Metal sintering is a versatile and efficient manufacturing process that offers numerous benefits, making it a preferred choice in various industries. It allows for the production of complex shapes and intricate designs while conserving materials and energy. The process enhances mechanical properties, such as strength and durability, and provides excellent control over material composition and porosity. Additionally, metal sintering is cost-effective, sustainable, and suitable for a wide range of applications, from electrical components to medical devices. Its ability to produce high-quality, consistent products with minimal waste makes it a valuable technique in modern manufacturing.
Key Points Explained:
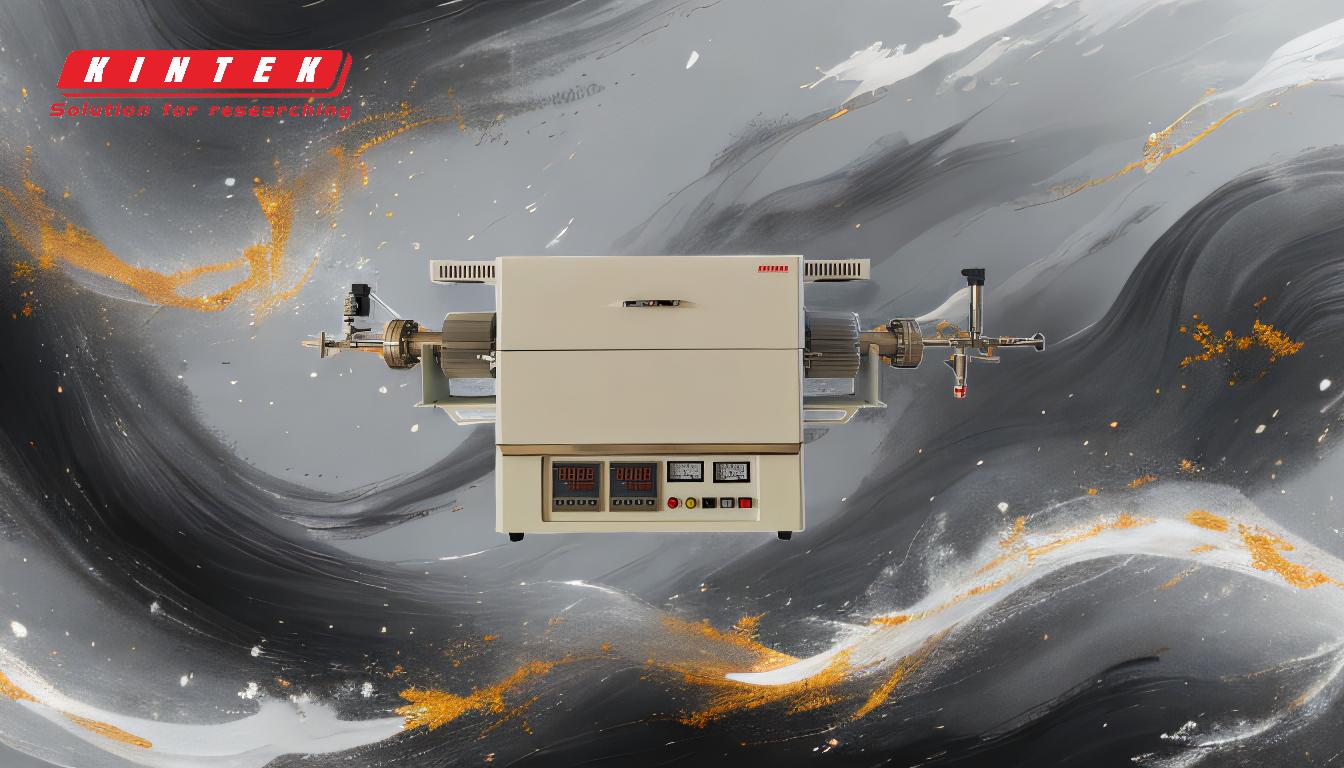
-
Complex Shapes and Intricate Designs:
- Metal sintering enables the production of components with complex geometries that would be difficult or impossible to achieve with traditional manufacturing methods. This is particularly beneficial for industries requiring precision parts, such as aerospace, automotive, and medical devices.
-
Improved Mechanical Properties:
- Sintering enhances the strength, durability, and wear resistance of metal parts. The process minimizes surface porosity, leading to denser and more robust components. This makes sintered metals ideal for high-stress applications like turbine blades and structural steel parts.
-
Material Conservation and Sustainability:
- The process produces minimal waste, as it uses metal powders that are compacted and fused together. This makes sintering an environmentally friendly option compared to traditional machining, which generates significant material waste.
-
Cost-Effectiveness:
- Sintering reduces production costs by minimizing material waste and simplifying manufacturing processes. It also eliminates the need for additional machining steps, as parts are often produced in near-net shapes.
-
Versatility in Material Selection:
- Metal sintering can be applied to a wide range of materials, including high-melting-point metals, alloys, and composites. This flexibility allows manufacturers to tailor material properties to specific applications, such as self-lubricating bearings or magnetic materials.
-
Energy Efficiency:
- The sintering process requires less energy compared to traditional melting and casting methods. This contributes to lower operational costs and a reduced environmental footprint.
-
Enhanced Control and Consistency:
- Sintering provides precise control over grain size, porosity, and material composition, resulting in highly uniform and repeatable products. This consistency is critical for industries like electronics and medical devices, where reliability is paramount.
-
Applications Across Industries:
- Sintered metals are used in a variety of applications, including electrical components, semiconductors, optical fibers, and custom metal forms for 3D printing. They are also essential in creating porous metals for filtering, tungsten wiring, and cutting tools.
-
Improved Part Appearance:
- The sintering process produces parts with smooth surfaces and fine details, enhancing their aesthetic appeal. This is particularly important for consumer products and decorative items.
-
Ability to Work with Difficult Materials:
- Sintering is capable of processing materials with very high melting points, such as tungsten and molybdenum, which are challenging to work with using conventional methods. This expands the range of materials available for advanced engineering applications.
In summary, metal sintering is a highly advantageous process that combines efficiency, sustainability, and versatility. Its ability to produce high-quality, complex components with minimal waste makes it a cornerstone of modern manufacturing across diverse industries.
Summary Table:
Benefit | Description |
---|---|
Complex Shapes & Designs | Enables intricate geometries for precision parts in aerospace, automotive, etc. |
Improved Mechanical Properties | Enhances strength, durability, and wear resistance of metal parts. |
Material Conservation | Minimizes waste, making it an eco-friendly manufacturing option. |
Cost-Effectiveness | Reduces production costs and eliminates additional machining steps. |
Versatility in Materials | Works with high-melting-point metals, alloys, and composites. |
Energy Efficiency | Requires less energy compared to traditional methods. |
Enhanced Control & Consistency | Ensures uniform grain size, porosity, and material composition. |
Wide Industry Applications | Used in electronics, medical devices, 3D printing, and more. |
Improved Part Appearance | Produces smooth surfaces and fine details for aesthetic appeal. |
Handles Difficult Materials | Processes high-melting-point metals like tungsten and molybdenum. |
Learn how metal sintering can transform your manufacturing process—contact our experts today!