Coreless type induction furnaces are versatile and widely used across various industries due to their ability to melt metals efficiently and precisely. These furnaces are particularly beneficial in industries that require high-quality metal melting, such as aerospace, automotive, medical, and tooling. They are also used in specialized applications like remelting electrodes and additive manufacturing. The vacuum induction furnace, a specific type of coreless induction furnace, is especially useful in industries that need high-purity metals and alloys, such as the aerospace and nuclear industries. Below, we explore the key applications and benefits of coreless type induction furnaces in detail.
Key Points Explained:
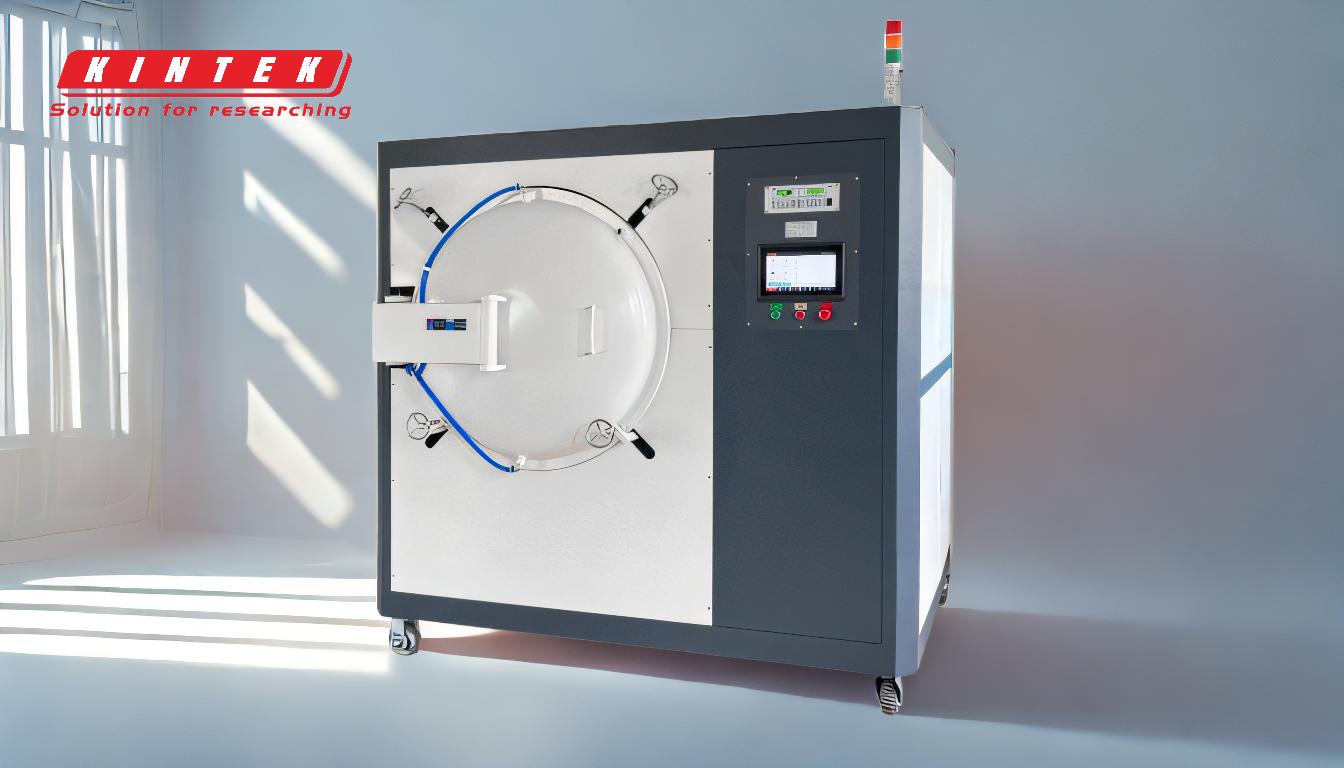
-
Aerospace Industry:
- Coreless induction furnaces, including vacuum induction furnaces, are crucial in the aerospace industry for melting and refining high-performance alloys like titanium and nickel-based superalloys. These materials are essential for manufacturing critical components such as turbine blades and engine parts, which require high strength, durability, and resistance to extreme temperatures.
