Protective atmospheres in heat treatment are essential for maintaining the integrity and properties of materials during high-temperature processes. These atmospheres prevent oxidation, contamination, and other forms of damage that could compromise the quality of the treated materials. Protective atmospheres can be broadly categorized into active and neutral types, depending on their interaction with the material. They are created using gases such as nitrogen, argon, hydrogen, carbon dioxide, or mixtures of these. Common types of controlled atmospheres include endothermic, exothermic, purified exothermic, drip-type, and ammonia decomposition atmospheres. Each type serves specific purposes, such as preventing oxidation, enhancing surface characteristics, or ensuring dimensional stability. Understanding these atmospheres is critical for achieving desired results in heat treatment processes.
Key Points Explained:
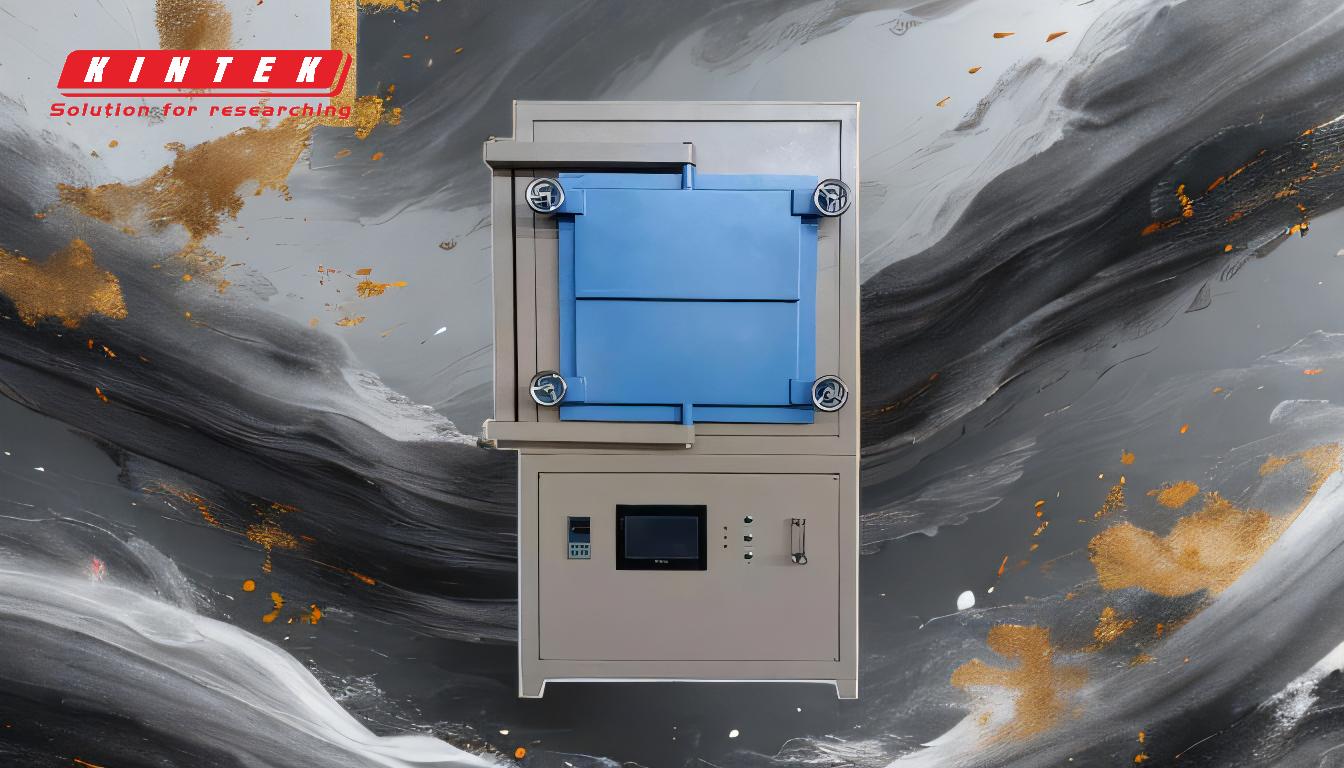
-
Purpose of Protective Atmospheres in Heat Treatment
- Protective atmospheres are used to prevent contamination, oxidation, and other forms of damage during heat treatment processes.
