Sintering is a complex thermal process where metal powders are heated just below their melting point, causing the particles to bond and form a solid mass. This process involves several critical stages, including compaction, heating, and cooling, which influence the final properties of the sintered metal. The sintering furnace plays a crucial role in controlling temperature, atmosphere, and pressure to ensure the desired outcomes, such as improved density, hardness, and structural integrity. Different metals, such as stainless steel, titanium, and nickel, undergo unique transformations during sintering, including particle bonding, oxide reduction, and crystallization. Understanding these changes is essential for optimizing the sintering process and achieving high-quality sintered products.
Key Points Explained:
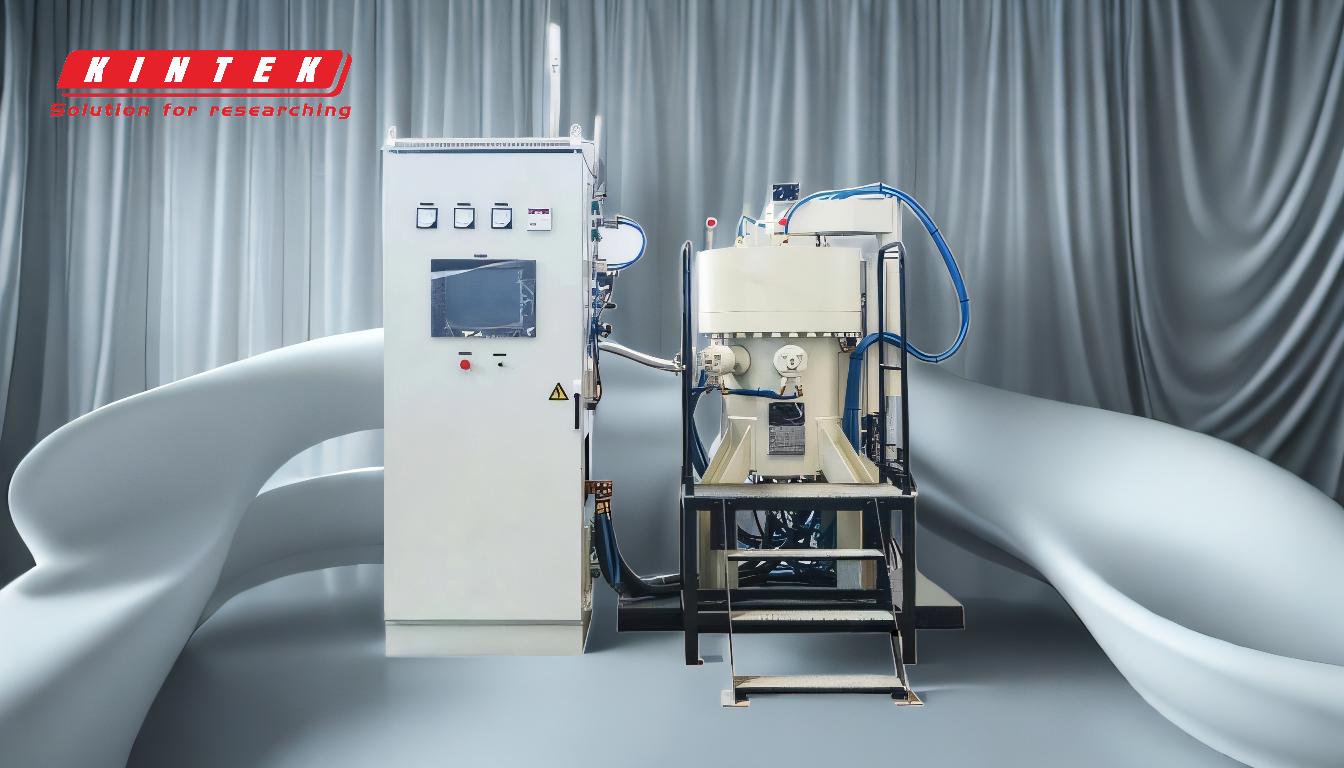
-
Heating Metal Powder Below Melting Point:
- Sintering involves heating metal powders to temperatures just below their melting point. This allows the particles to bond without fully melting, forming a solid mass with improved mechanical properties.
- The sintering furnace is critical in maintaining precise temperature control to ensure uniform heating and bonding of particles.
-
Particle Bonding and Densification:
- During sintering, the metal particles bond through diffusion mechanisms, reducing porosity and increasing density.
- The process often results in slight shrinkage, which must be accounted for in the design of the final product.
-
Oxide Reduction and Atmosphere Control:
- The sintering atmosphere, often a reducing environment, prevents oxidation and promotes the reduction of surface oxides on the metal particles.
- This is essential for achieving strong inter-particle bonds and improving the mechanical properties of the sintered material.
-
Transformation of Phases and Microstructure:
- Sintering can induce phase transformations, such as the conversion of α-Si3N4 to β-Si3N4, which enhances hardness and density.
- However, prolonged sintering times can lead to abnormal grain growth and defects, reducing material performance.
-
Application-Specific Considerations:
- In dental sintering, precise control of temperature, pressure, and atmosphere is crucial to ensure the quality and stability of dental restorations.
- Different metals, such as stainless steel, titanium, and nickel, require tailored sintering conditions to achieve optimal results.
-
Stages of the Sintering Process:
- Compaction: Metal powder is compacted under high pressure to form the desired shape.
- Heating: The compacted metal is heated in a sintering furnace to bond the particles.
- Cooling: The sintered metal is cooled to room temperature, allowing the formation of a stable microstructure.
-
Role of Additives and Binders:
- Additives like copper powder or cemented carbides can be introduced to enhance specific properties, such as strength or wear resistance.
- Binders and liquid additives help fill remaining pores, further improving density and mechanical performance.
-
Impact of Sintering Time and Temperature:
- Increasing sintering time and temperature can enhance density and hardness up to a certain point, beyond which defects may occur due to excessive grain growth.
- Optimal sintering conditions vary depending on the metal and desired properties.
By understanding these key aspects, manufacturers can optimize the sintering process to produce high-quality, durable metal components for various applications.
Summary Table:
Key Process | Description |
---|---|
Heating Below Melting Point | Metal powders are heated just below melting point to bond particles without melting. |
Particle Bonding | Diffusion mechanisms reduce porosity, increase density, and cause slight shrinkage. |
Oxide Reduction | A reducing atmosphere prevents oxidation and strengthens inter-particle bonds. |
Phase Transformation | Induces changes like α-Si3N4 to β-Si3N4, enhancing hardness and density. |
Stages of Sintering | Compaction → Heating → Cooling for stable microstructure formation. |
Additives and Binders | Enhance properties like strength, wear resistance, and fill remaining pores. |
Time and Temperature Impact | Optimized conditions improve density and hardness, but excess can cause defects. |
Want to optimize your sintering process for high-quality results? Contact our experts today!