The heat treatment process is a critical step in metallurgy, significantly influencing the properties and performance of metal parts. The success of this process depends on several key factors, including temperature control, time management, cooling rates, and environmental conditions. These variables must be carefully adjusted based on the type of material, the desired properties, and the part's end application. Additionally, uniform temperature distribution, proper gas circulation, and cycle optimization are essential to ensure high-quality outcomes. Anticipating potential issues and maintaining precise control over the process can prevent defects, reduce downtime, and enhance the overall efficiency of heat treatment.
Key Points Explained:
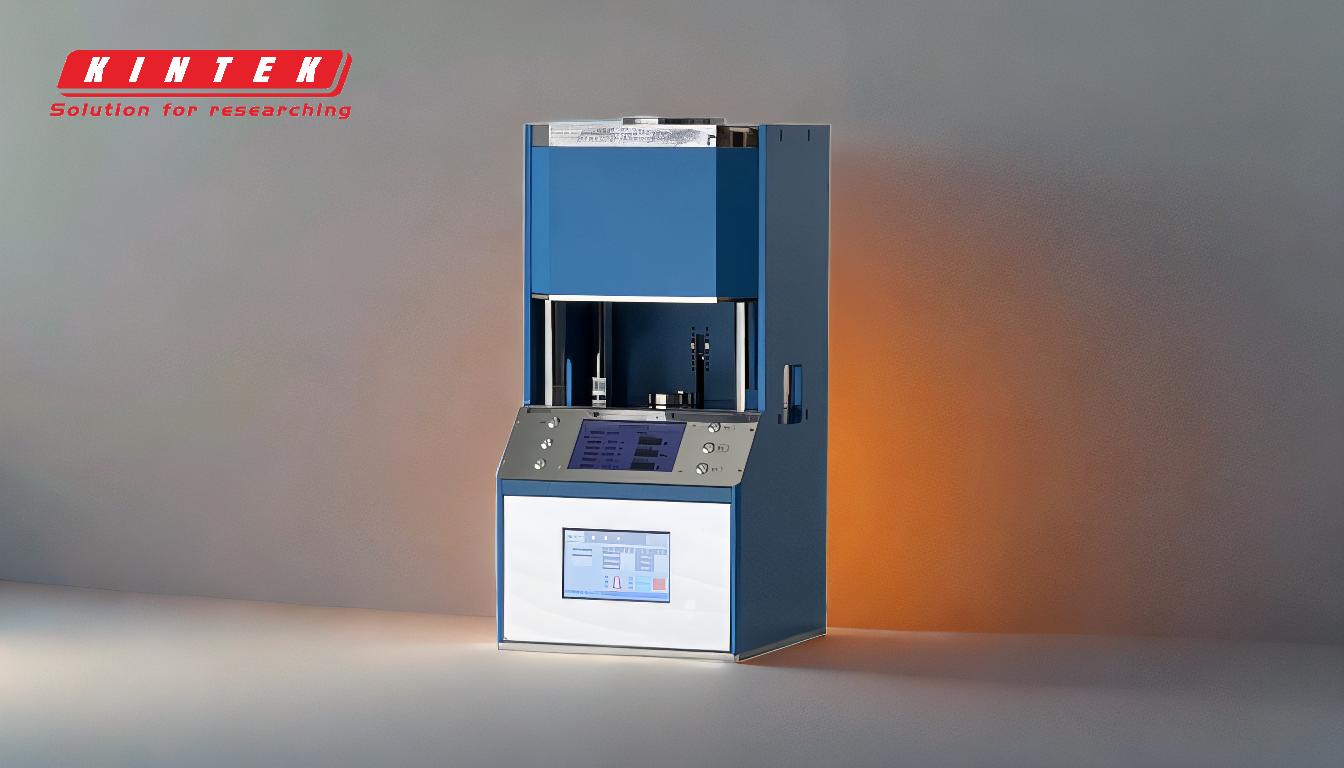
-
Temperature Control:
- Importance: Temperature is one of the most critical factors in heat treatment. It determines the phase transformations in the metal, which directly affect its mechanical properties.
- Details: The metal must be heated to a specific temperature range, often with tight tolerances, to achieve the desired microstructure. Exceeding or falling short of this range can lead to inadequate hardening, softening, or even cracking.
- Considerations: The maximum temperature, heat-up rate, and cool-down rate must be carefully controlled to avoid metallurgical defects and ensure uniform transformation.
-
Time at Temperature:
- Importance: The duration for which the metal is held at the target temperature influences the extent of phase transformation and diffusion processes.
