A vacuum brazing furnace is a specialized industrial equipment designed to join metal components using a brazing process in a vacuum environment. It consists of two main systems: a vacuum system and a heating system. The vacuum system creates and maintains the required vacuum level, while the heating system heats the workpiece and melts the brazing material to form strong, high-quality joints. The process is automated and controlled by temperature instruments, ensuring precision and consistency. Vacuum brazing furnaces are widely used for joining materials like aluminum alloys, stainless steel, titanium alloys, and cemented carbide, as well as for applications such as heat exchangers, ceramic-metal sealing, and tempering.
Key Points Explained:
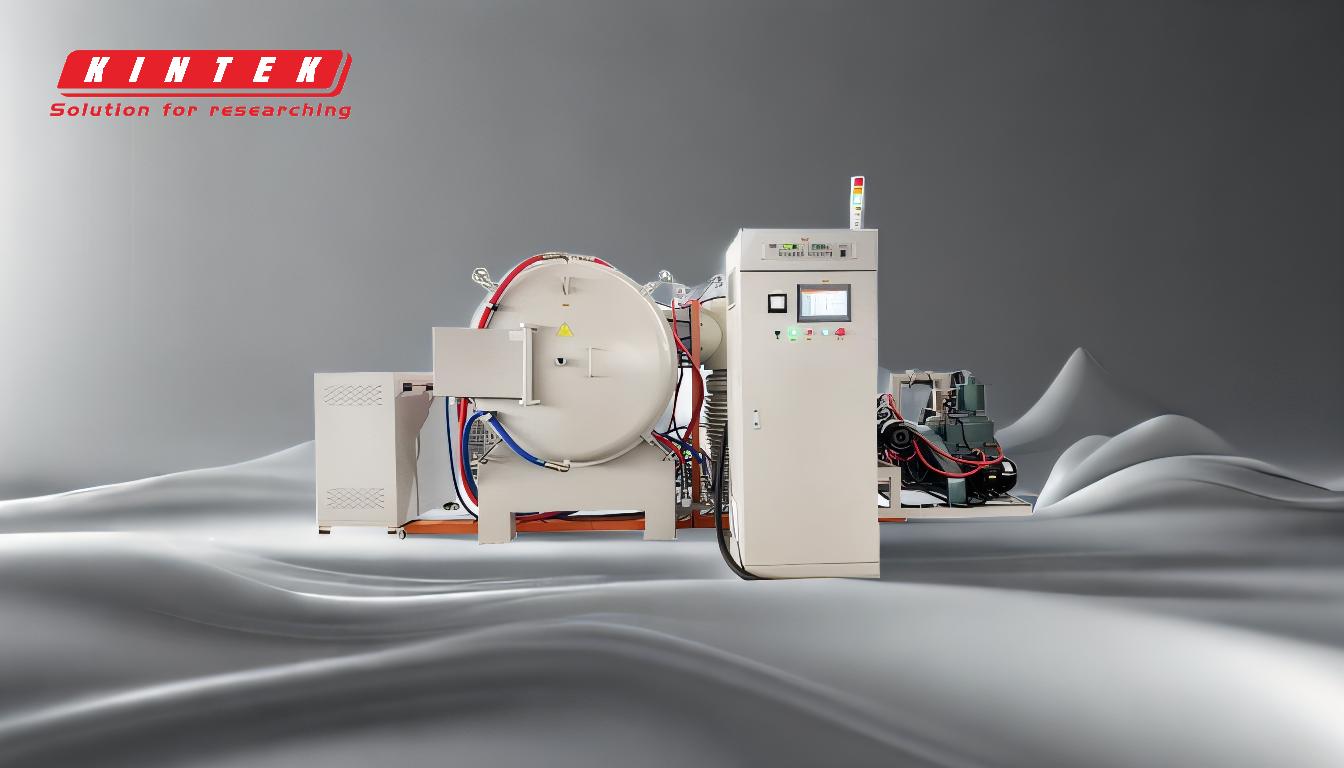
-
Components of a Vacuum Brazing Furnace:
- Vacuum System: This system includes components like vacuum valves, mechanical pumps, diffusion pumps, and Roots pumps. It ensures the creation and maintenance of a high vacuum level, typically up to 7 × 10^-3 Pa, which is essential for preventing oxidation and contamination during the brazing process.
- Heating System: The heating system is responsible for uniformly heating the workpiece and the brazing material to the required temperature, ensuring the filler metal melts and flows into the joints. The temperature is precisely controlled using automated instruments.
-
Brazing Process in a Vacuum Environment:
- The workpiece is placed in the vacuum chamber, and the vacuum system is activated to achieve the desired vacuum level.
- Once the vacuum is established, the heating system begins to heat the workpiece. The brazing material melts and flows into the joints, creating a strong bond.
- After brazing, the workpiece is cooled under vacuum to prevent oxidation and ensure the integrity of the joint.
-
Applications of Vacuum Brazing Furnaces:
- Aluminum Alloy Heat Exchangers: Vacuum brazing is widely used for joining aluminum alloy components in heat exchangers, ensuring leak-free and durable joints.
- Stainless Steel, Titanium Alloy, and Cemented Carbide: These materials are commonly brazed in vacuum furnaces for applications requiring high strength and corrosion resistance.
- Ceramic-Metal Sealing: Vacuum brazing is used to join ceramics and metals, creating hermetic seals for electronic and aerospace applications.
- Vacuum Tempering: The furnace can also be used for tempering materials like bearing steel to improve their mechanical properties.
-
Advantages of Vacuum Brazing:
- Oxidation-Free Joints: The vacuum environment prevents oxidation, resulting in clean, high-quality joints.
- Precision and Consistency: Automated temperature control ensures precise heating and consistent results.
- Versatility: Suitable for a wide range of materials and applications, from heat exchangers to aerospace components.
-
Comparison with Other Brazing Methods:
- Unlike traditional brazing methods, vacuum brazing eliminates the need for flux, reducing contamination and post-brazing cleaning.
- The vacuum environment allows for the simultaneous creation of multiple joints, making it highly efficient for mass production.
For more detailed information on vacuum brazing furnaces, you can visit vacuum brazing furnace. This resource provides additional insights into the design, operation, and applications of these specialized furnaces.
Summary Table:
Aspect | Details |
---|---|
Components | Vacuum system (pumps, valves) and heating system (automated temperature control). |
Process | Workpiece heated in a vacuum to melt brazing material, forming durable joints. |
Applications | Heat exchangers, ceramic-metal sealing, tempering, and aerospace components. |
Advantages | Oxidation-free joints, precision heating, and versatility for various materials. |
Comparison | No flux required, efficient for mass production, and superior joint quality. |
Learn how a vacuum brazing furnace can enhance your production quality—contact us today!