The heat treating process is a critical method used to alter the physical and sometimes chemical properties of materials, primarily metals, to achieve desired characteristics such as increased strength, hardness, or ductility. The process typically involves four key steps: heating the material to a specific temperature, holding it at that temperature for a predetermined time, cooling it according to specified methods, and sometimes performing additional steps like tempering or stress relieving to fine-tune the material's properties. These steps are essential for ensuring the material meets the required performance standards for its intended application.
Key Points Explained:
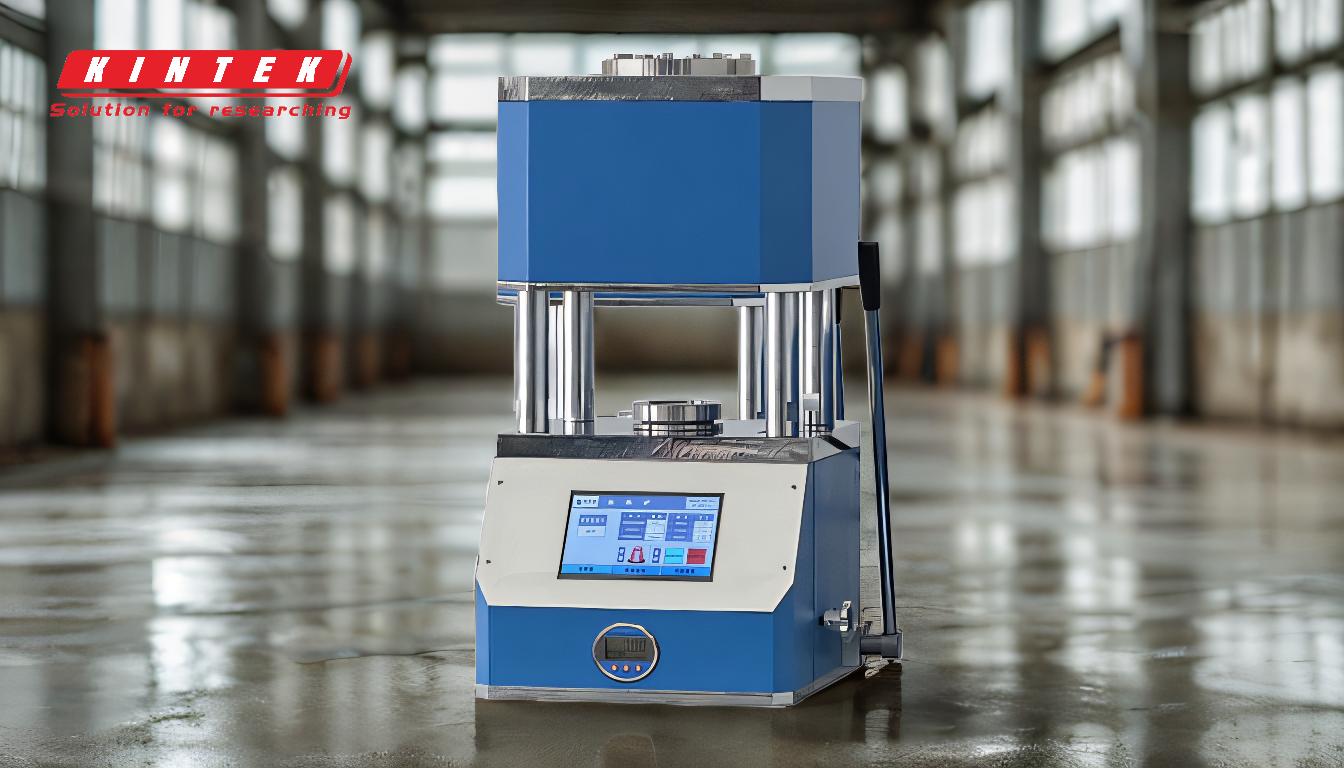
-
Heating to a Specified Temperature
- The first step in the heat treating process involves heating the material to a precise temperature. This temperature varies depending on the material and the desired outcome. For example, annealing typically requires lower temperatures compared to hardening processes.
- Heating can be done in various furnaces, such as electric, gas, or induction furnaces, depending on the material and the scale of production.
- The temperature range can be as high as 2,400°F (1,315°C) for certain alloys, ensuring the material reaches the necessary phase transformation or recrystallization state.
-
Holding at the Specified Temperature
- Once the material reaches the desired temperature, it is held at that temperature for a specific duration. This step ensures uniformity in the material's microstructure and allows for complete transformation or diffusion processes.
- The holding time can range from a few seconds for thin materials to several hours or even days for thicker or more complex components.
- This step is critical for achieving consistent results, as insufficient time can lead to incomplete transformations, while excessive time may cause grain growth or other undesirable effects.
-
Cooling According to Prescribed Methods
- After the material has been held at the specified temperature, it is cooled using controlled methods. The cooling rate is crucial and varies depending on the desired properties. For example, rapid cooling (quenching) is used to harden metals, while slow cooling is employed for annealing to soften them.
- Cooling methods include air cooling, oil quenching, water quenching, or furnace cooling, each chosen based on the material and the required outcome.
- Improper cooling can lead to issues such as cracking, warping, or residual stresses, making this step vital for the success of the heat treating process.
-
Additional Steps (Optional)
- Depending on the application, additional steps such as tempering, stress relieving, or surface treatments may be performed after the initial heat treating process.
- Tempering, for instance, is often used after hardening to reduce brittleness and improve toughness by reheating the material to a lower temperature.
- Stress relieving involves heating the material to a temperature below its transformation range to remove internal stresses caused by machining, welding, or forming.
These four steps form the foundation of the heat treating process, enabling manufacturers to tailor materials to meet specific performance requirements across industries such as aerospace, automotive, and tool manufacturing. Understanding and controlling each step is essential for achieving the desired material properties and ensuring the longevity and reliability of the final product.
Summary Table:
Step | Description | Key Details |
---|---|---|
Heating | Heat material to a precise temperature. | - Temperature varies by material and process (e.g., annealing vs. hardening). |
- Heating methods: electric, gas, or induction furnaces. | ||
- Temperatures can reach up to 2,400°F (1,315°C) for certain alloys. | ||
Holding | Maintain the material at the specified temperature for a set duration. | - Ensures uniform microstructure and complete transformation. |
- Holding time ranges from seconds to days, depending on material thickness and complexity. | ||
Cooling | Cool the material using controlled methods. | - Cooling rate impacts material properties (e.g., quenching for hardening, slow cooling for annealing). |
- Methods include air cooling, oil quenching, water quenching, or furnace cooling. | ||
Additional Steps | Optional steps like tempering or stress relieving. | - Tempering reduces brittleness and improves toughness. |
- Stress relieving removes internal stresses caused by machining or welding. |
Optimize your material properties with expert heat treating solutions—contact us today!