A furnace refractory is a critical component of industrial furnaces, designed to withstand extreme temperatures and protect the furnace structure from the corrosive and thermal effects of molten materials. It acts as a working liner, directly interfacing with the molten aluminum or other materials inside the furnace. Furnace refractories are typically made from high-temperature-resistant materials such as high-purity alumina fiber, lightweight refractory bricks, and silicon carbide (SiC). These materials ensure durability, thermal insulation, and energy efficiency, making them essential for maintaining consistent process conditions and preventing heat loss. The refractory lining is often constructed using a multi-layer design to enhance performance and longevity.
Key Points Explained:
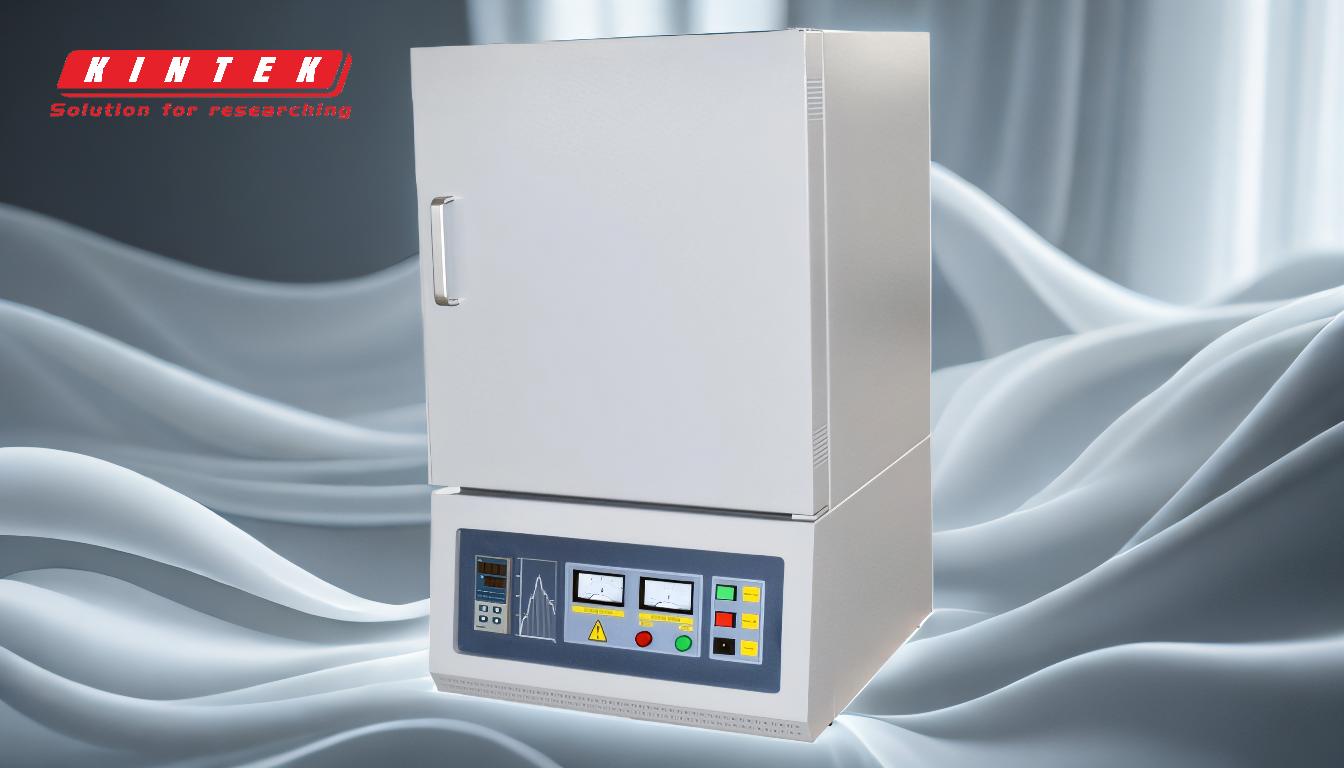
-
Definition and Purpose of Furnace Refractory:
- A furnace refractory is the ceramic lining inside a furnace that directly interacts with molten materials, such as aluminum.
- Its primary purpose is to protect the furnace structure from extreme heat, chemical corrosion, and thermal shock, ensuring the furnace operates efficiently and safely.
-
Materials Used in Furnace Refractories:
- High-Purity Alumina Fiber: This material is vacuum-formed and used for its ability to withstand high temperatures, provide excellent insulation, and resist thermal shock.
- Lightweight Refractory Bricks: These bricks are used for their durability and insulating properties, reducing heat loss and energy consumption.
- Silicon Carbide (SiC): SiC is used in heating rods and refractory linings due to its high strength, thermal conductivity, and resistance to wear and corrosion.
-
Construction and Design of Furnace Refractories:
- Furnace refractories are often constructed using a multi-layer insulation design, combining materials like lightweight alumina ceramic fiber and high-quality insulation boards.
- This layered approach enhances thermal insulation, reduces heat loss, and ensures the furnace operates at optimal energy efficiency.
- The design avoids asbestos components, making it safer and more environmentally friendly.
-
Performance Characteristics:
- High Service Temperature: Refractory materials are designed to operate at extremely high temperatures without degrading.
- Thermal Insulation: The materials used provide excellent insulation, minimizing heat loss and improving energy efficiency.
- Durability: Refractory linings are resistant to cracking, slagging, and thermal shock, ensuring long service life and consistent performance.
-
Applications in Different Furnace Types:
- Holding and Melting Furnaces: Refractory linings in these furnaces are critical for maintaining the temperature and integrity of molten metals.
- Sintering Furnaces: High-purity alumina fiber and Morgan materials brick are commonly used in sintering furnaces for their durability and efficiency in high-temperature environments.
- Muffle Furnaces: These furnaces use high-strength alumina or insulating firebricks to ensure accurate and uniform process conditions.
-
Advantages of Modern Refractory Materials:
- Energy Efficiency: The use of advanced refractory materials reduces heat loss, leading to lower energy consumption.
- Environmental Safety: Modern refractories are asbestos-free, making them safer for both operators and the environment.
- Rapid Heating and Cooling: Materials like high-purity alumina fiber allow furnaces to heat up and cool down quickly, improving operational efficiency.
-
Structural Features of Furnace Bodies:
- Furnace bodies are often constructed with stainless steel shells, which are mirror-polished for durability and aesthetic appeal.
- The design includes various functional components such as electrode holes, suction holes, vent holes, thermocouple holes, and observation holes, all made from stainless steel for strength and corrosion resistance.
By understanding these key points, equipment and consumable purchasers can make informed decisions about selecting the right refractory materials and designs for their specific furnace applications, ensuring optimal performance, energy efficiency, and longevity.
Summary Table:
Aspect | Details |
---|---|
Purpose | Protects furnace structure from extreme heat, corrosion, and thermal shock. |
Materials | High-purity alumina fiber, lightweight refractory bricks, silicon carbide. |
Design | Multi-layer insulation for enhanced thermal efficiency and durability. |
Performance | High service temperature, excellent insulation, and long-lasting durability. |
Applications | Holding, melting, sintering, and muffle furnaces. |
Advantages | Energy efficiency, environmental safety, rapid heating/cooling. |
Optimize your furnace performance with the right refractory materials—contact our experts today!