Carburizing is a widely used heat treatment process that enhances the surface hardness and wear resistance of low-carbon steel parts while maintaining a ductile core. This process involves diffusing carbon into the surface of the metal at high temperatures, followed by quenching to create a hard outer layer. Carburizing is applied across various industries, including automotive, aerospace, manufacturing, and tool production, to improve the durability and performance of components subjected to high stress, friction, or wear. The process is versatile, allowing for selective hardening of specific areas and preparation for further treatments like induction hardening.
Key Points Explained:
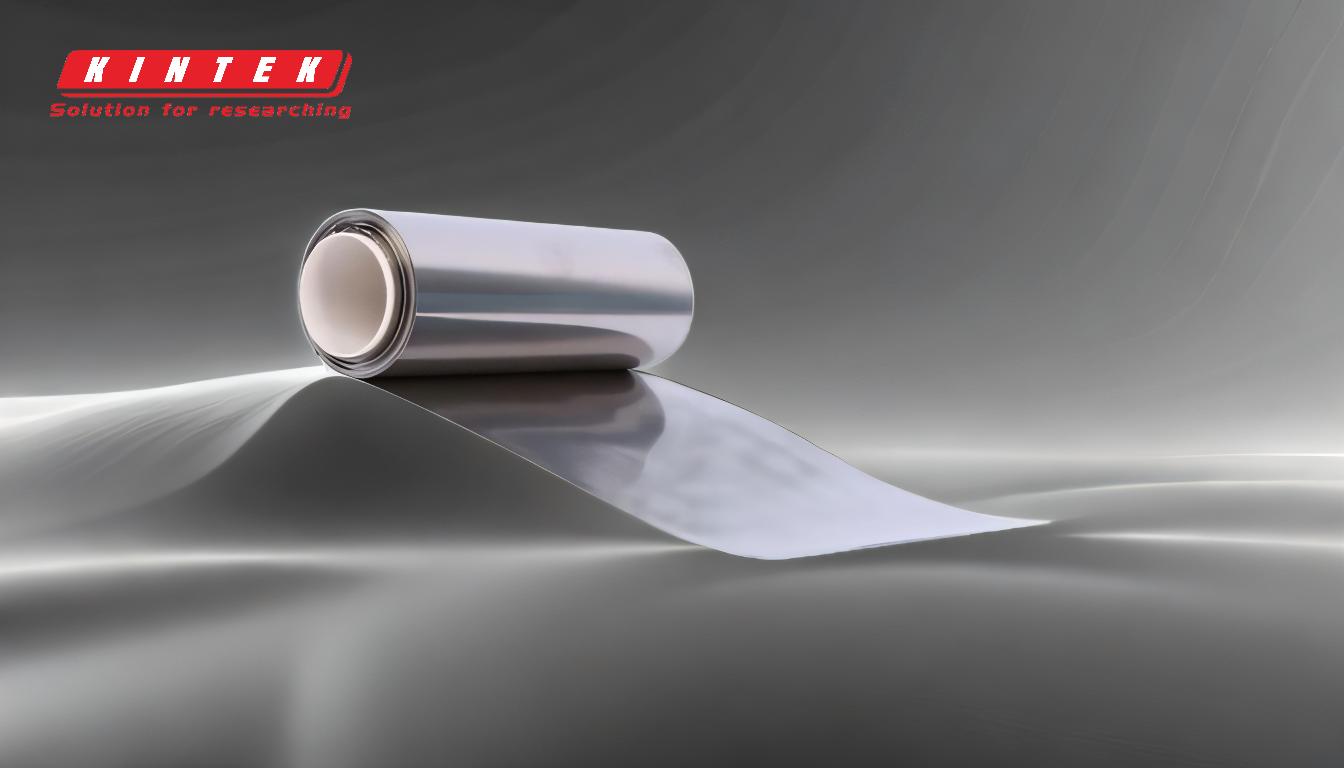
-
Surface Hardening for Wear Resistance
- Carburizing is primarily used to create a hard, wear-resistant surface on low-carbon steel parts. By diffusing carbon into the surface, the outer layer becomes significantly harder, making it ideal for components exposed to friction, abrasion, or impact.
- Applications include gears, shafts, bearings, and other mechanical parts in automotive and industrial machinery.
-
Ductile Core for Toughness
- While the surface becomes hard, the core of the part remains soft and ductile. This combination ensures that the component can withstand high stress without fracturing, making it suitable for parts that require both strength and flexibility.
- Examples include crankshafts, camshafts, and transmission components in vehicles.
-
Selective Hardening
- Carburizing can be applied to specific areas of a part by masking non-hardened regions with carbon-stopping paint. This allows manufacturers to tailor the hardness of components to their specific functional requirements.
- This technique is often used in complex parts where only certain surfaces need to be hardened, such as gear teeth or bearing races.
-
Preparation for Induction Hardening
- Carburizing is sometimes used as a precursor to induction hardening. By increasing the carbon content in the surface layer, the part becomes more responsive to subsequent hardening processes, resulting in even greater hardness and wear resistance.
- This is particularly useful in high-performance applications, such as heavy-duty machinery and aerospace components.
-
Improved Mechanical Properties
- The process enhances the microstructure and mechanical properties of the metal, including fatigue strength and resistance to deformation. This makes carburized parts more durable and longer-lasting in demanding environments.
- Applications include power generation components, medical devices, and tooling equipment.
-
Versatility Across Industries
- Carburizing is used in a wide range of industries, including automotive, aerospace, manufacturing, and medical device production. Its ability to improve surface hardness and wear resistance makes it indispensable for creating reliable and high-performance components.
- For example, aircraft landing gear, surgical instruments, and industrial cutting tools often undergo carburizing to meet stringent performance standards.
-
Typical Case Depths
- The depth of the hardened layer (case depth) typically ranges from 0.020″ to 0.050″, depending on the application. This ensures sufficient surface hardness while maintaining the core's ductility.
- Case depth is carefully controlled to meet the specific requirements of each component, such as load-bearing capacity and wear resistance.
-
Process Variations
- Carburizing can be performed using different methods, such as gas carburizing, liquid carburizing, and pack carburizing, each suited to specific applications and material types.
- For instance, gas carburizing is commonly used for high-volume production, while pack carburizing is preferred for smaller batches or specialized parts.
By understanding these key points, equipment and consumable purchasers can make informed decisions about when and how to use carburizing to meet their specific needs. The process's versatility, combined with its ability to enhance both surface hardness and core toughness, makes it a critical technique in modern manufacturing and engineering.
Summary Table:
Key Aspect | Description |
---|---|
Surface Hardening | Creates a hard, wear-resistant outer layer for components exposed to friction. |
Ductile Core | Maintains a soft, flexible core to withstand high stress without fracturing. |
Selective Hardening | Allows targeted hardening of specific areas using carbon-stopping paint. |
Induction Hardening Prep | Enhances responsiveness to subsequent hardening processes. |
Mechanical Properties | Improves fatigue strength, deformation resistance, and durability. |
Versatility | Used in automotive, aerospace, manufacturing, and medical device industries. |
Typical Case Depth | Ranges from 0.020″ to 0.050″, tailored to application needs. |
Process Variations | Includes gas, liquid, and pack carburizing for different applications. |
Discover how carburizing can optimize your components—contact our experts today!