A hydraulic press is a machine that uses liquid pressure to generate a compressive force, widely used in industrial applications such as metal forming, molding, and compression testing. It consists of three main components: the mainframe, power system, and hydraulic control instrument. These components work together to apply high pressure for tasks like shaping materials, pressing components, or testing material strength. An example of a hydraulic press is the hydraulic hot press machine, which is specifically designed for high-temperature applications, such as laminating, vulcanizing, or bonding materials under heat and pressure.
Key Points Explained:
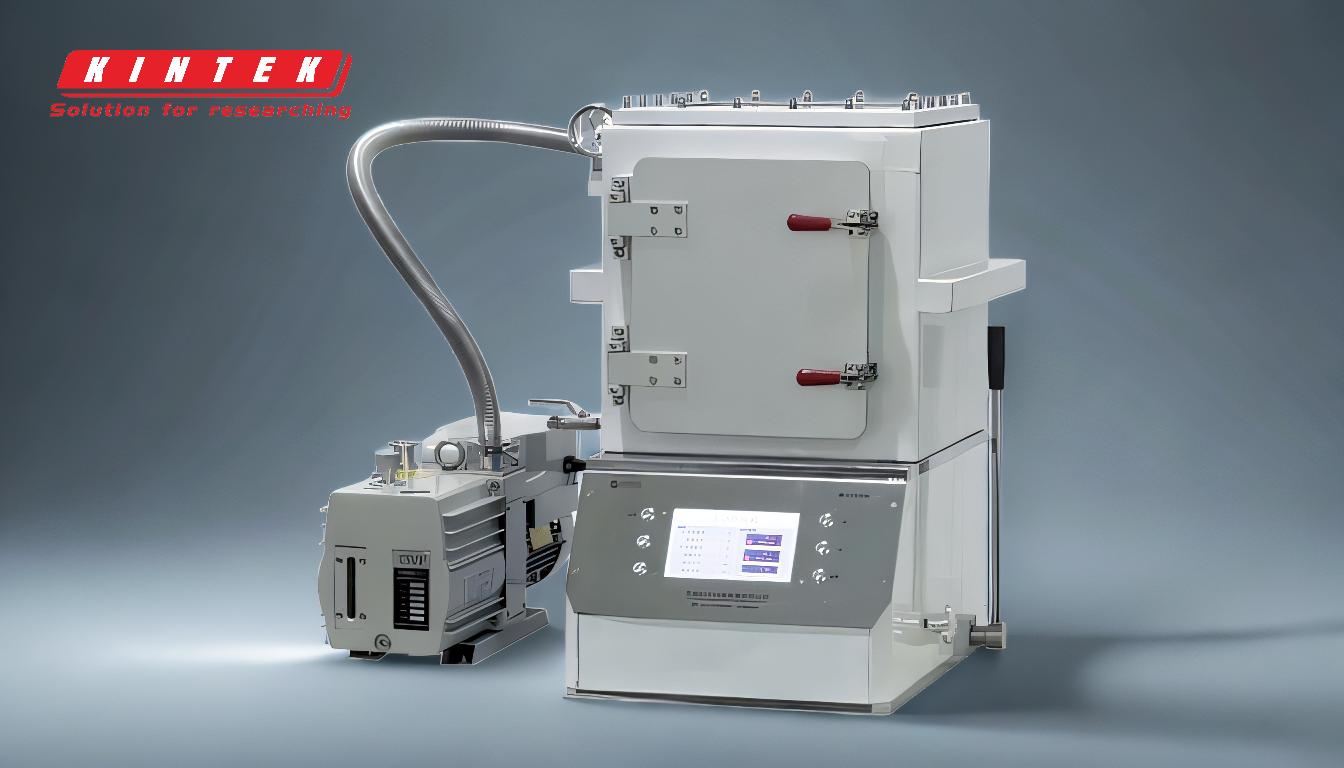
-
Components of a Hydraulic Press
- Mainframe Machine: The mainframe provides the structural support and houses the moving parts, such as the piston and cylinder. It ensures stability and precision during operations.
- Power System: This system generates the force required for pressing. It typically includes a hydraulic pump, motor, and reservoir to store and circulate hydraulic fluid.
- Hydraulic Control Instrument: This component regulates the pressure and flow of the hydraulic fluid, allowing precise control over the force applied during the pressing process.
-
Working Principle
- Hydraulic presses operate based on Pascal's Law, which states that pressure applied to a confined fluid is transmitted equally in all directions.
- When force is applied to a small piston, it creates pressure in the hydraulic fluid, which is then transmitted to a larger piston, amplifying the force.
-
Example: Hydraulic Hot Press Machine
- The hydraulic hot press machine is a specialized type of hydraulic press designed for high-temperature applications.
- It is commonly used in industries like automotive, aerospace, and manufacturing for tasks such as laminating, vulcanizing, or bonding materials.
- This machine combines hydraulic pressure with heat to achieve precise and consistent results, making it ideal for processes requiring both force and temperature control.
-
Applications of Hydraulic Presses
- Metal Forming: Used to shape metals into desired forms, such as bending, stamping, or forging.
- Molding: Applied in plastic and composite molding to create intricate shapes.
- Compression Testing: Utilized to test the strength and durability of materials under high pressure.
- Laminating and Bonding: Used in industries like woodworking and electronics to bond layers of materials together.
-
Advantages of Hydraulic Presses
- High force generation with relatively low energy consumption.
- Precise control over pressure and speed, ensuring consistent results.
- Versatility in handling a wide range of materials and applications.
- Durability and reliability in industrial environments.
By understanding the components, working principle, and applications of hydraulic presses, users can better appreciate their importance in industrial processes. The hydraulic hot press machine stands out as a prime example, showcasing the versatility and efficiency of hydraulic technology in high-temperature applications.
Summary Table:
Feature | Description |
---|---|
Mainframe Machine | Provides structural support and houses moving parts for stability and precision. |
Power System | Includes a hydraulic pump, motor, and reservoir to generate and circulate force. |
Hydraulic Control | Regulates pressure and flow for precise force application. |
Applications | Metal forming, molding, compression testing, laminating, and bonding. |
Advantages | High force, precise control, versatility, durability, and reliability. |
Discover how the hydraulic hot press machine can revolutionize your industrial processes—contact us today!