The braze repair process is a specialized technique used to repair cracks, voids, or other defects in metal components, particularly in high-stress or high-temperature applications such as gas turbine engines. This process involves using a filler metal with a lower melting point than the base metal, which is heated to a temperature that allows it to flow into the defect area, creating a strong metallurgical bond upon cooling. Braze repair is widely used in industries like aerospace, power generation, and automotive due to its ability to restore the structural integrity and performance of critical components. It is a cost-effective alternative to replacing damaged parts, especially for expensive or complex components.
Key Points Explained:
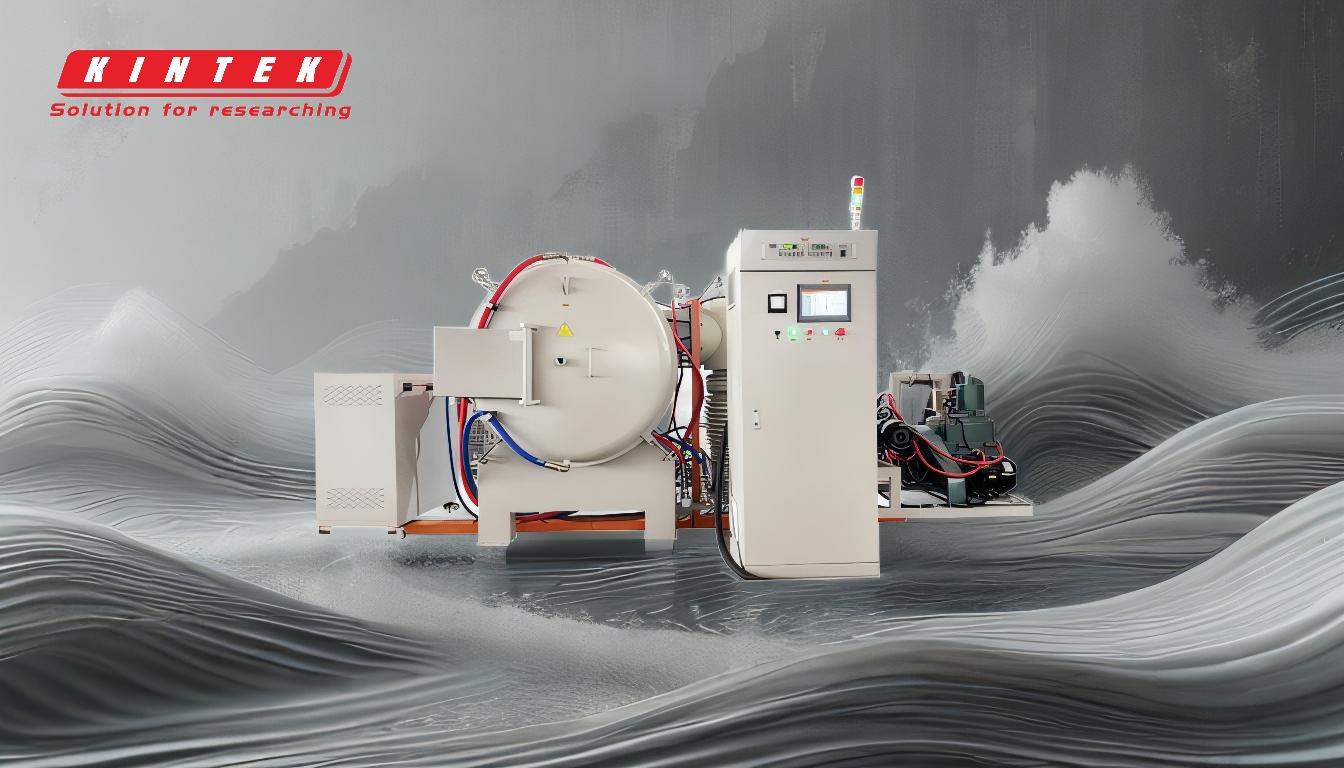
-
Definition and Purpose of Braze Repair:
- Braze repair is a joining process used to fix defects in metal components by filling cracks, voids, or gaps with a filler metal.
- The primary purpose is to restore the structural integrity, functionality, and lifespan of damaged parts, particularly in high-performance applications.
- It is commonly used in industries like aerospace, power generation, and automotive, where component failure can have severe consequences.
-
Materials Used in Braze Repair:
- Base Metal: The material of the component being repaired, often high-temperature alloys like nickel-based or cobalt-based superalloys.
- Filler Metal: A metal alloy with a lower melting point than the base metal, designed to flow into the defect area. Common filler metals include nickel-based, cobalt-based, or silver-based alloys.
- Flux or Atmosphere: Used to prevent oxidation and ensure proper wetting of the filler metal on the base metal.
-
Steps in the Braze Repair Process:
-
Inspection and Preparation:
- The damaged component is inspected to identify the extent of the defect.
- The area around the defect is cleaned and prepared to ensure proper adhesion of the filler metal.
-
Application of Filler Metal:
- The filler metal is applied to the defect area in the form of powder, paste, or pre-placed foil.
-
Heating:
- The component is heated in a controlled environment, such as a vacuum furnace or inert gas atmosphere, to the brazing temperature.
- The temperature is carefully controlled to melt the filler metal without damaging the base metal.
-
Cooling and Solidification:
- The component is cooled slowly to allow the filler metal to solidify and form a strong bond with the base metal.
-
Post-Repair Processing:
- The repaired component may undergo additional processes like machining, heat treatment, or surface finishing to restore its original dimensions and properties.
-
Inspection and Preparation:
-
Advantages of Braze Repair:
- Cost-Effective: Repairing a damaged component is often more economical than replacing it, especially for expensive or complex parts.
- Restores Performance: Braze repair can restore the mechanical properties and performance of the component, extending its service life.
- Versatility: Suitable for a wide range of materials and applications, including high-temperature and high-stress environments.
-
Applications of Braze Repair:
- Aerospace: Repairing turbine blades, vanes, and other engine components.
- Power Generation: Fixing cracks in gas turbine components and heat exchangers.
- Automotive: Repairing exhaust systems, turbochargers, and other high-temperature parts.
-
Challenges and Considerations:
- Material Compatibility: The filler metal must be compatible with the base metal to ensure a strong bond and avoid issues like cracking or corrosion.
- Process Control: Precise control of temperature, heating rate, and cooling rate is critical to achieving a successful repair.
- Inspection and Quality Assurance: Post-repair inspection is essential to ensure the repair meets the required standards and specifications.
By following these steps and considerations, the braze repair process can effectively restore damaged components, ensuring their continued performance and reliability in demanding applications.
Summary Table:
Aspect | Details |
---|---|
Purpose | Fix defects in metal components, restoring structural integrity and performance. |
Materials | Base metal (e.g., nickel-based alloys), filler metal (e.g., silver-based alloys), flux or atmosphere. |
Steps | Inspection, preparation, filler metal application, heating, cooling, post-repair processing. |
Advantages | Cost-effective, restores performance, versatile for high-stress applications. |
Applications | Aerospace, power generation, automotive. |
Challenges | Material compatibility, process control, inspection, and quality assurance. |
Need expert advice on braze repair for your metal components? Contact us today to learn more!