Heat treatment is a critical process in manufacturing and materials engineering, offering a wide range of advantages that enhance the physical and mechanical properties of metals and alloys. By carefully controlling the heating and cooling processes, heat treatment can improve strength, durability, flexibility, and resistance to wear and corrosion. It also plays a vital role in relieving internal stresses, making materials easier to machine or weld, and enhancing electrical and magnetic properties. These benefits make heat treatment indispensable in industries such as automotive, aerospace, construction, and tool manufacturing, where material performance is paramount.
Key Points Explained:
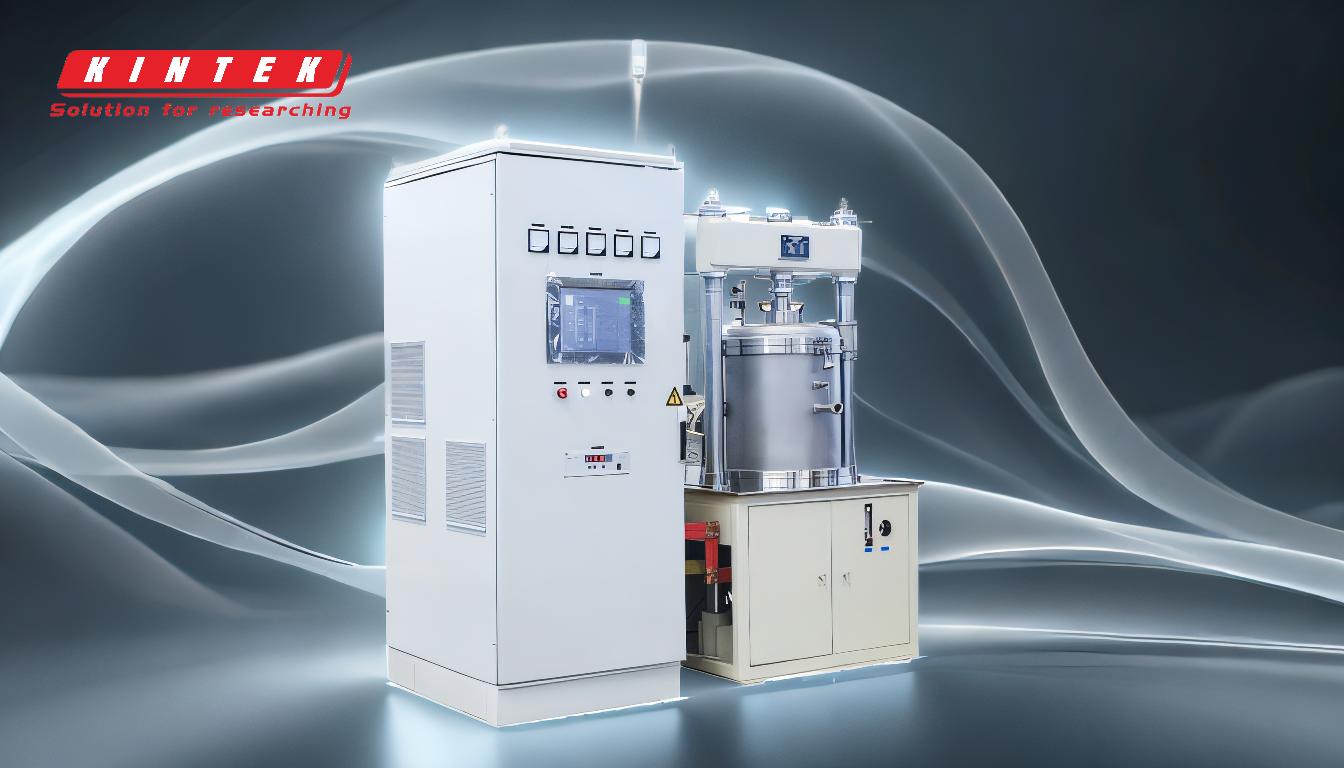
-
Improvement of Mechanical Properties:
- Heat treatment significantly enhances the mechanical properties of metals, including hardness, strength, toughness, ductility, and elasticity. This is achieved by altering the microstructure of the material through controlled heating and cooling.
- For example, processes like quenching and tempering can increase the hardness and strength of steel, making it suitable for high-stress applications such as gears and cutting tools.
