Hot pressing is a widely used technique in materials science, particularly for sintering ceramics and other hard materials. It involves applying heat and pressure simultaneously to a powder or preform to achieve densification and sintering in a single step. This method is especially useful for materials that are difficult to sinter using conventional methods. Below, we explore the different types of hot pressing, their characteristics, and their advantages and disadvantages.
Key Points Explained:
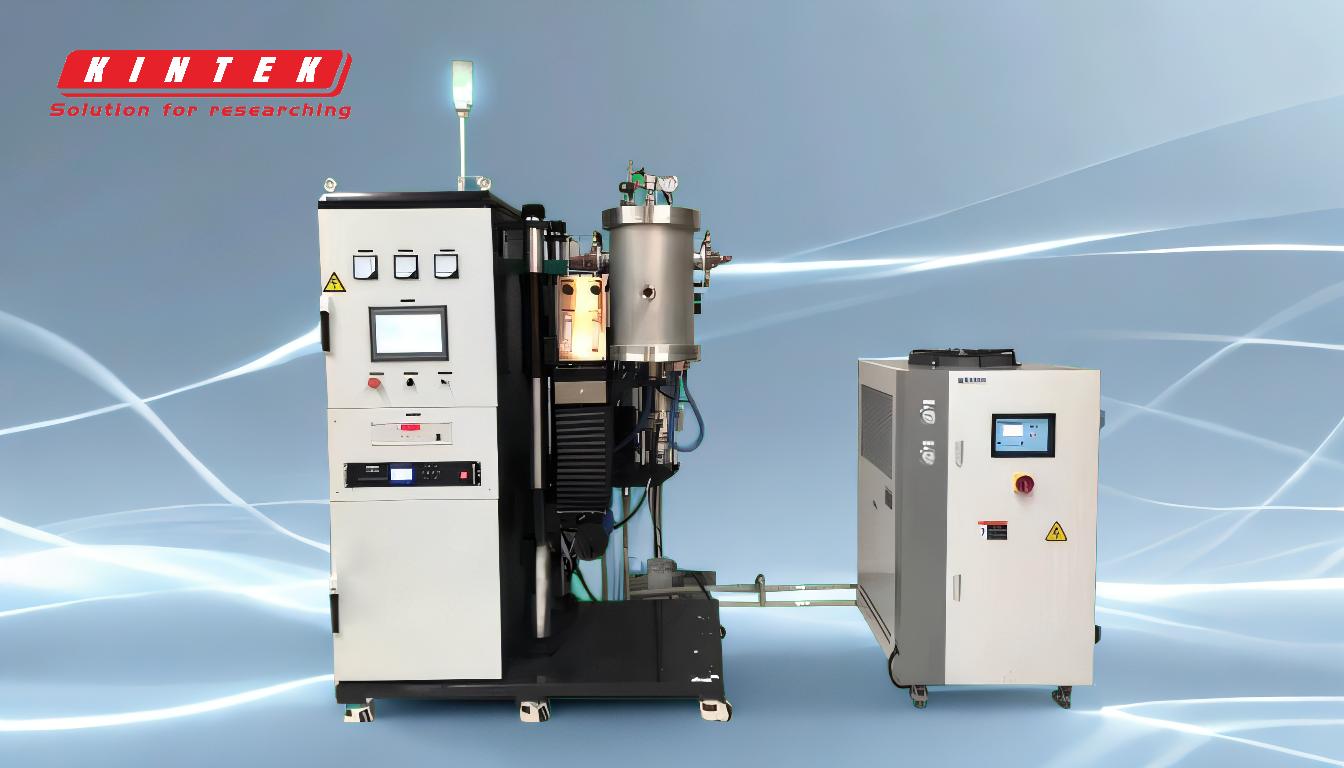
-
Hot Press Sintering:
- Process: In hot press sintering, silicon carbide powder or other materials are placed into a mold. The mold is then heated while maintaining a specific pressure, allowing the material to densify and sinter simultaneously.
-
Characteristics:
- Simultaneous application of heat and pressure.
- Controlled pressure-temperature-time conditions ensure precise sintering.
