A furnace liner plays a crucial role in ensuring the efficient and safe operation of furnaces, particularly in high-temperature and high-frequency environments. It acts as a protective barrier, directing gases, reducing decay and deterioration, and enhancing the overall performance of the furnace. In applications like aluminum melting induction furnaces, the liner is specifically designed to withstand extreme conditions, such as high vibration frequencies and the strong penetrability of molten aluminum. A well-designed liner can significantly extend the lifespan of the furnace, often lasting for hundreds of melting cycles.
Key Points Explained:
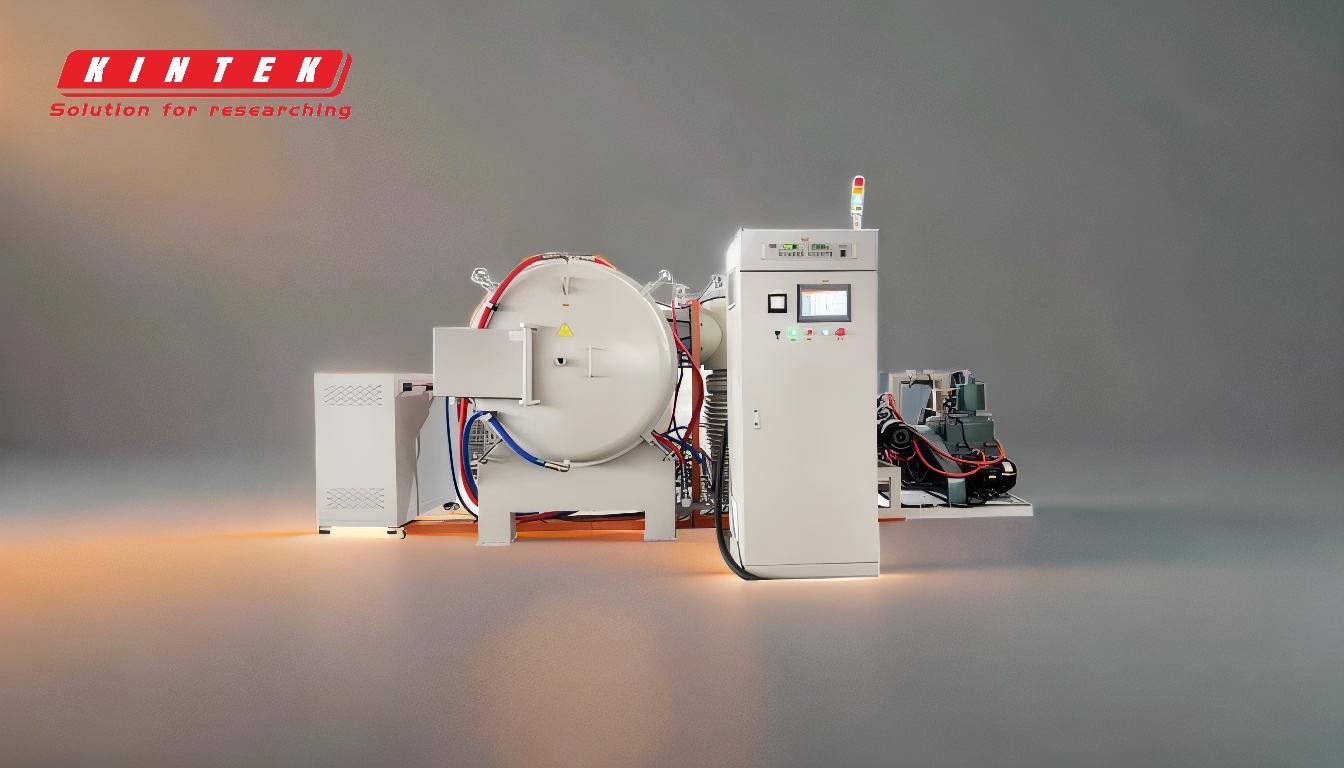
-
Directs Gases and Improves Efficiency
- The furnace liner helps channel gases, such as combustion byproducts, up and out of the flue.
- This ensures that the furnace operates more efficiently by maintaining proper airflow and reducing the risk of gas buildup.
- Improved gas flow also minimizes the risk of corrosion and decay, prolonging the furnace's lifespan.
-
Protects the Furnace Structure
- The liner acts as a protective barrier between the high-temperature environment inside the furnace and the furnace's structural components.
- It prevents direct exposure to heat, reducing wear and tear on the furnace walls and other parts.
- This protection is especially critical in environments with high-frequency vibrations or corrosive materials, such as molten aluminum.
-
Enhances Performance in Specialized Applications
- In aluminum melting induction furnaces, the liner must be specifically designed to handle unique challenges, such as the strong penetrability of molten aluminum and high vibration frequencies.
- Specialized liners are engineered to withstand these conditions, ensuring consistent performance and reducing the risk of failure.
- A high-quality liner can typically be used for more than 300 melting cycles, making it a cost-effective solution for industrial applications.
-
Reduces Maintenance and Operational Costs
- By preventing decay and deterioration, the liner reduces the need for frequent repairs or replacements.
- This not only lowers maintenance costs but also minimizes downtime, ensuring continuous operation and productivity.
- The liner's ability to withstand extreme conditions further contributes to long-term savings.
-
Ensures Safety and Reliability
- A well-functioning liner maintains the structural integrity of the furnace, reducing the risk of leaks, cracks, or other failures that could lead to hazardous situations.
- In applications involving molten metals, the liner's durability is critical to preventing spills or accidents.
- This reliability is essential for maintaining a safe working environment and protecting both equipment and personnel.
In summary, a furnace liner is a vital component that enhances the efficiency, durability, and safety of furnaces. Its role in directing gases, protecting the furnace structure, and withstanding extreme conditions makes it indispensable, particularly in specialized applications like aluminum melting induction furnaces. By investing in a high-quality liner, users can optimize furnace performance, reduce maintenance costs, and ensure long-term reliability.
Summary Table:
Key Role | Benefits |
---|---|
Directs Gases | Improves airflow, reduces gas buildup, and minimizes corrosion risks. |
Protects Furnace Structure | Shields components from heat, vibrations, and corrosive materials. |
Enhances Specialized Performance | Designed for extreme conditions like molten aluminum and high vibrations. |
Reduces Maintenance Costs | Extends lifespan, lowers repair needs, and minimizes downtime. |
Ensures Safety and Reliability | Prevents leaks, cracks, and accidents, ensuring a safe working environment. |
Optimize your furnace's performance with a high-quality liner—contact us today to learn more!