Coreless induction furnaces, while offering advantages such as precise temperature control, even heat distribution, and flexibility in alloy changes, come with notable disadvantages. The primary drawbacks include reduced power efficiency (approximately 75%) compared to core-type furnaces, which can achieve up to 98% efficiency. Additionally, frequent alloy changes can accelerate wear on the refractory lining, reducing its operational lifespan. The absence of a flux-concentrating core in coreless furnaces further contributes to their lower efficiency. These factors make coreless induction furnaces less suitable for high-throughput operations or environments requiring continuous production with minimal downtime.
Key Points Explained:
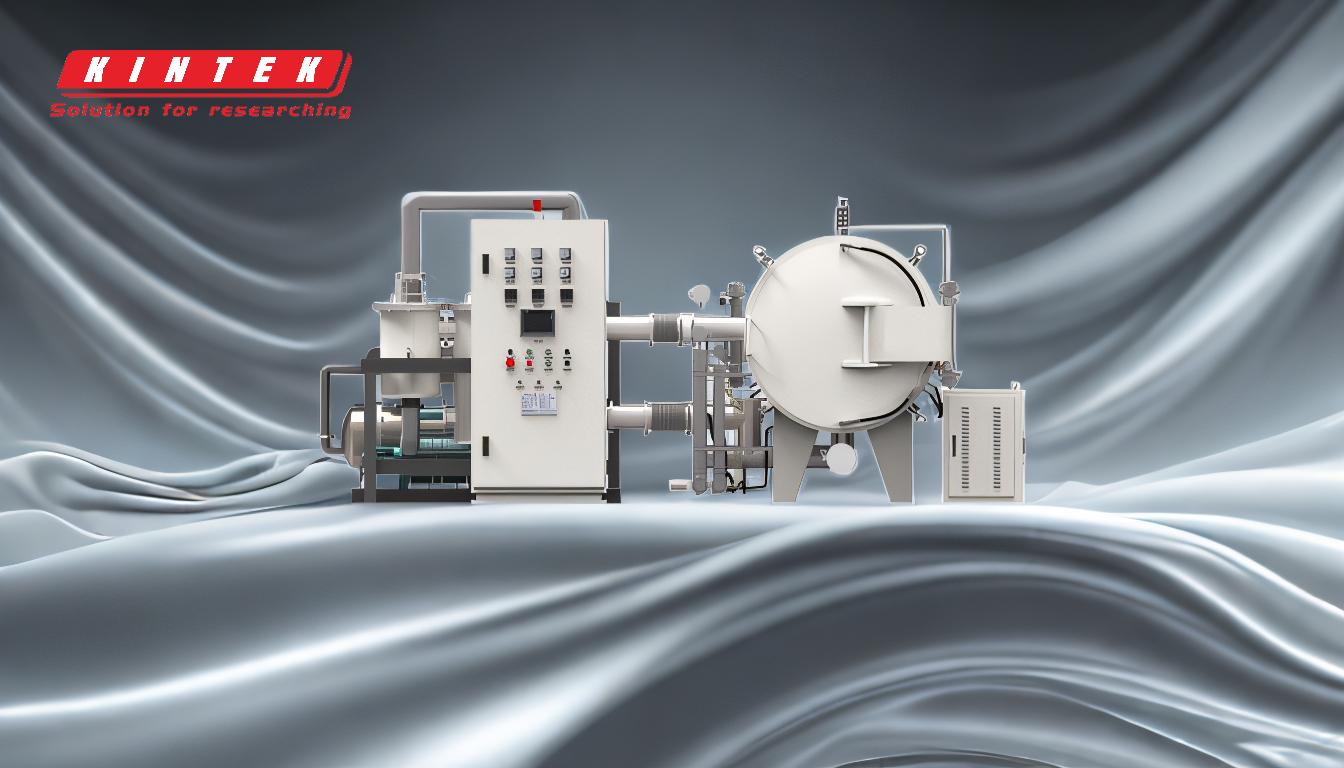
-
Reduced Power Efficiency
- Coreless induction furnaces operate at approximately 75% power efficiency, significantly lower than core-type furnaces, which can achieve up to 98% efficiency.
- The absence of a flux-concentrating core in coreless furnaces leads to energy losses, as the magnetic field is less effectively concentrated on the metal charge.
- This lower efficiency translates to higher energy consumption and operational costs, making coreless furnaces less economical for high-throughput or energy-intensive applications.
-
Refractory Lining Wear
- Frequent alloy changes, a common practice in coreless furnaces, can accelerate the degradation of the refractory lining.
- The refractory lining is exposed to thermal cycling and chemical reactions with different alloys, leading to cracks, erosion, and reduced lifespan.
- Replacing the refractory lining is costly and time-consuming, increasing maintenance expenses and downtime.
-
Limited Suitability for Continuous Operations
- Coreless induction furnaces are designed for flexibility, allowing them to be shut down and started cold, which is advantageous for alloy changes.
- However, this design makes them less suitable for continuous, high-production operations where maintaining a constant molten metal pool is essential.
- Core-type furnaces, in contrast, are better suited for such applications due to their higher efficiency and ability to operate continuously.
-
Higher Energy Consumption
- The lower efficiency of coreless furnaces means more energy is required to achieve the same melting results as core-type furnaces.
- This increased energy demand can lead to higher operational costs, particularly in regions with expensive electricity.
- For businesses aiming to minimize energy expenses, coreless furnaces may not be the most cost-effective option.
-
Cooling System Dependency
- Coreless induction furnaces rely on water-cooled copper coils to prevent overheating during operation.
- The cooling system adds complexity to the furnace design and requires regular maintenance to ensure proper functioning.
- Any failure in the cooling system can lead to coil damage or furnace shutdown, disrupting production.
-
Operational Limitations
- While coreless furnaces offer flexibility in terms of alloy changes and frequency range (50 Hz to 10 kHz), they are less efficient at lower frequencies.
- Core-type furnaces, with their higher efficiency, are better suited for applications requiring consistent performance across a wide range of frequencies.
In summary, while coreless induction furnaces provide excellent control over temperature and metal chemistry, their reduced power efficiency, susceptibility to refractory lining wear, and higher energy consumption make them less ideal for high-throughput or continuous operations. These disadvantages should be carefully considered when selecting a furnace for specific industrial applications.
Summary Table:
Disadvantage | Description |
---|---|
Reduced Power Efficiency | Operates at ~75% efficiency vs. 98% in core-type furnaces, leading to higher energy consumption. |
Refractory Lining Wear | Frequent alloy changes accelerate lining degradation, increasing maintenance costs and downtime. |
Limited for Continuous Use | Less suitable for high-throughput or continuous operations due to design limitations. |
Higher Energy Consumption | Lower efficiency increases operational costs, especially in regions with expensive electricity. |
Cooling System Dependency | Relies on water-cooled coils, adding complexity and maintenance needs. |
Operational Limitations | Less efficient at lower frequencies, making core-type furnaces better for consistent performance. |
Need help choosing the right furnace for your needs? Contact our experts today!