Chemical Vapor Deposition (CVD) is a versatile and widely used process in various industries, particularly for creating high-quality coatings and fabricating semiconductor devices. It is valued for its ability to produce films with exceptional purity and uniformity, making it suitable for applications ranging from protective coatings to advanced electronics. However, the process comes with challenges, such as the requirement for high temperatures and the use of hazardous chemicals, which necessitate strict safety protocols. Below, we explore the key uses of CVD in detail.
Key Points Explained:
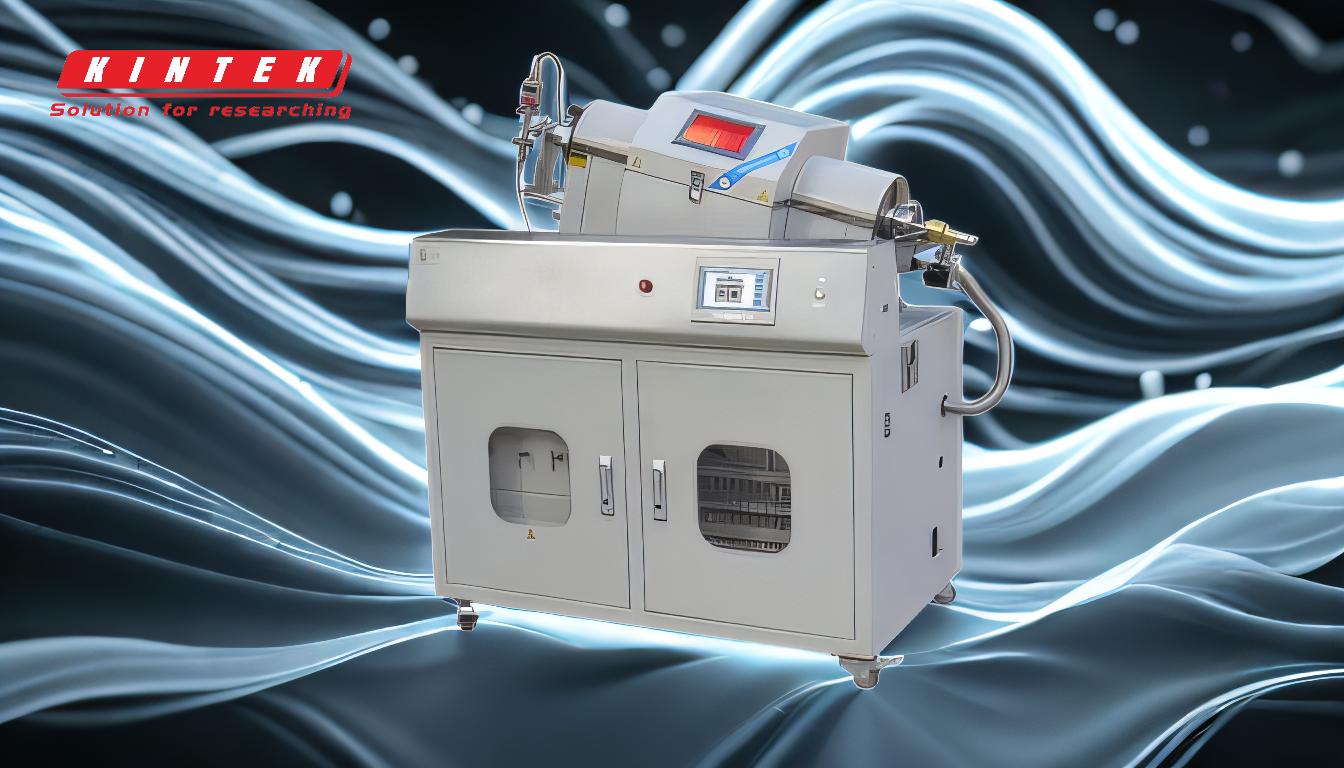
-
Production of Coatings
- CVD is extensively used to create protective and functional coatings on various materials. These coatings can enhance properties such as wear resistance, corrosion resistance, and thermal stability.
- For example, CVD is employed to deposit diamond-like carbon (DLC) coatings on cutting tools, improving their durability and performance.
- It is also used to apply coatings on components in aerospace and automotive industries, where materials must withstand extreme conditions.
-
Fabrication of Semiconductor Devices
- CVD plays a critical role in the semiconductor industry, where it is used to deposit thin films of materials such as silicon dioxide, silicon nitride, and polysilicon.
- These films are essential for creating insulation layers, conductive pathways, and other components in integrated circuits.
- Specific applications include shallow trench isolation (STI), pre-metal dielectric (PMD), inter-metal dielectric (IMD), conformal liners, and conductor gap fill in electrical circuits.
-
Creation of Insulation and Conductive Layers
- In transistor structures, CVD is used to form insulation materials that prevent electrical interference between components.
- It is also employed to deposit conductive metal layers, such as tungsten or copper, which serve as interconnects in microelectronic devices.
- These processes are crucial for the miniaturization and performance enhancement of modern electronics.
-
High Purity and Uniformity of Films
- One of the standout advantages of CVD is its ability to produce films with exceptional purity and uniformity. This is particularly important in industries like semiconductors, where even minor impurities can affect device performance.
- The process allows for precise control over film thickness and composition, ensuring consistent quality across large-scale production.
-
Challenges and Safety Considerations
- Despite its advantages, CVD requires extremely high temperatures, which can limit its use with temperature-sensitive substrates.
- The process often involves toxic or hazardous chemicals, necessitating robust safety measures for handling and disposal.
- Companies must implement strict protocols to protect workers and minimize environmental impact, ensuring compliance with safety regulations.
In summary, CVD is a cornerstone technology in modern manufacturing, enabling the production of high-performance coatings and advanced semiconductor devices. Its ability to deliver pure, uniform films makes it indispensable in industries ranging from electronics to aerospace. However, the challenges associated with high temperatures and hazardous materials highlight the importance of careful process management and safety practices.
Summary Table:
Application | Description |
---|---|
Production of Coatings | Enhances wear resistance, corrosion resistance, and thermal stability. |
Semiconductor Fabrication | Deposits thin films for insulation, conductive pathways, and device components. |
Insulation & Conductive Layers | Forms insulation materials and deposits conductive metals in microelectronics. |
High Purity & Uniformity | Produces films with exceptional purity and uniformity for consistent quality. |
Challenges & Safety | Requires high temperatures and hazardous chemicals, necessitating strict safety protocols. |
Interested in how CVD can benefit your industry? Contact our experts today to learn more!