Induction heating is a highly efficient and precise method for heating conductive materials, primarily metals, by generating heat within the material itself through electromagnetic induction. This process is widely used in various industries due to its rapid heating capabilities, localized heating, and minimal contamination risks. When considering induction heating, several critical factors must be evaluated to ensure optimal performance and efficiency. These include the material properties of the part being heated, the depth of heating penetration, operating frequency, applied power, required temperature rise, coil design, coupling efficiency, and the facility's infrastructure. Each of these factors plays a significant role in determining the effectiveness and suitability of induction heating for a specific application.
Key Points Explained:
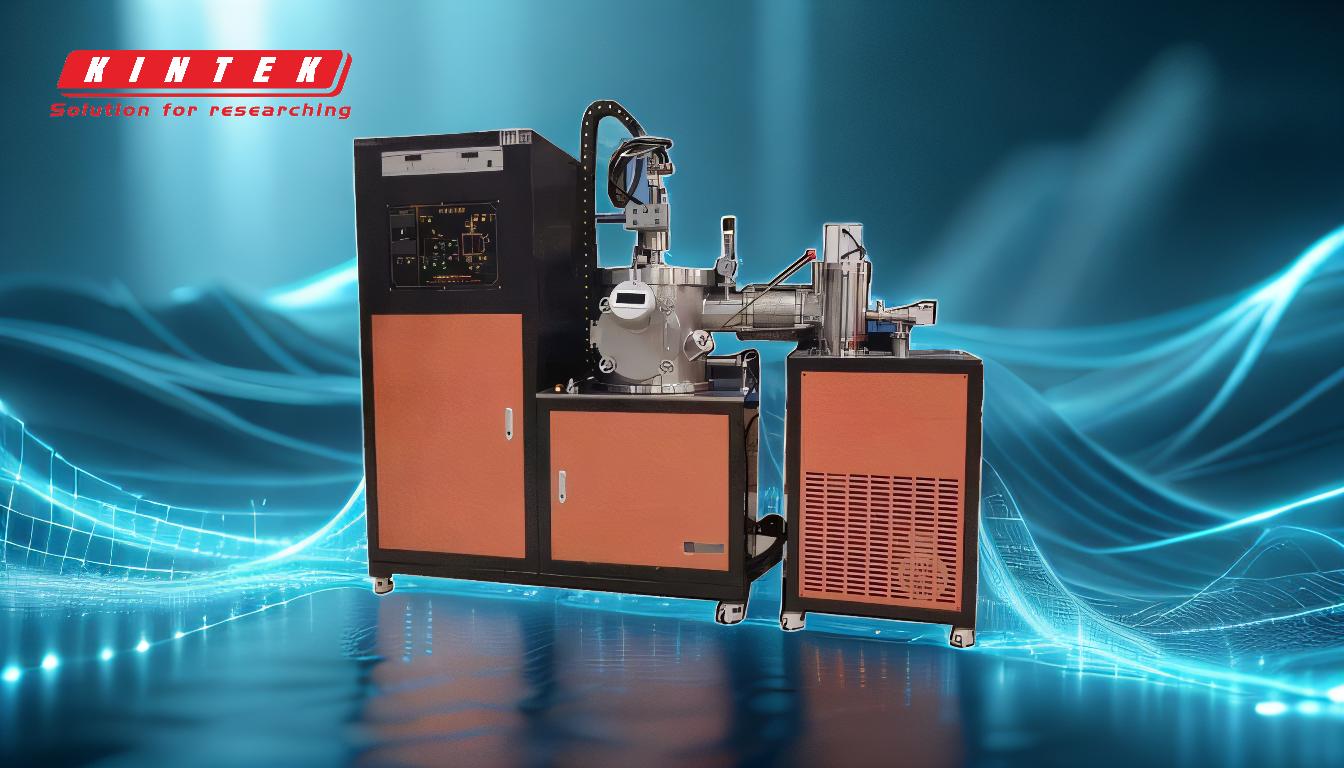
-
Part's Material
- Induction heating is most effective with conductive materials, such as metals. The material's electrical conductivity and magnetic permeability significantly influence the heating process. For example, ferromagnetic materials like iron and steel heat more efficiently due to their higher magnetic permeability. Non-conductive materials, such as plastics or ceramics, cannot be heated using induction.