- They ensure that the material retains its properties, such as strength, ductility, and dimensional stability, which are critical for its performance.
- Without proper atmosphere control, materials may become brittle, corroded, or otherwise compromised, leading to poor-quality outcomes.
-
Types of Protective Atmospheres
- Active Atmospheres: These atmospheres chemically interact with the material being treated. For example, they may introduce elements like carbon or nitrogen to enhance surface characteristics such as hardening.
- Neutral Atmospheres: These do not chemically react with the material but provide a protective environment to prevent oxidation or contamination. Examples include nitrogen and argon.
- Inert Atmospheres: These are a subset of neutral atmospheres and are used to prevent oxidation and contamination by reactive gases. They are particularly important in heat-treating applications where maintaining material integrity is critical.
-
Common Gases Used in Protective Atmospheres
- Nitrogen: Widely used as an inert gas to prevent oxidation and contamination.
- Argon: Another inert gas, often used in applications requiring high purity.
- Hydrogen: Used in reducing atmospheres to prevent oxidation and remove oxides from the material's surface.
- Carbon Dioxide: Sometimes used in controlled amounts to achieve specific surface reactions.
- Mixtures of Gases: Custom gas blends are often used to achieve specific outcomes, such as carbon enrichment or decarburization prevention.
-
Types of Controlled Atmospheres
- Endothermic Atmosphere: Produced by reacting a hydrocarbon gas with air in the presence of a catalyst. It is rich in carbon monoxide and hydrogen and is used for processes like carburizing.
- Exothermic Atmosphere: Created by burning a hydrocarbon gas with air. It is less expensive and used for general-purpose heat treatment.
- Purified Exothermic Atmosphere: A refined version of the exothermic atmosphere, with lower levels of reactive gases, used for more sensitive applications.
- Drip-Type Atmosphere: Generated by dripping a liquid hydrocarbon into the furnace, often used for small-scale or specialized heat treatment.
- Ammonia Decomposition Atmosphere: Produced by decomposing ammonia into nitrogen and hydrogen, used for processes like nitriding.
-
Importance of Atmosphere Control
- Controlled atmospheres ensure that heat treatment processes are completed successfully by maintaining specific temperature and gas composition conditions.
- They protect the material from exposure to air at high temperatures, which can lead to oxidation and other forms of damage.
- Proper atmosphere control is critical in commercial heat treatment, where large quantities of materials are processed, and consistency is key.
-
Applications and Benefits
- Surface Hardening: Protective atmospheres can chemically react with the material's surface to enhance characteristics like hardness.
- Oxidation Prevention: Inert and reducing atmospheres prevent oxidation, ensuring the material retains its desired properties.
- Dimensional Stability: By preventing contamination, protective atmospheres help maintain the material's dimensional stability during heat treatment.
-
Challenges and Considerations
- Cost: Some protective atmospheres, such as those using argon or specialized gas mixtures, can be expensive.
- Safety: Gases like hydrogen require careful handling due to their flammability.
- Complexity: Creating and maintaining precise atmospheric conditions can be technically challenging, especially for large-scale operations.
In conclusion, protective atmospheres are a critical component of heat treatment processes, ensuring that materials retain their desired properties and performance characteristics. By understanding the types of atmospheres, the gases used, and their applications, manufacturers can optimize their heat treatment processes for better outcomes.
Summary Table:
Aspect | Details |
---|---|
Purpose | Prevent oxidation, contamination, and damage during heat treatment. |
Types | Active, Neutral, Inert atmospheres. |
Common Gases | Nitrogen, Argon, Hydrogen, Carbon Dioxide, Gas Mixtures. |
Controlled Atmospheres | Endothermic, Exothermic, Purified Exothermic, Drip-Type, Ammonia Decomposition. |
Applications | Surface hardening, oxidation prevention, dimensional stability. |
Challenges | Cost, safety (flammable gases), technical complexity. |
Optimize your heat treatment process with the right protective atmosphere—contact our experts today!