- Details: Holding the metal at the desired temperature allows for uniform heating and ensures that the entire part reaches the necessary state. Insufficient time can result in incomplete transformation, while excessive time may lead to grain growth or other undesirable effects.
- Considerations: The time at temperature must be optimized based on the material type, part size, and desired properties.
-
Cooling Rate and Method:
- Importance: The cooling rate determines the final microstructure and hardness of the metal.
- Details: Rapid cooling (quenching) is often used to achieve high hardness, while slower cooling (annealing) is employed to soften the metal and improve ductility. The choice of cooling medium (air, oil, water, or gas) and the rate of cooling must be tailored to the material and desired outcome.
- Considerations: Improper cooling can cause distortion, residual stresses, or cracking. Precise control over the cooling process is essential to achieve the desired mechanical properties.
-
Material Type and Part Size:
- Importance: Different materials and part sizes require specific heat treatment parameters to achieve optimal results.
- Details: For example, carbon steels, alloy steels, and non-ferrous metals each have unique heat treatment requirements. Larger parts may require longer heating times to ensure uniform temperature distribution.
- Considerations: The heat treatment process must be customized based on the material's composition, part geometry, and intended application.
-
Uniform Temperature Distribution:
- Importance: Uniform heating ensures consistent properties throughout the part.
- Details: Hot zones in the furnace must maintain a consistent temperature to prevent uneven transformation. Variations in temperature can lead to soft spots, warping, or other defects.
- Considerations: Proper furnace design, insulation, and heat distribution systems are critical to achieving uniform heating.
-
Gas Circulation and Atmosphere Control:
- Importance: The atmosphere in the furnace can affect the surface chemistry and properties of the metal.
- Details: In processes like carburizing or nitriding, the gas composition (e.g., partial pressure of carbon or nitrogen) must be precisely controlled to achieve the desired surface hardness and case depth. Inert gases may be used to prevent oxidation or decarburization.
- Considerations: Proper gas circulation ensures consistent results and prevents contamination or surface defects.
-
Cycle Optimization:
- Importance: Efficient heat treatment cycles reduce energy consumption and processing time while maintaining quality.
- Details: Balancing heating, holding, and cooling times is essential to minimize process duration without compromising metallurgical outcomes. Advanced control systems can optimize cycles based on real-time data.
- Considerations: Anticipating potential issues, such as equipment malfunctions or process deviations, can prevent costly downtime and ensure consistent quality.
-
End Application and Property Requirements:
- Importance: The heat treatment process must align with the part's intended use and performance requirements.
- Details: For example, a part requiring high wear resistance may undergo hardening and tempering, while a part needing improved machinability may be annealed. Localized heat treatment may be applied to specific areas of a part to achieve targeted properties.
- Considerations: Understanding the end application helps in selecting the appropriate heat treatment method and parameters.
-
Maintenance and Downtime Prevention:
- Importance: Regular maintenance and process monitoring can prevent defects and reduce downtime.
- Details: Anticipating potential problems, such as furnace malfunctions or gas leaks, ensures uninterrupted production. Predictive maintenance strategies can identify issues before they escalate.
- Considerations: Investing in reliable equipment and training personnel to monitor and maintain the heat treatment process can enhance overall efficiency and product quality.
By carefully considering these factors, manufacturers can optimize the heat treatment process to achieve the desired material properties, improve product performance, and reduce costs.
Summary Table:
Key Factor | Importance | Details |
---|---|---|
Temperature Control | Determines phase transformations and mechanical properties. | Requires precise heating within tight tolerances to avoid defects like cracking or softening. |
Time at Temperature | Influences phase transformation and diffusion processes. | Must be optimized based on material type, part size, and desired properties. |
Cooling Rate and Method | Determines final microstructure and hardness. | Rapid cooling (quenching) for hardness; slower cooling (annealing) for ductility. |
Material Type and Part Size | Different materials and sizes require specific parameters. | Customize process based on composition, geometry, and application. |
Uniform Temperature Distribution | Ensures consistent properties throughout the part. | Proper furnace design and heat distribution prevent uneven transformation. |
Gas Circulation and Atmosphere Control | Affects surface chemistry and properties. | Precise gas composition prevents oxidation or contamination. |
Cycle Optimization | Reduces energy consumption and processing time. | Advanced control systems optimize heating, holding, and cooling cycles. |
End Application and Property Requirements | Aligns process with part performance needs. | Hardening for wear resistance; annealing for machinability. |
Maintenance and Downtime Prevention | Prevents defects and reduces downtime. | Predictive maintenance strategies ensure uninterrupted production. |
Optimize your heat treatment process today—contact our experts for tailored solutions!