The three stages of heat treatment are heating, soaking, and cooling. These stages are universally applicable across various industries, including aerospace, and are designed to alter the physical and sometimes chemical properties of materials, particularly metals. Heating involves raising the material to a specified temperature to prepare it for structural changes. Soaking maintains the material at this temperature for a set duration to ensure uniform transformation. Cooling returns the material to room temperature, solidifying its new properties. Each stage is critical and must be carefully controlled to achieve the desired material characteristics, such as hardness, ductility, or stress relief.
Key Points Explained:
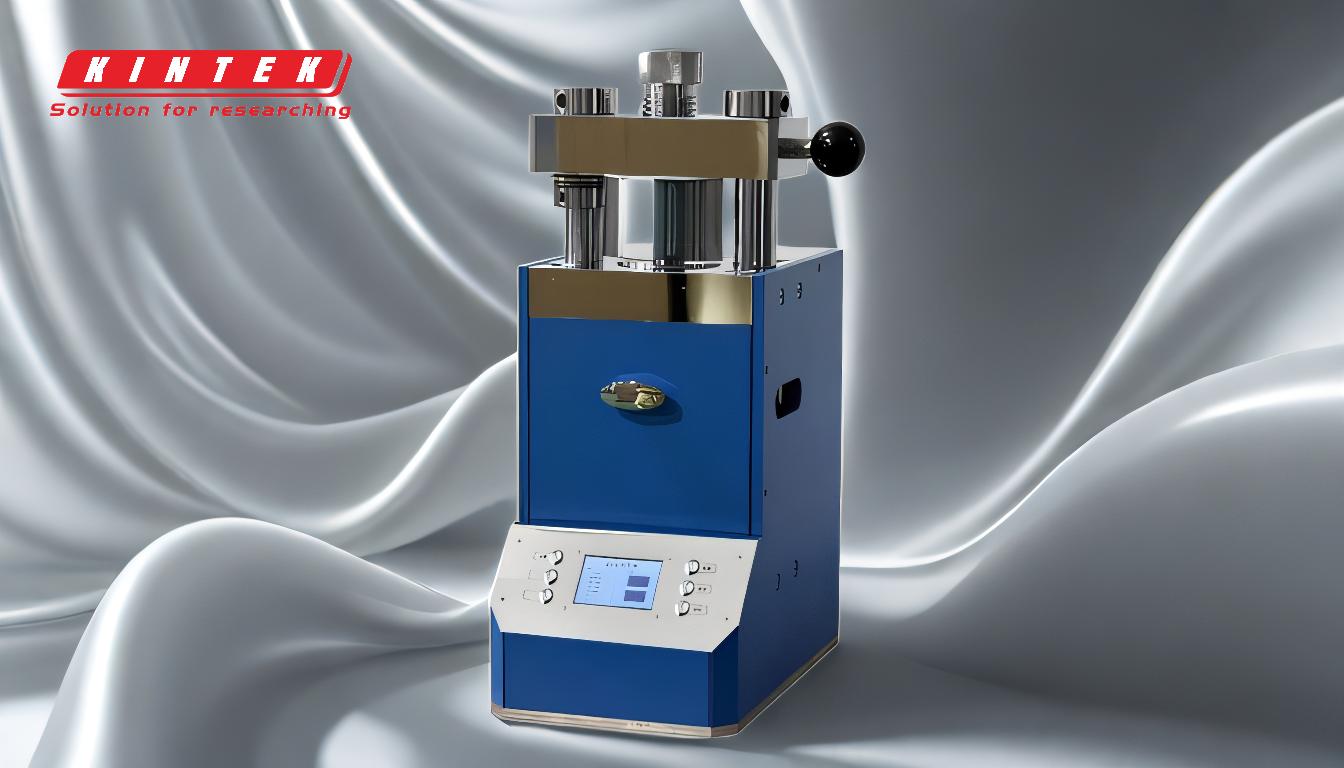
-
Heating:
- Purpose: The primary goal of heating is to raise the material's temperature to a specific level that allows for the desired structural changes. This temperature can range up to 2,400°F, depending on the material and the intended outcome.
- Process: The material is gradually heated to prevent thermal shock, which can cause cracking or deformation. The heating rate and final temperature are carefully controlled based on the material's properties and the heat treatment objectives.
- Importance: Proper heating ensures that the material reaches a uniform temperature throughout, which is essential for consistent results in the subsequent stages.
-
Soaking:
- Purpose: Soaking involves maintaining the material at the specified temperature for a predetermined period. This stage ensures that the entire material reaches thermal equilibrium and that the desired internal structural changes occur uniformly.
- Duration: The soaking time can vary significantly, from a few seconds to over 60 hours, depending on the material's thickness, composition, and the specific heat treatment process being applied.
- Importance: Soaking is crucial for achieving the desired microstructure, such as the formation of austenite in steel, which is necessary for processes like hardening or annealing. Inadequate soaking can lead to inconsistent material properties.
-
Cooling:
- Purpose: Cooling is the final stage where the material is returned to room temperature. The cooling method and rate are critical as they determine the final properties of the material, such as hardness, toughness, and stress levels.
- Methods: Cooling can be done in various ways, including air cooling, oil quenching, water quenching, or controlled furnace cooling. Each method has a different effect on the material's microstructure and properties.
- Importance: The cooling rate must be carefully controlled to avoid issues like warping, cracking, or the formation of undesirable phases. For example, rapid cooling (quenching) is used to harden steel, while slow cooling is used in annealing to soften the material.
Additional Considerations:
- Material-Specific Requirements: Different materials require different heat treatment parameters. For instance, aluminum alloys may need lower temperatures compared to steel, and the soaking time may be shorter.
- Process Variations: Heat treatment processes like annealing, tempering, and hardening each have unique requirements for heating, soaking, and cooling. For example, annealing typically involves slow cooling to soften the material, while hardening involves rapid cooling to increase hardness.
- Equipment and Atmosphere: The equipment used for heat treatment, such as furnaces, must be capable of precise temperature control. Additionally, the atmosphere within the furnace (e.g., inert gases like argon or hydrogen) can affect the outcome, especially in processes like bright annealing, where oxidation must be minimized.
In summary, the three stages of heat treatment—heating, soaking, and cooling—are fundamental to altering the properties of materials. Each stage must be meticulously controlled to achieve the desired outcomes, whether it's increasing hardness, improving ductility, or relieving stress. Understanding these stages is essential for anyone involved in material processing, from aerospace engineers to metal fabricators.
Summary Table:
Stage | Purpose | Key Details |
---|---|---|
Heating | Raise material temperature for structural changes | - Temperature up to 2,400°F - Gradual heating to prevent thermal shock - Ensures uniform heat |
Soaking | Maintain temperature for uniform transformation | - Duration: seconds to 60+ hours - Achieves thermal equilibrium - Critical for microstructure |
Cooling | Return material to room temperature to solidify new properties | - Methods: air, oil, water, or furnace cooling - Determines final hardness, toughness, and stress |
Optimize your material properties with expert heat treatment solutions—contact us today!