Heat treatment is a critical process in manufacturing, offering numerous advantages such as enhancing material properties, improving strength, and reducing internal stresses. However, it also has limitations, including potential material distortion, high energy consumption, and the need for precise control. The integration of advanced techniques like vacuum heat treatment and Hot Isostatic Pressing (HIP) further amplifies these benefits by improving efficiency, reducing scrap, and optimizing material performance. Below, we explore the key advantages and limitations of heat treatment processes in detail.
Key Points Explained:
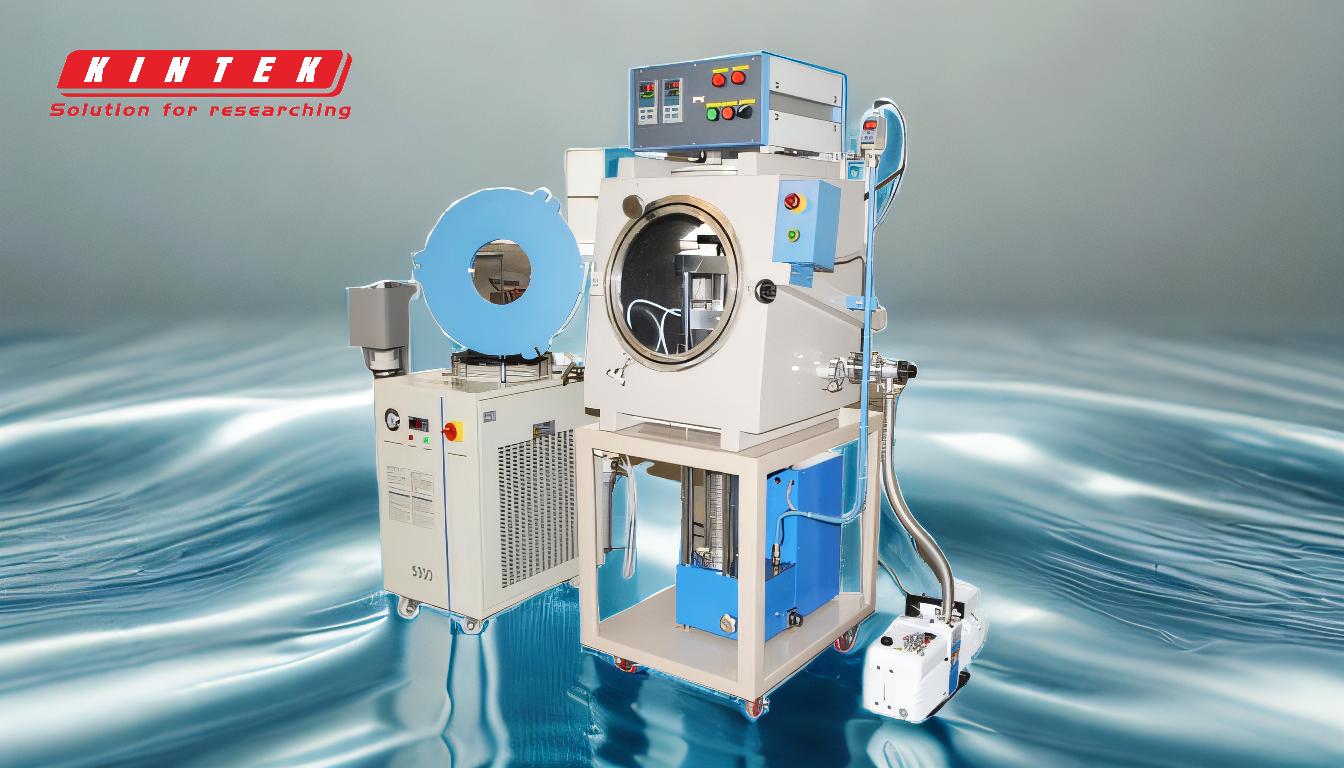
-
Advantages of Heat Treatment:
-
Improved Material Properties:
- Heat treatment can significantly alter the mechanical properties of materials, such as increasing strength, hardness, and ductility. For example, it can introduce wear-resistant characteristics or improve brittleness, making materials more suitable for demanding applications.
