Spark plasma sintering (SPS) is a modern sintering technique that combines uniaxial pressure and pulsed direct current (DC) to rapidly consolidate powders into dense, homogeneous materials. The process is characterized by its speed, efficiency, and ability to achieve high densification at lower temperatures compared to conventional sintering methods. The main stages of SPS include gas removal and vacuum creation, application of pressure, resistance heating, and cooling. Each stage plays a critical role in ensuring the successful densification and bonding of powder particles. The process leverages plasma discharge, joule heating, and plastic deformation to achieve rapid heating, particle bonding, and material consolidation.
Key Points Explained:
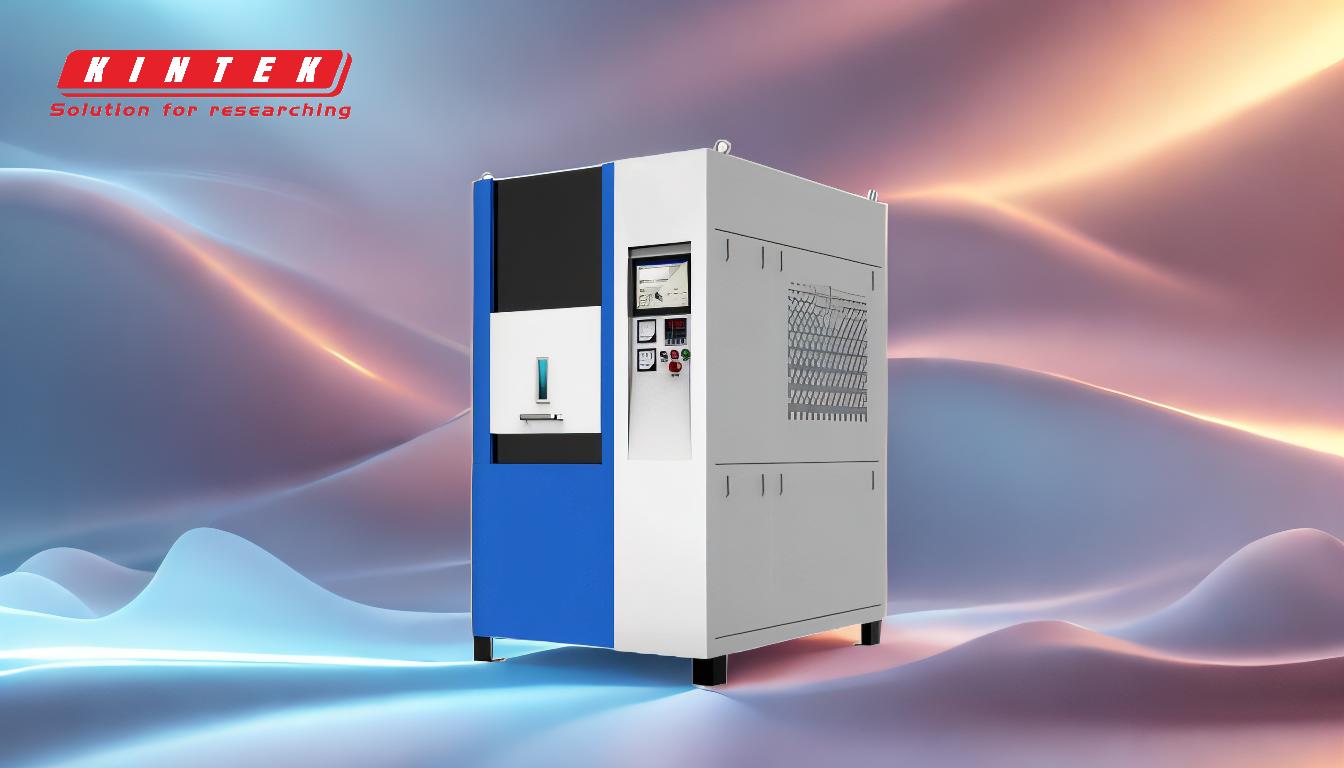
-
Gas Removal and Vacuum Creation
- The first step in SPS involves removing gases from the sintering chamber and creating a vacuum or controlled atmosphere.
- This is crucial to prevent oxidation and contamination of the powder material, ensuring the purity and quality of the final product.
- A vacuum environment also facilitates better heat transfer and plasma generation during the subsequent stages.
-
Application of Pressure
- Uniaxial pressure is applied to the powder material within a die, typically made of graphite.
- The pressure helps to compact the powder particles, reducing gaps between them and promoting better contact for sintering.
- The applied pressure also aids in the plastic deformation of particles, which is essential for achieving high densification.
-
Resistance Heating
- Pulsed DC current is passed through the graphite die and, if conductive, through the powder material itself.
- This generates localized high temperatures and plasma discharge between particles, causing rapid heating.
- The process involves three heating mechanisms:
- Plasma Heating: Discharge between particles creates plasma, which facilitates surface diffusion and bonding.
- Joule Heating: Electrical resistance within the material generates heat, further aiding in sintering.
- Plastic Deformation: The combination of heat and pressure causes particles to deform and bond at their interfaces.
- These mechanisms enable sintering at much lower temperatures and shorter times compared to conventional methods.
-
Cooling Stage
- After the sintering process, the material is rapidly cooled to room temperature.
- Rapid cooling helps to preserve the microstructure and properties of the sintered material.
- The cooling rate is controlled to prevent thermal stresses or cracks in the final product.
-
Advantages of SPS
- Speed: SPS completes the sintering process in a fraction of the time required by conventional methods.
- Lower Temperatures: SPS achieves densification at temperatures several hundred degrees lower than traditional sintering.
- Improved Material Properties: The rapid heating and cooling rates result in finer microstructures and enhanced mechanical properties.
- Versatility: SPS can be used for a wide range of materials, including ceramics, metals, and composites.
-
Applications of SPS
- SPS is widely used in the fabrication of advanced materials, such as nanostructured ceramics, functionally graded materials, and composites.
- It is particularly valuable in industries requiring high-performance materials with precise control over microstructure and properties, such as aerospace, automotive, and electronics.
By following these steps, spark plasma sintering enables the production of high-quality, dense materials with superior properties, making it a preferred choice for advanced material fabrication.
Summary Table:
Stage | Key Details |
---|---|
Gas Removal & Vacuum | Removes gases, prevents oxidation, and ensures a controlled atmosphere. |
Application of Pressure | Compacts powder particles, reduces gaps, and aids in plastic deformation. |
Resistance Heating | Uses pulsed DC for plasma discharge, joule heating, and rapid particle bonding. |
Cooling Stage | Rapid cooling preserves microstructure and prevents thermal stresses. |
Advantages | Speed, lower temperatures, improved properties, and material versatility. |
Applications | Aerospace, automotive, electronics, and advanced material fabrication. |
Learn how Spark Plasma Sintering can revolutionize your material fabrication process—contact us today!