- The vacuum environment in vacuum induction furnaces ensures that the metals are free from impurities, making them ideal for aerospace applications where material integrity is paramount.
-
Automotive Industry:
- In the automotive sector, coreless induction furnaces are used for heat treating components like gears, bearings, and engine parts. This process enhances the hardness and wear resistance of these components, leading to improved performance and longevity.
- The precise control over the melting process in coreless induction furnaces allows for the production of high-quality alloys that meet the stringent requirements of the automotive industry.
-
Medical and Pharmaceutical Industries:
- The medical industry benefits from coreless induction furnaces in the production of biocompatible and sterile medical devices, such as orthopedic implants and surgical instruments. The ability to melt and refine metals in a controlled environment ensures that the final products are free from contaminants and meet the high standards required for medical applications.
- Vacuum induction furnaces are particularly useful in this sector due to their ability to produce high-purity metals that are essential for medical devices.
-
Tool and Die Industry:
- Coreless induction furnaces are used in the tool and die industry for heat treating molds, dies, and cutting tools. This process enhances the hardness and wear resistance of these tools, making them more durable and efficient.
- The precise temperature control offered by coreless induction furnaces ensures that the tools are treated uniformly, leading to consistent quality and performance.
-
Electronics and Semiconductor Industry:
- In the electronics and semiconductor industry, coreless induction furnaces are used for processes like diffusion bonding and sintering. These processes are essential for producing high-performance electronic components that require precise thermal control.
- The ability to melt and refine metals in a controlled environment ensures that the final products meet the high standards required for electronic applications.
-
Energy and Power Generation:
- Coreless induction furnaces are used in the energy and power generation industry for producing components like turbine blades and heat exchangers. These components require high temperature and corrosion resistance, which can be achieved through the precise melting and refining processes offered by coreless induction furnaces.
- Vacuum induction furnaces are particularly useful in this sector due to their ability to produce high-purity metals that are essential for energy applications.
-
Research and Development:
- Coreless induction furnaces are widely used in research and development for studying material behavior under controlled thermal conditions. The ability to precisely control the melting process allows researchers to develop new materials and improve existing ones.
- Vacuum induction furnaces are particularly useful in R&D due to their ability to produce high-purity metals and alloys, which are essential for advanced material research.
-
Additive Manufacturing:
- Coreless induction furnaces are used in additive manufacturing processes like Rapid Induction Printing. In this process, a conductive wire feedstock is subjected to induction heating and ejected as a liquid, which then solidifies to form three-dimensional metal structures.
- This process offers greater energy and material efficiency, as well as a higher degree of safety compared to other additive manufacturing methods.
In summary, coreless type induction furnaces, including vacuum induction furnaces, are indispensable tools across a wide range of industries. Their ability to melt and refine metals with precision and control makes them ideal for applications that require high-quality materials, such as aerospace, automotive, medical, and tooling industries. Additionally, their use in research and development and additive manufacturing highlights their versatility and importance in advancing technology and material science.
Summary Table:
Industry | Applications |
---|---|
Aerospace | Melting high-performance alloys for turbine blades and engine parts. |
Automotive | Heat treating gears, bearings, and engine components for enhanced durability. |
Medical & Pharmaceutical | Producing biocompatible implants and sterile surgical instruments. |
Tool & Die | Heat treating molds, dies, and cutting tools for improved hardness. |
Electronics & Semiconductor | Diffusion bonding and sintering for high-performance electronic components. |
Energy & Power Generation | Manufacturing turbine blades and heat exchangers with corrosion resistance. |
Research & Development | Studying material behavior and developing advanced alloys. |
Additive Manufacturing | Rapid Induction Printing for energy-efficient 3D metal structures. |
Discover how coreless induction furnaces can elevate your operations—contact us today for expert advice!