A rotary kiln is a complex piece of equipment used in various industrial processes, such as cement production, lime calcination, and chemical processing. Its main components work together to ensure efficient heat transfer, material processing, and structural stability. The primary parts include the shell, refractory lining, support tyres (riding rings) and rollers, drive gear, and internal heat exchangers. Each component plays a critical role in the kiln's operation, from providing structural integrity to enabling rotation and heat management. Understanding these parts is essential for equipment purchasers to make informed decisions about customization, maintenance, and operational efficiency.
Key Points Explained:
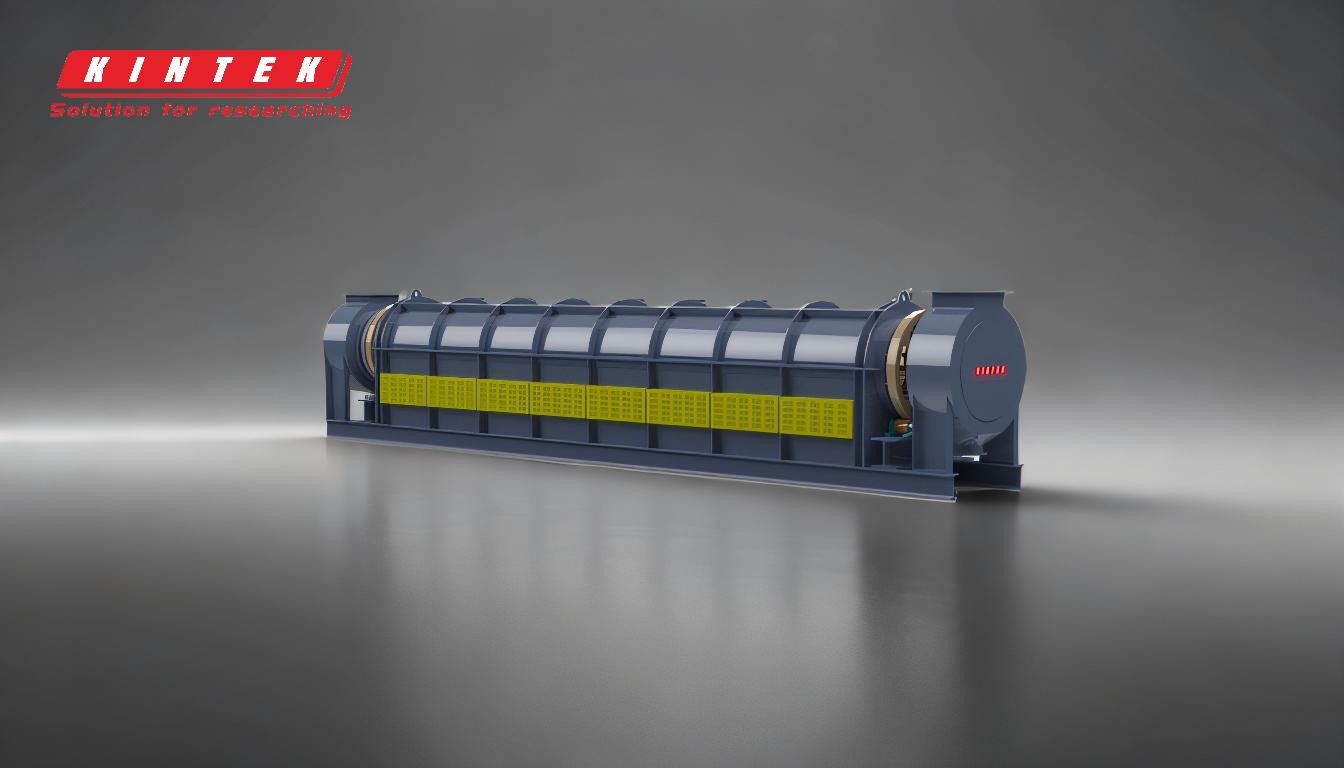
-
Shell:
- The shell is the outermost structure of the rotary kiln, typically made of steel. It is conically tapered at the ends to facilitate material flow and withstands significant mechanical stress, including torsion and flexural forces.
- Importance: The shell provides structural integrity and houses the internal components. Its design and material quality are critical for durability and operational efficiency.
-
Refractory Lining:
- The refractory lining is an insulating layer inside the shell, designed to withstand high temperatures and protect the shell from thermal damage. It is made of heat-resistant materials like firebricks or castables.
- Importance: This lining ensures efficient heat retention, reduces heat loss, and prolongs the life of the shell by preventing overheating and wear.
-
Support Tyres (Riding Rings) and Rollers:
- Support tyres, also known as riding rings, are large steel rings mounted on the shell. They rest on rollers, which support the kiln's weight and allow it to rotate smoothly.
- Importance: These components distribute the kiln's weight evenly and enable controlled rotation, which is essential for uniform material processing and heat distribution.
-
Drive Gear:
- The drive gear is the mechanism responsible for rotating the kiln. It can be a chain and sprocket drive, gear drive, friction drive, or direct drive assembly, depending on the kiln's design and application.
- Importance: The drive gear ensures consistent rotation, which is crucial for maintaining process efficiency and material flow. Its reliability directly impacts the kiln's operational performance.
-
Internal Heat Exchangers:
- Internal heat exchangers are components designed to optimize heat transfer within the kiln. They may include features like lifters or baffles to improve material exposure to heat.
- Importance: These exchangers enhance thermal efficiency, reduce energy consumption, and ensure uniform heating of the material being processed.
-
Additional Components:
- Thrust Rollers: These rollers prevent axial movement of the kiln, ensuring it stays aligned during operation.
- Trunnion Wheels: These support the kiln at the discharge end and help maintain alignment.
- Discharge Breeching: This component directs processed material out of the kiln and into the next stage of the process.
- Product Discharge Area: The area where processed material exits the kiln, often customized based on the specific material and process requirements.
Importance: These additional components ensure smooth operation, alignment, and material handling, contributing to the overall efficiency and longevity of the rotary kiln.
By understanding these key components, equipment purchasers can better evaluate the design, customization options, and maintenance needs of rotary kilns, ensuring optimal performance and cost-effectiveness for their specific applications.
Summary Table:
Component | Function | Importance |
---|---|---|
Shell | Outermost steel structure, tapered for material flow and stress resistance. | Provides structural integrity and durability for efficient operation. |
Refractory Lining | Heat-resistant layer inside the shell to protect from thermal damage. | Ensures heat retention, reduces energy loss, and prolongs shell life. |
**Support Tyres & Rollers | Steel rings and rollers that support and enable smooth rotation. | Distributes weight evenly and ensures uniform material processing and heat distribution. |
Drive Gear | Mechanism for rotating the kiln (e.g., gear drive, friction drive). | Maintains consistent rotation, crucial for process efficiency and material flow. |
**Internal Heat Exchangers | Optimizes heat transfer with features like lifters or baffles. | Enhances thermal efficiency, reduces energy consumption, and ensures uniform material heating. |
Additional Components | Includes thrust rollers, trunnion wheels, discharge breeching, and more. | Ensures alignment, smooth operation, and efficient material handling for longevity and efficiency. |
Ready to optimize your industrial processes with a rotary kiln? Contact our experts today for tailored solutions!