The two primary methods of hardening metals are quenching and tempering. Quenching involves rapidly cooling the metal after heating it to a high temperature, which increases its hardness but can make it brittle. Tempering, on the other hand, involves reheating the quenched metal to a lower temperature to reduce brittleness while maintaining hardness. Both methods are essential in achieving the desired balance of hardness, strength, and durability in metal components. Below, we explore these methods in detail, their processes, and their applications.
Key Points Explained:
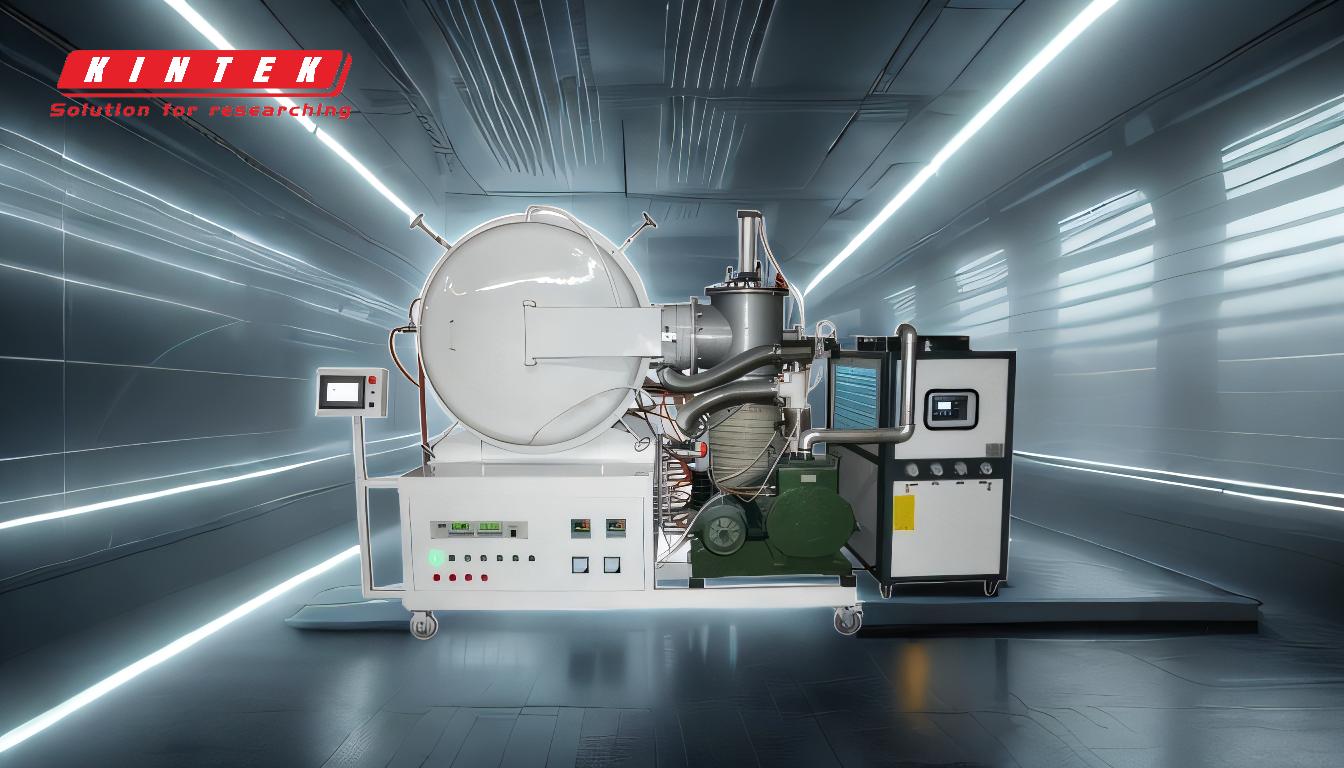
-
Quenching: Rapid Cooling for Hardness
- Process: Quenching involves heating the metal to a high temperature (above its critical temperature) and then rapidly cooling it by immersing it in a quenching medium such as water, oil, or air. This rapid cooling locks the metal's microstructure into a hardened state.
- Purpose: The primary goal of quenching is to increase the hardness and strength of the metal by creating a martensitic structure, which is a very hard and brittle crystalline form.
- Applications: Quenching is commonly used in the production of tools, blades, and mechanical components that require high wear resistance and hardness.
-
Tempering: Reducing Brittleness While Maintaining Hardness
- Process: After quenching, the metal is often too brittle for practical use. Tempering involves reheating the metal to a temperature below its critical point (typically between 150°C and 650°C) and then allowing it to cool slowly. This process reduces internal stresses and brittleness while retaining much of the hardness achieved during quenching.
- Purpose: Tempering balances hardness with toughness, making the metal more durable and less prone to cracking or breaking under stress.
- Applications: Tempering is widely used in the manufacturing of springs, gears, and structural components that need to withstand repeated stress without failing.
-
Comparison of Quenching and Tempering
- Quenching focuses on maximizing hardness but often results in brittleness, while tempering sacrifices a small amount of hardness to improve toughness and durability.
- Together, these methods form a two-step process that is essential for creating high-performance metal parts.
-
Factors Influencing the Hardening Process
- Material Composition: The type of metal or alloy being hardened affects the choice of quenching medium and tempering temperature.
- Cooling Rate: Faster cooling rates (e.g., water quenching) result in greater hardness but also increase the risk of cracking.
- Tempering Temperature: Higher tempering temperatures reduce hardness more significantly but improve toughness and ductility.
-
Practical Considerations for Equipment and Consumables Purchasers
- Quenching Media: The choice of quenching medium (water, oil, or air) depends on the metal type and desired hardness. Oil quenching is often preferred for high-carbon steels to minimize cracking.
- Furnace Requirements: Both quenching and tempering require precise temperature control, making equipment like muffle furnaces essential for consistent results.
- Safety and Maintenance: Proper handling of quenching media and regular maintenance of furnaces are critical to ensure safety and longevity of equipment.
By understanding these two methods of hardening, purchasers can make informed decisions about the equipment and consumables needed to achieve the desired properties in metal components. Whether producing tools, machinery parts, or structural elements, the combination of quenching and tempering ensures optimal performance and durability.
Summary Table:
Method | Process | Purpose | Applications |
---|---|---|---|
Quenching | Rapidly cool heated metal in water, oil, or air to lock in hardness. | Increases hardness and strength, but may cause brittleness. | Tools, blades, mechanical components requiring high wear resistance. |
Tempering | Reheat quenched metal to a lower temperature and cool slowly. | Reduces brittleness while maintaining hardness, improving toughness. | Springs, gears, structural components needing durability under stress. |
Comparison | Quenching maximizes hardness; tempering balances hardness with toughness. | Together, they create high-performance metal parts with optimal properties. | Essential for tools, machinery parts, and structural elements. |
Need expert advice on hardening metals? Contact us today to find the right equipment for your needs!