A batch type furnace is a specialized heating system designed to process materials in discrete batches, making it ideal for applications requiring precise heat treatment, cleanroom standards, or inert atmospheres. These furnaces heat treat components by raising the temperature from room temperature to a predetermined maximum, holding it for a specified duration, and then cooling it at a controlled rate. They are particularly suited for low-volume production, large or complex parts, and processes like deep case carburizing. Batch furnaces are versatile, cost-effective, and can operate with or without a controlled atmosphere, making them a preferred choice for industries requiring tailored heat treatment solutions.
Key Points Explained:
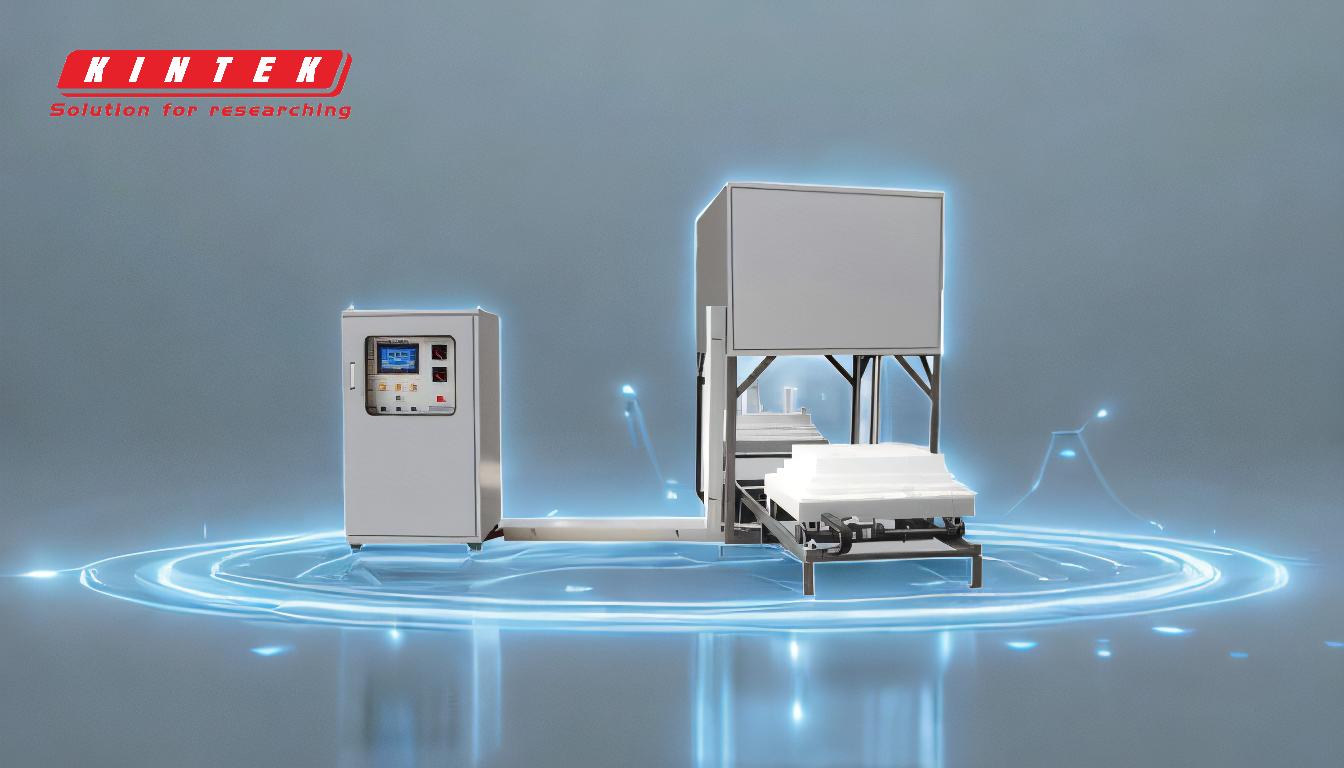
-
Definition and Operation:
- A batch furnace processes materials in discrete batches, charging and discharging the workload as a single unit.
- The furnace is sealed during operation, ensuring no external contaminants enter, making it suitable for cleanroom and inert atmosphere applications.
-
Heat Treatment Process:
- The furnace heats from room temperature to a specified maximum temperature at a controlled rate.
- It maintains the target temperature for a set duration before cooling at a predetermined rate.
- This process ensures consistent and precise heat treatment for each batch.
-
Versatility in Applications:
- Batch furnaces handle varying workloads, including differences in weight, size, material grade, and heat treatment requirements.
- They are ideal for low-volume production, large or complex parts, and specialized processes like deep case carburizing.
-
Types of Batch Furnaces:
- Common types include box furnaces, car-bottom furnaces, integral-quench furnaces, pit furnaces, and vacuum furnaces.
- Each type is designed for specific applications, such as stress-relieving, hardening, or annealing.
-
Temperature Range and Capacity:
- Batch furnaces typically operate between 1200℉ and 2500℉, accommodating a wide range of metals and alloys.
- They can handle parts up to 24 inches in width, making them suitable for large or bulky components.
-
Controlled Atmosphere Options:
- Batch furnaces can operate with or without a controlled atmosphere, providing flexibility for different heat treatment needs.
- Vacuum and protective atmosphere furnaces are common variants, ensuring minimal oxidation or contamination during processing.
-
Cost-Effectiveness:
- Compared to continuous furnaces, batch furnaces are generally less expensive, making them a practical choice for smaller-scale operations or specialized applications.
-
Advantages Over Continuous Furnaces:
- Batch furnaces are better suited for low-volume production and large or complex parts that are difficult to handle in continuous systems.
- They offer greater flexibility in processing diverse materials and heat treatment requirements.
By understanding these key points, equipment and consumable purchasers can make informed decisions about whether a batch furnace meets their specific heat treatment needs.
Summary Table:
Feature | Description |
---|---|
Operation | Processes materials in discrete batches with sealed, contaminant-free operation. |
Heat Treatment | Heats, holds, and cools materials at controlled rates for consistent results. |
Applications | Ideal for low-volume production, large parts, and processes like carburizing. |
Types | Box, car-bottom, integral-quench, pit, and vacuum furnaces. |
Temperature Range | Operates between 1200℉ and 2500℉, suitable for various metals and alloys. |
Atmosphere Options | Can operate with or without controlled atmospheres (e.g., vacuum, inert gas). |
Cost-Effectiveness | More affordable than continuous furnaces for specialized applications. |
Ready to enhance your heat treatment process? Contact us today to find the perfect batch furnace for your needs!