The deposition rate, which measures how fast a film is grown, is influenced by several factors, including the size of the erosion zone, target-substrate distance, power, temperature, plasma characteristics, and the physical properties of the target material. These factors interact in complex ways to determine the rate at which material is deposited onto a substrate. For example, increasing power or decreasing the target-substrate distance can enhance the deposition rate, while the size of the erosion zone and plasma characteristics also play significant roles. Understanding these factors is crucial for selecting the right deposition technology and ensuring optimal film properties like uniformity, stress, and density.
Key Points Explained:
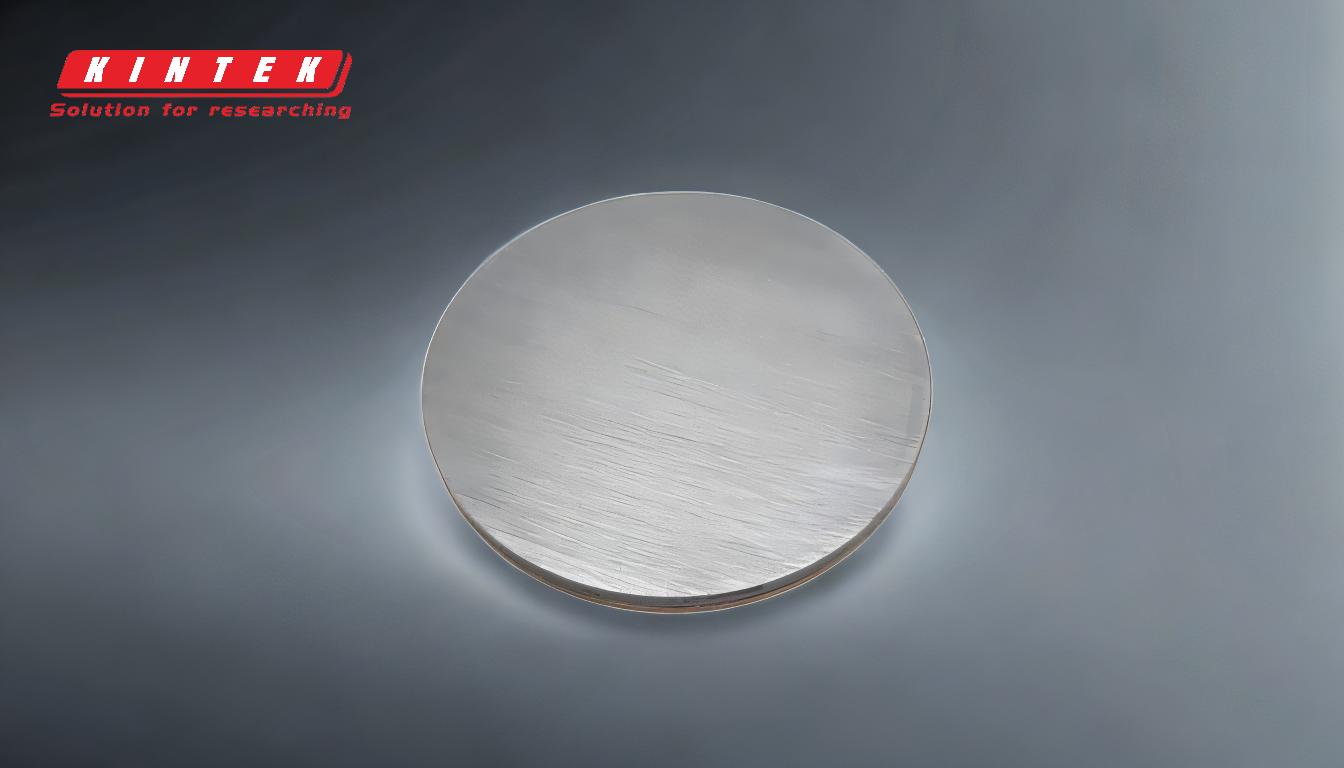
-
Erosion Zone Size and Target-Substrate Distance:
- The size of the erosion zone directly impacts the deposition rate. A larger erosion zone generally leads to a higher deposition rate.
- Thickness uniformity decreases as the target-substrate distance increases. Conversely, decreasing this distance can enhance the deposition rate.
- These factors are interrelated; optimizing the target-substrate distance and erosion zone size is essential for achieving desired deposition rates and film uniformity.
-
Power and Temperature:
- Increasing the power supplied to the deposition process can significantly increase the deposition rate. Higher power levels provide more energy to the system, facilitating faster material deposition.
- Temperature also plays a critical role. Elevated temperatures can enhance the mobility of atoms or molecules, leading to faster deposition rates. However, excessive temperatures may adversely affect film properties.
-
Plasma Characteristics:
- The plasma used in deposition processes (e.g., sputtering) has characteristics such as temperature, composition, and density that influence the deposition rate.
- Monitoring the elemental composition within the plasma chamber is crucial to ensure the correct material composition and to detect any contamination that could affect the deposition rate and film quality.
-
Physical Properties of the Target Material:
- The deposition rate in processes like sputtering is influenced by the physical properties of the target material, including its atomic mass, binding energy, and sputtering yield.
- Materials with higher sputtering yields will generally have higher deposition rates under the same conditions.
-
Deposition Rate Ranges and Application Suitability:
- Deposition rates can vary widely, from a few tens of Å/min to 10,000 Å/min, depending on the technology and conditions used.
- Selecting a deposition technology with a rate suitable for the specific application is crucial. Faster rates may compromise film properties like uniformity, stress, or density, while slower rates may be impractical for high-throughput applications.
-
Monitoring and Control:
- Continuous monitoring of process parameters such as plasma composition, temperature, and target-substrate distance is essential for maintaining consistent deposition rates.
- Advanced control systems can adjust these parameters in real-time to optimize the deposition rate and ensure high-quality film production.
By carefully considering and controlling these factors, it is possible to achieve the desired deposition rate while maintaining the quality and properties of the deposited film. This understanding is vital for equipment and consumable purchasers to select the appropriate deposition technology and optimize process parameters for their specific applications.
Summary Table:
Factor | Impact on Deposition Rate |
---|---|
Erosion Zone Size | Larger zones increase deposition rate but may affect uniformity. |
Target-Substrate Distance | Decreasing distance enhances deposition rate and improves uniformity. |
Power | Higher power levels significantly increase deposition rate. |
Temperature | Elevated temperatures enhance deposition rate but may affect film properties. |
Plasma Characteristics | Plasma temperature, composition, and density influence deposition rate and film quality. |
Target Material Properties | Higher sputtering yields lead to faster deposition rates. |
Deposition Rate Ranges | Rates vary from tens of Å/min to 10,000 Å/min, depending on technology and conditions. |
Need help optimizing your deposition process? Contact our experts today for tailored solutions!