PVD (Physical Vapor Deposition) plating offers a wide variety of colors, ranging from metallic shades like gold, rose gold, and bronze to non-metallic colors such as black, blue, green, and red. The specific color achieved depends on the material being vaporized (target) and the conditions of the deposition process, including the mixture of reactive gases used. PVD coatings are known for their high purity, uniformity, and excellent adhesion, making them durable and resistant to corrosion, abrasion, and high temperatures. These coatings are available in polished, satin, or matte finishes, providing versatility for various applications.
Key Points Explained:
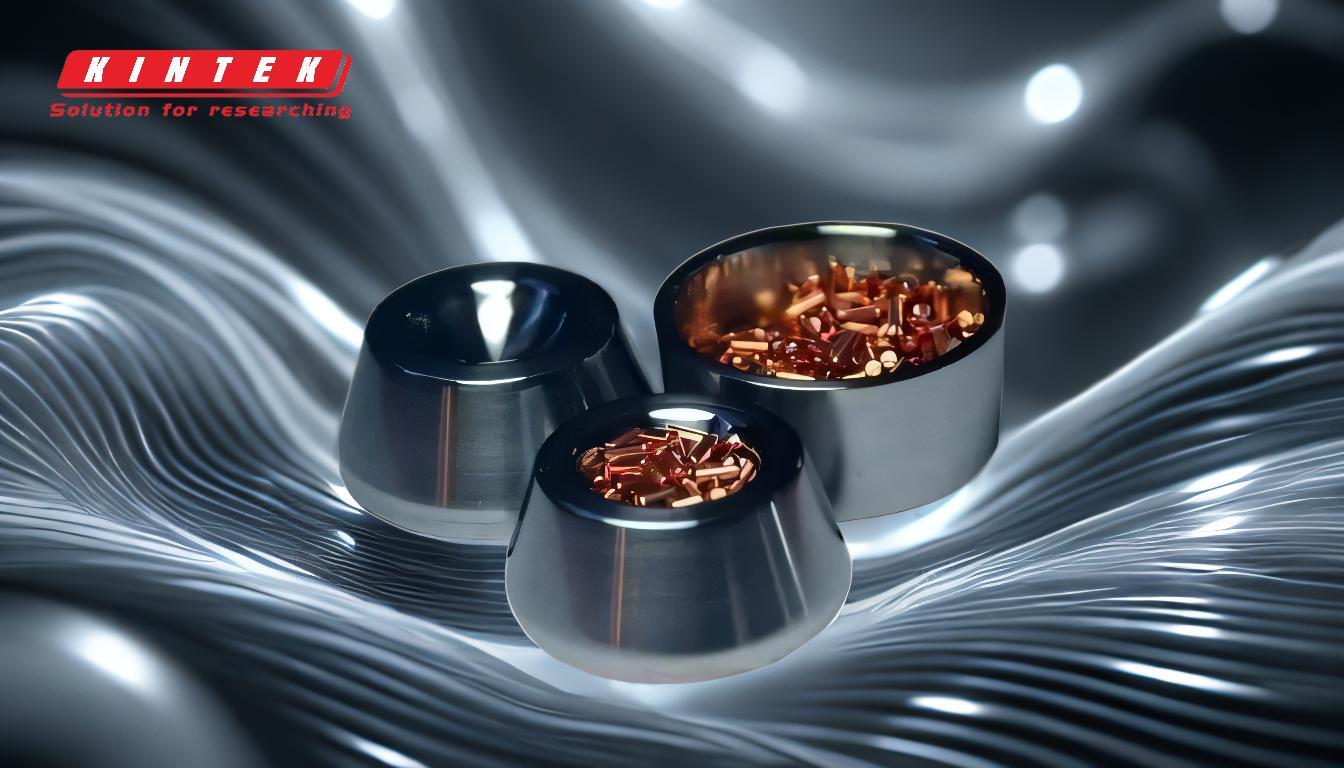
-
Range of Colors Available in PVD Plating:
- PVD plating can produce a wide spectrum of colors, including:
- Metallic Colors: Gold, rose gold, chrome, brass, nickel, copper, bronze, and silver white.
- Non-Metallic Colors: Black, blue, green, red, purple, brown, burgundy, and smoky shades.
- These colors are achieved by varying the evaporated metal (target) and the reactive gases used during the deposition process.
- PVD plating can produce a wide spectrum of colors, including:
-
Factors Influencing Color in PVD Plating:
- Target Material: The type of metal being vaporized (e.g., titanium, zirconium, or chromium) plays a significant role in determining the final color.
- Reactive Gases: The mixture of gases (e.g., nitrogen, oxygen, or acetylene) introduced during the process can alter the color. For example, nitrogen can produce gold or bronze tones, while oxygen can create black or blue hues.
- Deposition Conditions: Parameters like temperature, pressure, and deposition time also influence the color outcome.
-
Finishes Available:
- PVD coatings can be applied in different finishes to suit aesthetic and functional requirements:
- Polished: Provides a high-gloss, reflective surface.
- Satin: Offers a soft, brushed appearance.
- Matte: Delivers a non-reflective, smooth finish.
- PVD coatings can be applied in different finishes to suit aesthetic and functional requirements:
-
Applications and Advantages of PVD Coatings:
- Applications: PVD coatings are used in industries such as automotive, jewelry, watches, hardware, and consumer electronics due to their aesthetic appeal and durability.
-
Advantages:
- Durability: PVD coatings are harder and more corrosion-resistant than traditional electroplating.
- Aesthetic Versatility: The wide range of colors and finishes makes PVD suitable for decorative and functional purposes.
- Environmental Benefits: PVD is an eco-friendly process with minimal waste and no harmful chemicals.
-
Limitations of PVD Coatings:
- Coating Uniformity: PVD coatings may have poor performance on the back and sides of tools due to low air pressure during deposition.
- Thickness: The film thickness is typically around 2.5 μm, which may limit certain applications requiring thicker coatings.
-
Cost-Effectiveness:
- PVD coatings provide an affordable alternative to pure metals while offering similar or superior aesthetic and functional properties. This makes them a popular choice for manufacturers and designers.
By understanding these key points, purchasers and designers can make informed decisions about using PVD plating to achieve the desired color, finish, and performance for their specific applications.
Summary Table:
Aspect | Details |
---|---|
Metallic Colors | Gold, rose gold, chrome, brass, nickel, copper, bronze, silver white |
Non-Metallic Colors | Black, blue, green, red, purple, brown, burgundy, smoky shades |
Finishes Available | Polished (high-gloss), satin (brushed), matte (non-reflective) |
Applications | Automotive, jewelry, watches, hardware, consumer electronics |
Advantages | Durability, corrosion resistance, aesthetic versatility, eco-friendly |
Limitations | Coating uniformity, limited thickness (2.5 μm) |
Ready to explore the possibilities of PVD plating for your project? Contact us today to get started!