Annealing is a critical heat treatment process used to alter the physical and sometimes chemical properties of a material, primarily metals, to increase ductility, reduce hardness, and improve machinability. The process involves heating the material to a specific temperature, holding it at that temperature to allow changes in the microstructure, and then cooling it at a controlled rate. Various types of annealing processes exist, each tailored to achieve specific outcomes based on the material and desired properties. Standards for annealing are crucial to ensure consistency, quality, and performance of the treated materials.
Key Points Explained:
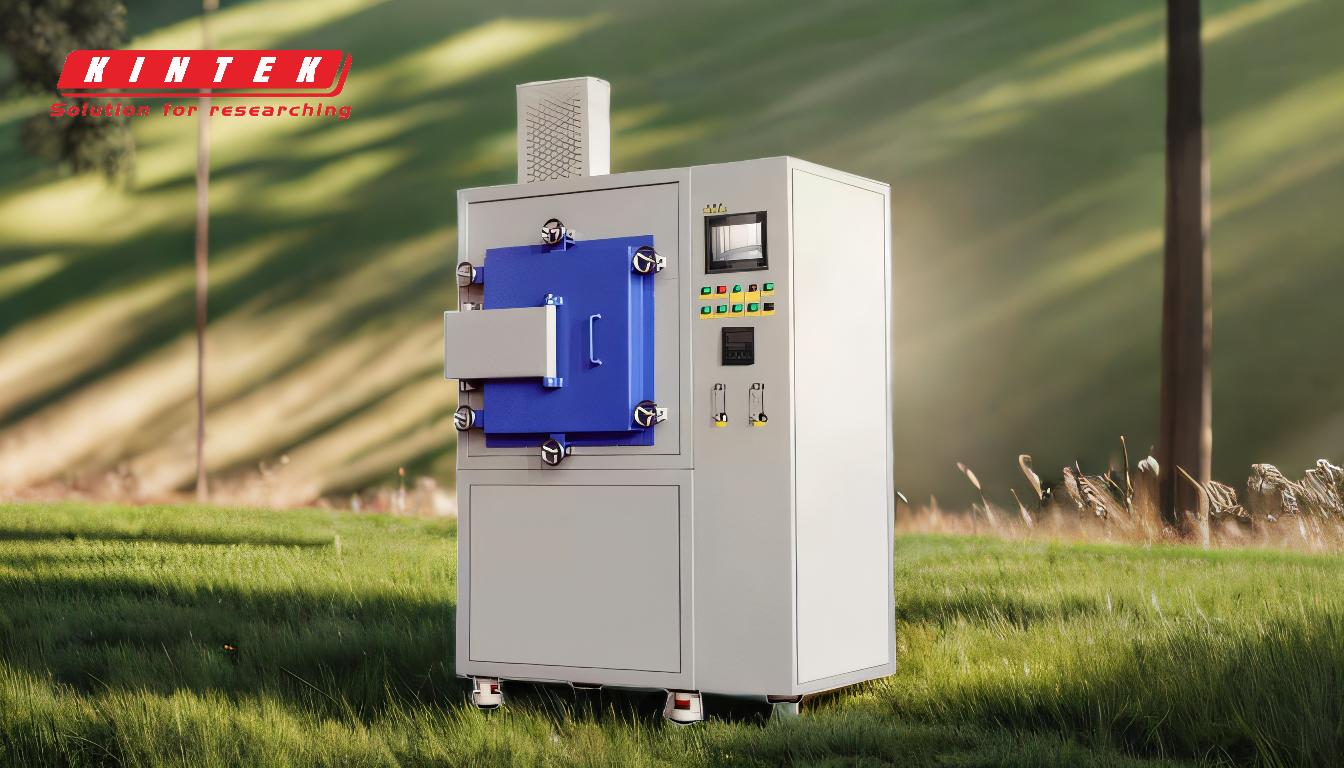
-
Definition and Purpose of Annealing:
- Annealing is a heat treatment process that involves heating a material to a specific temperature, holding it at that temperature, and then cooling it at a controlled rate.
- The primary purposes of annealing are to soften materials, improve machinability, facilitate cold working, enhance mechanical or electrical properties, and increase dimensional stability.
-
Types of Annealing Processes:
- Black Annealing: Typically used for steel, this process involves heating the metal in an open flame or furnace, resulting in a black oxide surface.
- Blue Annealing: Similar to black annealing but performed at a lower temperature, resulting in a blue oxide finish.
- Box Annealing: The metal is placed in a sealed container to protect it from oxidation during heating and cooling.
- Bright Annealing: Conducted in a controlled atmosphere or vacuum to prevent oxidation, resulting in a bright, clean surface.
- Cycle Annealing: Involves repeated heating and cooling cycles to achieve specific material properties.
- Flame Annealing: Uses a direct flame to heat the metal, often used for localized annealing.
- Full Annealing: The metal is heated above its upper critical temperature and then slowly cooled to refine the grain structure.
- Graphitizing: Used for cast iron to convert carbon into graphite, improving machinability.
- Intermediate Annealing: Performed between cold working stages to restore ductility.
- Isothermal Annealing: The metal is held at a constant temperature for a specific period to achieve uniform properties.
- Process Annealing: A lower temperature process used to relieve stresses without significantly altering the microstructure.
- Quench Annealing: Involves rapid cooling after heating to achieve specific properties.
- Spheroidizing: A process to produce a spherical or globular form of carbide in steel to improve machinability.
-
Temperature and Holding Time:
- The temperature and duration of the annealing process are critical and vary depending on the material and desired outcome.
- For example, full annealing typically involves heating the material to a temperature above its upper critical temperature and holding it there until the microstructure changes, followed by slow cooling.
-
Cooling Rate:
- The cooling rate is a crucial factor in annealing. Slow cooling rates are generally used to allow the formation of a more ductile and soft microstructure.
- Rapid cooling, as in quench annealing, can be used to achieve specific properties but may also introduce stresses that need to be managed.
-
Standards and Guidelines:
- Various international standards govern the annealing process to ensure consistency and quality. These standards specify the temperature ranges, holding times, cooling rates, and atmosphere conditions for different materials.
- Examples include ASTM (American Society for Testing and Materials) and ISO (International Organization for Standardization) standards, which provide detailed guidelines for annealing processes.
-
Applications:
- Annealing is widely used in industries such as automotive, aerospace, construction, and manufacturing to improve the properties of metals and alloys.
- It is also used in the production of electronic components, where precise control of material properties is essential.
-
Quality Control:
- Quality control measures, such as metallographic analysis and hardness testing, are often employed to verify that the annealing process has achieved the desired material properties.
- Non-destructive testing methods, such as ultrasonic testing, may also be used to ensure the integrity of the annealed material.
In summary, annealing is a versatile and essential heat treatment process with various methods tailored to specific materials and desired outcomes. Standards and guidelines ensure the process is carried out consistently and effectively, resulting in materials with improved properties for a wide range of applications.
Summary Table:
Aspect | Details |
---|---|
Purpose | Soften materials, improve machinability, enhance mechanical properties |
Types | Black, Blue, Box, Bright, Full, Spheroidizing, and more |
Key Factors | Temperature, holding time, cooling rate, and controlled atmosphere |
Standards | ASTM, ISO, and other international guidelines |
Applications | Automotive, aerospace, construction, electronics, and manufacturing |
Quality Control | Metallographic analysis, hardness testing, and non-destructive testing |
Optimize your material properties with expert annealing solutions—contact us today!