An induction furnace operates on the principles of electromagnetic induction and the Joule effect to heat and melt conductive materials. It uses a hollow copper coil through which alternating current flows, generating a powerful electromagnetic field. When a conductive metal charge is placed within this field, eddy currents are induced within the metal, generating heat internally. This process ensures efficient, uniform, and non-contact heating. The furnace's design allows for precise temperature control and rapid melting, making it ideal for applications like metal melting and alloy production. The heat is generated directly within the metal charge, not the furnace itself, ensuring energy efficiency and minimal heat loss.
Key Points Explained:
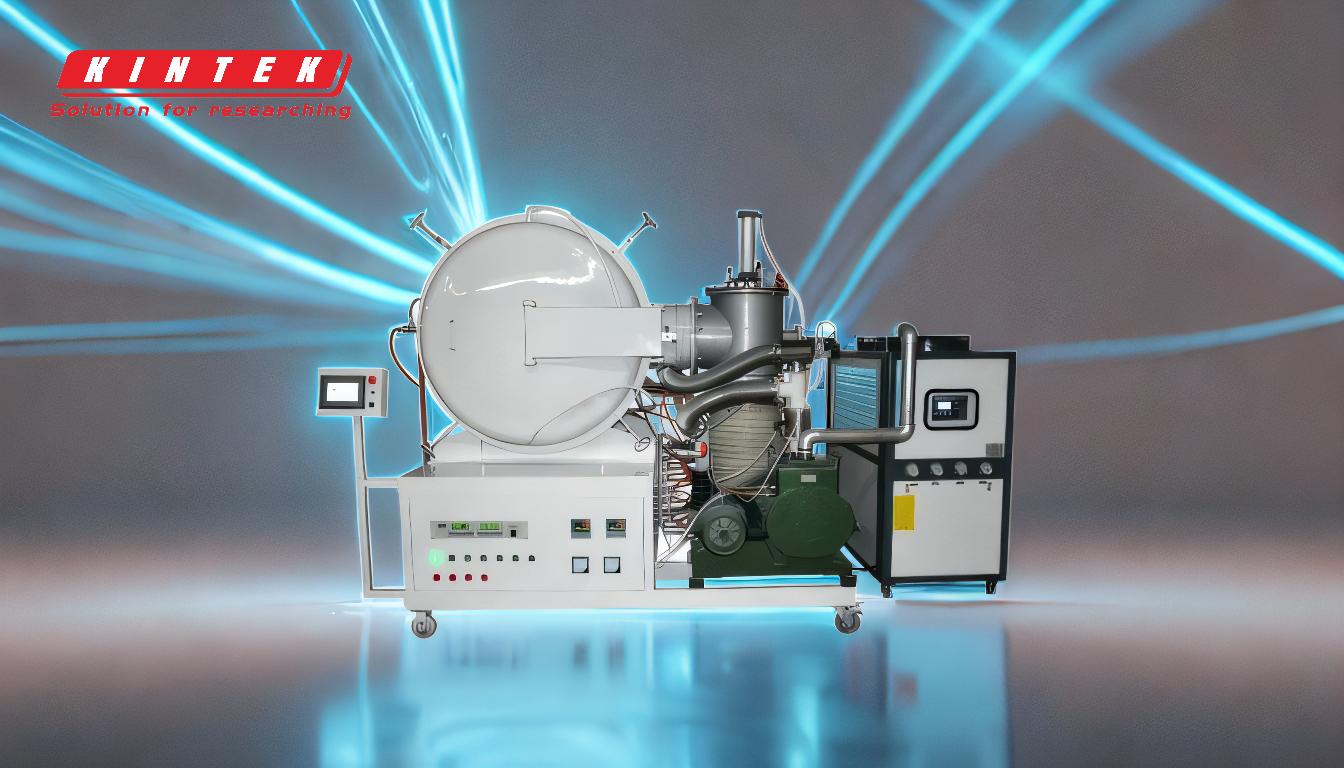
-
Electromagnetic Induction and Eddy Currents:
- The core principle of an induction furnace is electromagnetic induction. An alternating current (AC) is passed through a hollow copper coil, creating a powerful electromagnetic field.
- When a conductive metal charge is placed within this field, the changing magnetic field induces eddy currents within the metal.
- These eddy currents circulate within the metal, generating heat due to the metal's electrical resistance (Joule effect).
-
Non-Contact Heating:
- Induction heating is a non-contact process, meaning the heat is generated directly within the metal charge rather than through external heating elements.
- This ensures uniform heating and minimizes contamination, making it ideal for applications requiring precise temperature control and clean melting environments.
-
Transformer Principles:
- The furnace operates on principles similar to a transformer. The copper coil acts as the primary winding, and the metal charge acts as the secondary winding.
- The alternating current in the primary coil induces a current in the metal charge, which heats up due to its electrical resistance.
-
Frequency and Efficiency:
- The frequency of the alternating current plays a crucial role in the efficiency of the furnace. Higher frequencies (e.g., 150 Hz to 8000 Hz) are used to ensure deeper penetration of eddy currents and faster heating.
- High-frequency currents are generated using a silicon-controlled variable frequency power supply, which converts three-phase AC into medium-frequency AC.
-
Cooling and Heat Management:
- The primary coil is cooled by circulating water to prevent overheating and ensure consistent performance.
- Heat is generated directly within the metal charge, minimizing heat loss to the furnace structure and improving energy efficiency.
-
Applications and Advantages:
- Induction furnaces are widely used in metal melting, alloy production, and heat treatment due to their ability to achieve precise temperature control and uniform heating.
- They offer advantages such as rapid heating, energy efficiency, and the ability to work with a wide range of conductive materials.
-
Design and Operation:
- The furnace consists of a coil, a power supply, and a container or chamber for the metal charge.
- The alternating magnetic field generated by the coil cuts through the metal charge, inducing eddy currents and generating heat internally.
- The design ensures that the heat is concentrated within the metal, allowing for efficient melting and minimal energy waste.
In summary, an induction furnace leverages electromagnetic induction and the Joule effect to generate heat directly within a conductive metal charge. Its non-contact heating, precise temperature control, and energy efficiency make it a preferred choice for industrial metal melting and alloy production.
Summary Table:
Key Feature | Description |
---|---|
Principle | Electromagnetic induction and Joule effect generate heat within the metal charge. |
Heating Method | Non-contact heating ensures uniform heating and minimal contamination. |
Temperature Control | Precise control for applications like metal melting and alloy production. |
Energy Efficiency | Heat is generated directly in the metal, minimizing energy loss. |
Applications | Metal melting, alloy production, and heat treatment. |
Frequency | Higher frequencies (150 Hz to 8000 Hz) ensure deeper eddy current penetration. |
Discover how an induction furnace can optimize your metal melting process—contact us today!