-
Stress Relief and Improved Machinability:
- Heat treatment helps relieve internal stresses that develop during manufacturing processes like casting, welding, or machining. This stress relief makes the material easier to work with, reducing the risk of cracking or distortion during further processing.
- Annealing, a common heat treatment process, softens metals, making them more machinable and less prone to wear on cutting tools.
-
Enhanced Wear Resistance:
- By introducing wear-resistant characteristics, heat treatment extends the lifespan of components subjected to friction and abrasion. Processes like case hardening create a hard outer layer while maintaining a tough inner core, ideal for parts like bearings and gears.
- This dual-layer structure ensures that the component can withstand surface wear without compromising its overall strength.
-
Improved Brittleness and Flexibility:
- Heat treatment can reduce brittleness in metals, making them more flexible and less likely to fracture under impact. This is particularly important for materials used in dynamic or high-impact environments.
- Tempering, for instance, reduces the brittleness of hardened steel, improving its toughness and making it suitable for applications like springs and structural components.
-
Enhanced Electrical and Magnetic Properties:
- Certain heat treatment processes can improve the electrical conductivity and magnetic properties of metals. This is crucial for applications in the electronics and electrical industries, where materials like silicon steel are used in transformers and motors.
- By optimizing the grain structure, heat treatment can enhance the efficiency of electrical components.
-
Cost Efficiency and Uniform Heating:
- Furnace heat treatment is a cost-effective method when uniform heating of the entire part is required. It ensures consistent properties throughout the material, making it ideal for applications where distortion is not a concern.
- This uniformity is essential for components that must maintain precise dimensions and performance characteristics.
-
Versatility Across Materials and Applications:
- Heat treatment is applicable to both ferrous (iron-based) and non-ferrous metals (e.g., aluminum, copper, and titanium). This versatility allows it to be used in a wide range of industries, from automotive and aerospace to construction and tool manufacturing.
- Each material can be tailored to meet specific performance requirements, ensuring optimal functionality in its intended application.
-
Surface Hardening and Corrosion Resistance:
- Heat treatment can create a corrosion-resistant surface layer, extending the lifespan of components exposed to harsh environments. Processes like nitriding and carburizing introduce elements like nitrogen or carbon into the surface, enhancing its resistance to wear and corrosion.
- This is particularly beneficial for parts used in marine or chemical processing industries.
-
Support for Hot Forming and Post-Welding Processes:
- Heat treatment is particularly beneficial for steel materials undergoing hot forming or after welding. It helps restore the material's properties, ensuring it meets the required strength and durability standards.
- Post-weld heat treatment (PWHT) reduces residual stresses and improves the toughness of welded joints, preventing failures in critical applications.
-
Customization for Specific Applications:
- Heat treatment processes can be tailored to achieve specific outcomes based on the material and its intended use. This customization ensures that the final product meets precise performance criteria, whether it’s for high-strength applications or components requiring flexibility and wear resistance.
In summary, heat treatment is a versatile and essential process that enhances the performance, durability, and functionality of metals and alloys. Its ability to improve mechanical properties, relieve stresses, and introduce wear-resistant characteristics makes it indispensable in modern manufacturing and engineering.
Summary Table:
Advantage | Description |
---|---|
Improved Mechanical Properties | Enhances hardness, strength, toughness, ductility, and elasticity. |
Stress Relief | Reduces internal stresses, improving machinability and reducing cracking risks. |
Enhanced Wear Resistance | Extends component lifespan with wear-resistant surface layers. |
Improved Brittleness and Flexibility | Reduces brittleness, making metals more flexible and impact-resistant. |
Enhanced Electrical and Magnetic Properties | Improves conductivity and magnetic efficiency for electronics. |
Cost Efficiency and Uniform Heating | Ensures consistent properties with cost-effective uniform heating. |
Versatility Across Materials | Applicable to ferrous and non-ferrous metals for diverse industries. |
Surface Hardening and Corrosion Resistance | Creates corrosion-resistant layers for harsh environments. |
Support for Hot Forming and Post-Welding | Restores material properties after welding or hot forming. |
Customization for Specific Applications | Tailored processes to meet precise performance criteria. |
Optimize your materials with advanced heat treatment solutions—contact our experts today!