Debinding is a critical step in manufacturing processes such as powder metallurgy and technical ceramics, where it removes binding agents or organic materials from a component before sintering. These binders, initially necessary for shaping and compacting the material, become detrimental if left in the final product. Debinding ensures the component is free of impurities that could cause defects like warping, cracking, or contamination during sintering. The process involves precise control of temperature, pressure, and atmosphere to avoid damaging the material. By removing binders, debinding prepares the component for sintering, resulting in a stronger, more durable final product and preventing issues like furnace clogging or surface contamination.
Key Points Explained:
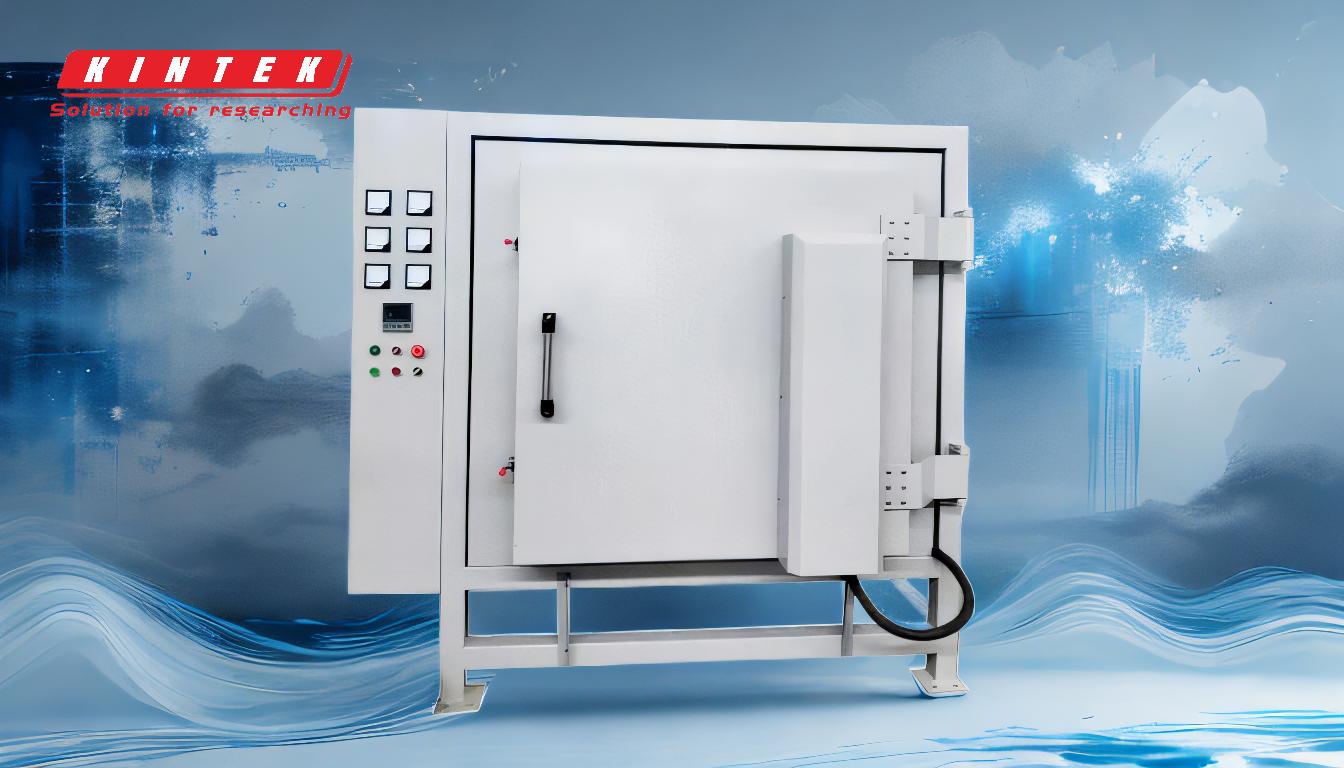
-
Purpose of Debinding:
- Debinding removes binding agents or organic materials used during the shaping and compaction of components.
- These binders are necessary initially but become undesirable during sintering, as they can interfere with the final product's integrity.
-
Importance in Manufacturing:
- Ensures the component is free of impurities that could lead to defects such as warping, cracking, or blistering.
- Prevents contamination of the sintering furnace, which could affect both the furnace and the final product.
-
Process Details:
- Debinding typically starts at room temperature and finishes at around 600°C.
- Requires careful control of temperature profiles, pressure, gas atmosphere, and annealing time to avoid damaging the material.
-
Impact on Final Product:
- Removes binders that could otherwise create pores or weak spots in the final product.
- Prepares the component for sintering, ensuring a stronger, more durable outcome.
-
Efficiency and Practical Benefits:
- Prevents furnace clogging, which can slow down the manufacturing process.
- Makes the overall process faster and more efficient compared to sintering without debinding.
-
Applications:
- Commonly used in powder metallurgy and technical ceramics manufacturing.
- Essential for producing high-quality, defect-free components in industries requiring precision and durability.
By understanding these key points, manufacturers can optimize the debinding process to achieve better results in their production workflows.
Summary Table:
Aspect | Details |
---|---|
Purpose | Removes binding agents or organic materials to ensure material integrity. |
Importance | Prevents defects like warping, cracking, and furnace contamination. |
Process | Controlled temperature (up to 600°C), pressure, and gas atmosphere. |
Impact | Prepares components for sintering, resulting in stronger, durable products. |
Efficiency | Prevents furnace clogging and speeds up the manufacturing process. |
Applications | Powder metallurgy, technical ceramics, and precision manufacturing. |
Optimize your debinding process for better results—contact our experts today!