Brazing is a metal-joining process that involves melting a filler metal and flowing it into the joint between two or more base materials. The filler metal has a lower melting point than the base materials, allowing it to create a strong bond without melting the base materials. A common example of brazing is furnace brazing, which is widely used in industries such as aerospace, automotive, medical, and nuclear. This process is particularly effective for joining complex assemblies and materials that are difficult to weld, such as exotic metals, ceramics, and refractory metals.
Key Points Explained:
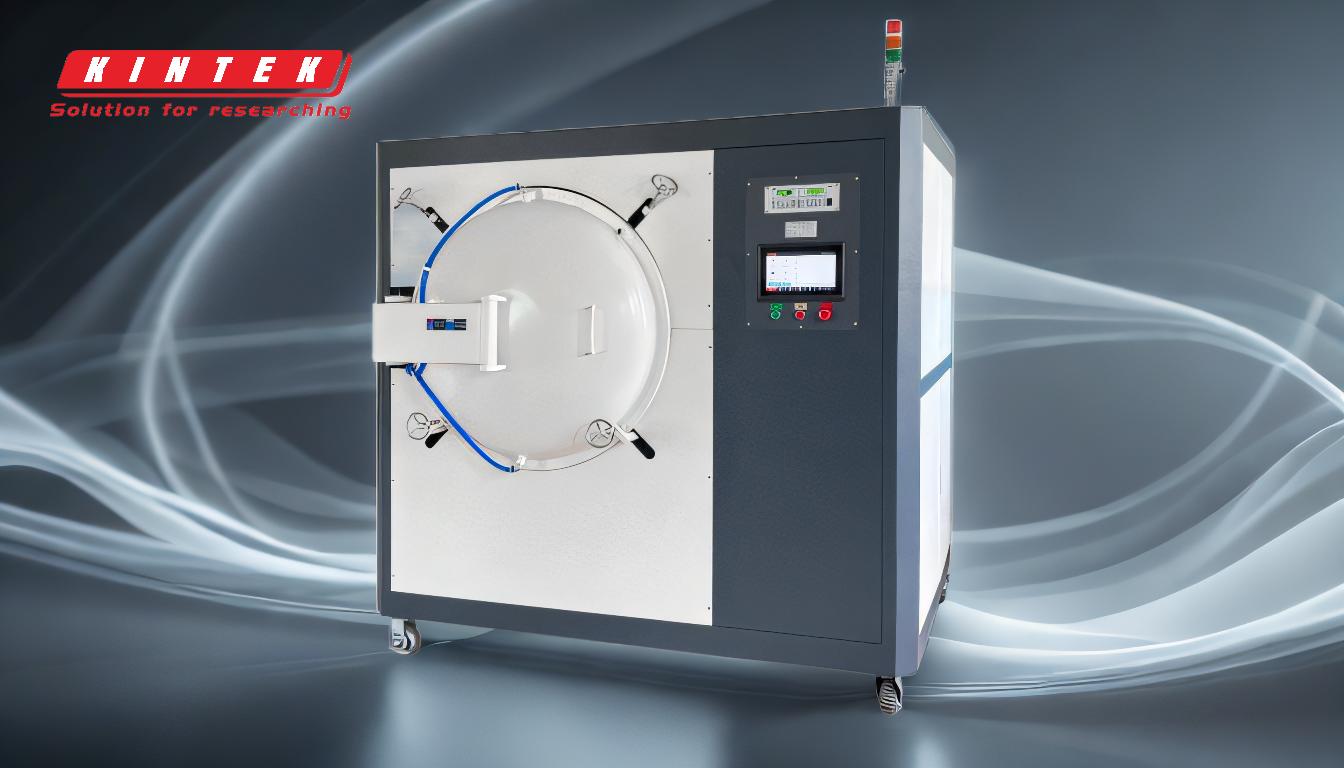
-
Definition of Brazing:
- Brazing is a joining process that uses a filler metal with a lower melting point than the base materials. The filler metal is heated until it melts and flows into the joint, creating a strong bond upon cooling. This method is ideal for joining dissimilar materials and complex assemblies.
-
Furnace Brazing:
- Furnace brazing is a specific type of brazing that takes place in a controlled environment, typically inside a furnace. This method is highly versatile and is used for joining a wide range of materials, including exotic metals like aluminum, titanium, zirconium, niobium, molybdenum, and tantalum, as well as nickel and iron-based alloys, ceramics, and beryllium.
-
Applications of Furnace Brazing:
- Furnace brazing is employed in various industries due to its ability to produce strong, reliable joints. Common applications include:
- Hydraulic fittings: Used in systems that require high-pressure fluid handling.
- Heat exchangers: Essential in industries that require efficient heat transfer.
- Tube manipulations: Used in systems that require precise tube configurations.
- Automotive components: Critical for manufacturing parts that require high strength and durability.
- Medical and scientific equipment: Used in the production of devices that require precision and reliability.
- Aerospace components: Essential for parts that must withstand extreme conditions.
- Industrial gas turbine components: Used in power generation and other industrial applications.
- Space applications: Critical for components that must function in the harsh environment of space.
- Electronic devices: Used in the production of components that require high conductivity and reliability.
- Nuclear components: Essential for parts that must withstand radiation and high temperatures.
- Offshore and petrochemical components: Used in environments that require resistance to corrosion and high pressure.
- Furnace brazing is employed in various industries due to its ability to produce strong, reliable joints. Common applications include:
-
Advantages of Furnace Brazing:
- Versatility: Can join a wide range of materials, including dissimilar metals and ceramics.
- Strength: Produces strong, durable joints that can withstand high stress and temperature.
- Precision: Allows for the joining of complex assemblies with tight tolerances.
- Efficiency: Can be automated for high-volume production, reducing labor costs.
- Reliability: Produces consistent, high-quality joints with minimal defects.
-
Materials Suitable for Furnace Brazing:
- Furnace brazing is particularly effective for materials that are difficult to weld, such as:
- Exotic metals: Aluminum, titanium, zirconium, niobium, molybdenum, and tantalum.
- Nickel and iron-based alloys: Often containing aluminum or titanium.
- Refractory metals: Known for their high melting points and resistance to wear.
- Reactive metals: Prone to oxidation but can be joined effectively in a controlled environment.
- Ceramics: Used in applications requiring high thermal and electrical insulation.
- Beryllium: Known for its stiffness and lightweight properties.
- Furnace brazing is particularly effective for materials that are difficult to weld, such as:
-
Industries Benefiting from Furnace Brazing:
- Aerospace: For components that must endure extreme conditions.
- Automotive: For parts requiring high strength and durability.
- Medical and Scientific: For precision instruments and devices.
- Nuclear: For components that must withstand radiation and high temperatures.
- Offshore and Petrochemical: For equipment that must resist corrosion and high pressure.
In summary, furnace brazing is a versatile and reliable method for joining a wide range of materials, particularly those that are difficult to weld. Its applications span across various industries, making it an essential process in modern manufacturing.
Summary Table:
Aspect | Details |
---|---|
Definition | Brazing uses a filler metal with a lower melting point to join materials. |
Example | Furnace brazing, used in controlled environments for precise, strong bonds. |
Applications | Aerospace, automotive, medical, nuclear, and more. |
Advantages | Versatility, strength, precision, efficiency, and reliability. |
Materials | Exotic metals, ceramics, refractory metals, and beryllium. |
Interested in furnace brazing for your industry? Contact us today to learn more!