- The material's thermal properties, such as specific heat capacity and thermal conductivity, also affect the heating rate and uniformity.
-
Depth of Heating Penetration
- The depth to which heat penetrates the material is determined by the operating frequency and the material's properties. Higher frequencies result in shallower heating penetration, making them suitable for surface heating or thin materials. Lower frequencies are used for deeper penetration, ideal for bulk heating of thicker parts.
- This factor is crucial when selecting the appropriate frequency for applications like case hardening or through heating.
-
Operating Frequency
- The frequency of the alternating current used in induction heating directly impacts the heating pattern and efficiency. Common frequencies range from low (1-10 kHz) for deep heating to high (100-500 kHz) for shallow or surface heating.
- The choice of frequency depends on the material, desired heating depth, and application requirements.
-
Applied Power
- The power supplied to the induction heating system determines the rate at which the material heats up. Higher power levels enable faster heating but require careful control to avoid overheating or damaging the material.
- Power requirements depend on factors such as the material's mass, desired temperature rise, and heating time.
-
Rise in Temperature Required
- The target temperature and the rate of temperature increase are critical considerations. Induction heating systems must be capable of achieving the required temperature within the specified time frame.
- Applications like brazing, annealing, or hardening have specific temperature requirements that must be met precisely.
-
Coil Design
- The induction coil, typically made of copper, is a key component that generates the electromagnetic field. The coil's shape, size, and configuration must match the part's geometry to ensure uniform heating.
- Custom coil designs are often necessary for complex or irregularly shaped parts.
-
Coupling Efficiency
- Coupling efficiency refers to how effectively the electromagnetic field transfers energy to the workpiece. Factors such as the gap between the coil and the part, the part's shape, and material properties influence coupling efficiency.
- Proper alignment and proximity between the coil and the workpiece are essential for maximizing energy transfer.
-
Facility and Footprint
- The physical space available for the induction heating system and its integration into existing facilities must be considered. Induction heating systems vary in size, from compact units for small-scale applications to large systems for industrial processes.
- Power supply requirements, cooling systems, and safety considerations also impact the facility's infrastructure.
-
Rapid Heating and Contamination Control
- Induction heating generates heat directly within the material, enabling rapid heating without the need for external contact. This feature is particularly beneficial in applications where contamination must be minimized, such as in the food or pharmaceutical industries.
- The absence of direct contact also reduces wear and tear on heating equipment.
-
System Components
- An induction heating system typically consists of a solid-state RF power supply, an induction coil, and the workpiece. Each component must be carefully selected and integrated to ensure optimal performance.
- The power supply must match the coil and workpiece requirements, while the coil must be designed for efficient energy transfer.
By carefully evaluating these factors, you can select the most suitable induction heating system for your specific application, ensuring efficient, precise, and reliable heating.
Summary Table:
Factor | Description |
---|---|
Part's Material | Conductive metals like iron and steel heat efficiently; non-conductive materials cannot be heated. |
Depth of Heating | Determined by frequency—higher for surface heating, lower for deeper penetration. |
Operating Frequency | Ranges from 1-10 kHz (deep heating) to 100-500 kHz (surface heating). |
Applied Power | Higher power enables faster heating but requires careful control. |
Temperature Rise | Target temperature and heating rate must align with application needs. |
Coil Design | Custom designs ensure uniform heating for complex or irregularly shaped parts. |
Coupling Efficiency | Maximized by proper alignment and proximity between coil and workpiece. |
Facility & Footprint | Space, power supply, and cooling systems must be considered. |
Rapid Heating & Control | Minimizes contamination and reduces wear on equipment. |
System Components | Includes RF power supply, induction coil, and workpiece, all tailored for optimal performance. |
Ready to optimize your induction heating process? Contact us today for expert guidance!