Sintering is a critical thermal process used to transform powdered materials into solid, cohesive structures without melting the primary material. It involves three main stages: shaping the powder into a "green" part, heating it to remove binders and fuse particles, and cooling to achieve the final product. The process occurs in specialized equipment like a sintering furnace, where temperature control is crucial to ensure particle bonding through diffusion. Sintering enhances material properties, reduces porosity, and achieves the desired mechanical strength and dimensional accuracy. The process is widely used in industries like metallurgy, ceramics, and manufacturing to produce complex, high-performance components.
Key Points Explained:
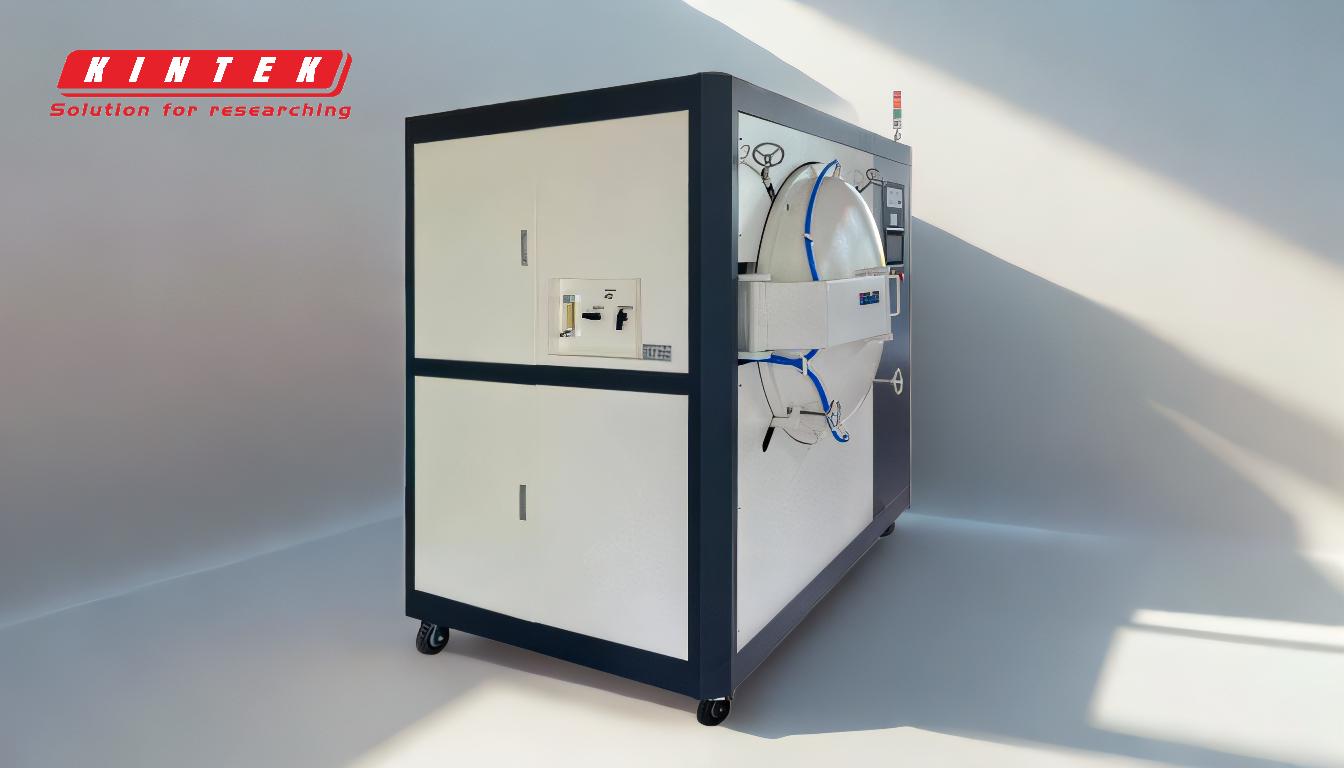
-
Formation of the Green Part:
- The process begins with a powder blend, often mixed with a binding agent (e.g., water, wax, or polymer), which is compacted into a specific shape. This "green" part is weak and oversize but holds the desired form.
- The binding agent ensures the powder particles adhere together during this initial stage.
-
Heating and Binder Removal:
- The green part is placed in a sintering furnace and heated to remove the binding agent. This occurs in the preheat zone of the furnace, where temperatures are high enough to evaporate or burn away the binder.
- This stage is critical for eliminating organic materials and lubricants, ensuring the part is ready for particle fusion.
-
Particle Fusion and Densification:
- In the sintering zone, the temperature is raised to a level just below the melting point of the primary material. This allows particles to bond through solid-state diffusion, forming necks between them.
- The particles fuse at their surfaces, reducing porosity and increasing density. In some cases, an intermediate bonding agent (e.g., bronze) may melt and bond the particles without altering the primary material.
-
Cooling and Final Properties:
- After sintering, the part enters the cooling zone, where controlled cooling solidifies the structure and enhances mechanical properties.
- Shrinkage occurs during this stage, giving the part its final dimensions. The cooling rate can be adjusted to fine-tune properties like hardness and strength.
-
Types of Sintering Furnaces:
- Periodic Kilns: These furnaces process parts in batches, with controlled heating and cooling cycles.
- Tunnel Kilns: Parts move through different temperature zones (preheat, sintering, and cooling) continuously, making them suitable for high-volume production.
-
Benefits of Sintering:
- Produces complex, high-strength parts with minimal material waste.
- Enhances material properties such as density, strength, and wear resistance.
- Allows for precise control over dimensions and mechanical characteristics.
-
Applications of Sintering:
- Widely used in metallurgy for producing metal components like gears, bearings, and filters.
- Essential in ceramics manufacturing for creating durable, heat-resistant products.
- Applied in powder metallurgy to fabricate intricate parts with tailored properties.
By understanding these stages and mechanisms, manufacturers can optimize the sintering process to produce high-quality, cost-effective components for various industrial applications.
Summary Table:
Stage | Description |
---|---|
Formation of Green Part | Powder blend is compacted into a shape with a binding agent. |
Heating & Binder Removal | Green part is heated to remove binders, preparing it for particle fusion. |
Particle Fusion | Particles bond through diffusion, reducing porosity and increasing density. |
Cooling & Finalization | Controlled cooling solidifies the structure, achieving final dimensions. |
Types of Furnaces | Description |
Periodic Kilns | Batch processing with controlled heating and cooling cycles. |
Tunnel Kilns | Continuous processing through preheat, sintering, and cooling zones. |
Benefits | Description |
Enhanced Properties | Improved density, strength, and wear resistance. |
Precision Control | Tailored dimensions and mechanical characteristics. |
Applications | Description |
Metallurgy | Production of gears, bearings, and filters. |
Ceramics | Creation of durable, heat-resistant products. |
Powder Metallurgy | Fabrication of intricate parts with tailored properties. |
Optimize your sintering process with expert guidance—contact us today!