-
Disadvantages:
- Complex machinery is required.
- High demands on mold materials.
- Strict production process requirements.
- High energy consumption.
- Low production efficiency.
- High production costs.
-
Types of Hot Pressing:
-
Uniaxial Hot Pressing:
- Description: Pressure is applied in a single direction, typically using a hydraulic press. This is the most common type of hot pressing.
- Applications: Used for producing simple shapes like discs, plates, and blocks.
- Advantages: Simplicity of the process and equipment.
- Disadvantages: Limited to simple geometries and may result in density gradients.
-
Isostatic Hot Pressing (HIP):
- Description: Pressure is applied uniformly from all directions using a gas or liquid medium. This method is also known as hot isostatic pressing.
- Applications: Ideal for complex shapes and components requiring uniform density.
- Advantages: Produces parts with uniform density and improved mechanical properties.
- Disadvantages: More complex and expensive equipment compared to uniaxial hot pressing.
-
Spark Plasma Sintering (SPS):
- Description: A rapid sintering technique where a pulsed electric current is passed through the material, generating heat internally. Pressure is applied simultaneously.
- Applications: Suitable for advanced ceramics, nanomaterials, and composites.
- Advantages: Very fast sintering times, lower temperatures, and fine microstructures.
- Disadvantages: High equipment costs and limited to small-scale production.
-
Hot Forging:
- Description: A form of hot pressing where the material is deformed plastically under high temperature and pressure to achieve the desired shape.
- Applications: Used for metals and alloys to produce high-strength components.
- Advantages: Improved mechanical properties and grain refinement.
- Disadvantages: Requires high temperatures and precise control over deformation.
-
-
Advantages of Hot Pressing:
- Enhanced Densification: The combination of heat and pressure leads to higher densification compared to conventional sintering.
- Improved Mechanical Properties: Hot-pressed materials often exhibit superior mechanical properties such as higher strength and toughness.
- Reduced Sintering Time: The simultaneous application of heat and pressure can significantly reduce the time required for sintering.
-
Disadvantages of Hot Pressing:
- High Equipment Costs: The machinery required for hot pressing, especially for HIP and SPS, is expensive.
- Energy Consumption: The process is energy-intensive, particularly for high-temperature applications.
- Limited Production Efficiency: Hot pressing is generally slower and less efficient than other sintering methods, making it less suitable for large-scale production.
-
Applications of Hot Pressing:
- Ceramics: Used for sintering advanced ceramics such as silicon carbide, alumina, and zirconia.
- Composites: Ideal for producing metal matrix composites and ceramic matrix composites.
- Metals: Used for hot forging of metals and alloys to produce high-strength components.
- Nanomaterials: SPS is particularly useful for sintering nanomaterials due to its rapid heating and cooling rates.
In summary, hot pressing is a versatile technique with several variants, each suited to specific applications and materials. While it offers significant advantages in terms of material properties and densification, it also comes with challenges such as high costs and energy consumption. Understanding the different types of hot pressing and their respective advantages and disadvantages is crucial for selecting the appropriate method for a given application.
Summary Table:
Type of Hot Pressing | Description | Applications | Advantages | Disadvantages |
---|---|---|---|---|
Uniaxial Hot Pressing | Pressure applied in a single direction using a hydraulic press. | Simple shapes like discs, plates, and blocks. | Simple process and equipment. | Limited to simple geometries; may result in density gradients. |
Isostatic Hot Pressing (HIP) | Pressure applied uniformly from all directions using a gas or liquid medium. | Complex shapes and components requiring uniform density. | Uniform density and improved mechanical properties. | Expensive and complex equipment. |
Spark Plasma Sintering (SPS) | Rapid sintering with pulsed electric current and simultaneous pressure. | Advanced ceramics, nanomaterials, and composites. | Fast sintering, lower temperatures, and fine microstructures. | High equipment costs; limited to small-scale production. |
Hot Forging | Material deformed plastically under high temperature and pressure. | Metals and alloys for high-strength components. | Improved mechanical properties and grain refinement. | Requires high temperatures and precise control over deformation. |
Need help choosing the right hot pressing technique for your materials? Contact our experts today!