- It also enhances electrical and magnetic properties, which is particularly beneficial for materials used in electronics and electrical engineering.
-
Stress Relief:
- Heat treatment helps relieve internal stresses in materials, making them easier to machine, weld, or form. This is especially important in processes like hot forming or post-welding treatments.
-
Versatility:
- It is applicable to a wide range of materials, including steel, aluminum, and ceramics, making it a versatile process across industries.
-
Integration with Advanced Techniques:
- Combining heat treatment with vacuum processes (e.g., vacuum drying or vacuum heating) prevents issues like ice formation and reduces the energy required for moisture removal. This improves efficiency and results in higher-quality outputs.
-
Improved Material Properties:
-
Limitations of Heat Treatment:
-
Material Distortion:
- High temperatures during heat treatment can cause warping, distortion, or dimensional changes in materials, especially in complex or thin-walled components.
-
Energy Consumption:
- Heat treatment processes, particularly those requiring sustained high temperatures, can be energy-intensive, leading to higher operational costs.
-
Precision and Control:
- The process requires precise control of temperature, time, and cooling rates to achieve desired properties. Any deviation can result in inconsistent or suboptimal outcomes.
-
Cost and Complexity:
- Advanced heat treatment techniques, such as vacuum heat treatment or HIP, involve specialized equipment and expertise, increasing initial setup and maintenance costs.
-
Material Distortion:
-
Enhanced Benefits with HIP (Hot Isostatic Pressing):
-
Reduced Scrap and Improved Yield:
- HIP minimizes material waste by treating defects like porosity in castings, reducing the need for additional machining or rework.
-
Optimized Material Properties:
- By applying heat and pressure simultaneously, HIP improves material density, strength, and reliability, often eliminating the need for subsequent heat treatments.
-
Lightweight and High-Performance Parts:
- HIP enables the production of smaller, lighter-weight components with superior performance, making it ideal for aerospace and automotive applications.
-
Extended Service Life:
- Treated materials exhibit enhanced durability and resistance to fatigue, extending the lifespan of components.
-
Reduced Scrap and Improved Yield:
-
Applications and Industry Relevance:
- Heat treatment is widely used in industries such as automotive, aerospace, electronics, and construction. For example, it is essential for strengthening steel components in vehicles or improving the wear resistance of cutting tools.
- Advanced methods like vacuum heat treatment and HIP are particularly valuable in high-precision industries, where material integrity and performance are critical.
-
Future Trends and Innovations:
- The integration of automation and digital monitoring systems is improving the precision and efficiency of heat treatment processes.
- Sustainable practices, such as energy-efficient furnaces and recycling heat, are being adopted to reduce environmental impact.
In summary, heat treatment offers significant advantages in enhancing material properties and extending component life, but it also presents challenges like distortion and high energy use. Advanced techniques like vacuum heat treatment and HIP further enhance these benefits by improving efficiency, reducing waste, and optimizing material performance. As technology advances, heat treatment processes are likely to become even more precise, sustainable, and cost-effective.
Summary Table:
Aspect | Advantages | Limitations |
---|---|---|
Material Properties | Improves strength, hardness, ductility, and wear resistance. | High temperatures can cause distortion or warping. |
Stress Relief | Reduces internal stresses, making materials easier to machine or weld. | Requires precise control of temperature and cooling rates. |
Versatility | Applicable to steel, aluminum, ceramics, and more. | Energy-intensive processes increase operational costs. |
Advanced Techniques | Vacuum heat treatment and HIP improve efficiency and reduce material waste. | Specialized equipment and expertise increase setup and maintenance costs. |
Ready to optimize your heat treatment process? Contact our experts today to learn more!