liquefaction point.
- It is commonly used for materials with high melting points, such as metals (e.g., tungsten, molybdenum) and ceramics.
-
How Sintering Works:
- The process involves heating powdered materials below their melting point, allowing atoms to diffuse across particle boundaries and fuse together.
- Pressure is often applied to ensure the particles bond tightly, resulting in a dense and durable solid mass.
-
Materials Used in Sintering:
- Sintering can be applied to a wide range of materials, including metals, ceramics, plastics, and composites.
- Common sintered metals include stainless steel, tungsten, and molybdenum, which are used in high-performance applications.
-
Technologies and Methods:
- Powder Pressing: Compacting metal powders into a desired shape before sintering.
- Metal Injection Molding (MIM): Combining powdered metal with a binder, molding it into shape, and then sintering to remove the binder and fuse the particles.
- Additive Manufacturing (Binder Jetting and Metal FDM): Using 3D printing technologies to create complex shapes that are later sintered to achieve final strength and density.
-
Applications of Sintered Components:
- Automotive Industry: Sintered parts are used in engines, transmissions, and braking systems due to their strength and durability.
- Biomedical Industry: Sintered components are used in implants and medical devices because of their biocompatibility and precision.
- Mechanical Engineering: Sintered parts are used in machinery and tools for their wear resistance and complex geometries.
- Fashion Industry: Sintered metals are used in jewelry and accessories for their intricate designs and surface finishes.
-
Advantages of Sintered Components:
- Cost Efficiency: Reduced material waste and lower production costs compared to traditional manufacturing methods.
- Complex Shapes: Ability to produce intricate and complex geometries that are difficult to achieve with other methods.
- Environmental Friendliness: Minimal waste and energy consumption during the sintering process.
- Surface Finish and Tolerance Control: Excellent surface finishes and precise dimensional tolerances, reducing the need for post-processing.
-
Performance Properties:
- Sintered components exhibit high strength, durability, and wear resistance, making them suitable for demanding applications.
- They can be tailored to specific performance requirements by adjusting the sintering parameters and material composition.
By understanding these key points, it becomes clear why sintering is a preferred method for producing high-performance components across various industries. Its versatility, efficiency, and ability to create complex shapes make it a valuable manufacturing process.
Summary Table:
Aspect | Details |
---|---|
Definition | Compacting and bonding particles using heat and pressure without melting. |
Materials | Metals (e.g., tungsten, molybdenum), ceramics, plastics, and composites. |
Technologies | Powder pressing, metal injection molding, additive manufacturing. |
Applications | Automotive, biomedical, mechanical engineering, fashion. |
Advantages | Cost efficiency, complex shapes, environmental friendliness, high strength. |
Explore how sintered components can enhance your projects—contact us today!